Делаем качественный нож из пилы за два с половиной часа
Со стороны кажется, что сделать нож легко, что это лишь заточенная стальная полоса да деревянная ручка. Но когда дело доходит до практики, картина резко меняется. Главное в этом процессе — знание и опыт. Когда знаешь, все просто, когда нет опыта, все сложно.

Недавно я выложил в интернете фотографию с семью клинками, сделанными за один день в стахановском порыве.
Александр Кудряшов в комментарии попросил рассказать, как я делаю ровные и симметричные спуски.
В ответ я пошутил: «Это просто: берешь «волшебный маркер», рисуешь ровные спуски, произносишь чудесные слова, и ровные спуски готовы».
Но шутка ли это на самом деле? Шутка, конечно, но истина где-то рядом.
Позднее я предложил приехать и на практике увидеть, как делаются правильные спуски и весь нож целиком. И это предложение было принято.
По моей задумке Александр должен был сам немного поучаствовать в изготовлении: выбрать заготовку под клинок, материал для рукояти, предпочтительную длину клинка и рукояти. С нашего эксперимента Александр должен был уехать с готовым, добротным, а главное, рабочим ножом.
Приехал Александр нарядный, в светлых штанах песочного цвета и флисовой куртке цвета койот, что совершенно не подходило для предстоящей работы. Пришлось выдать ему рабочие штаны и камуфляжную рубашку на случай, если испачкается. Все подошло идеально — мы с ним одних габаритов.
В мастерской работы пошли по заранее намеченному плану. В качестве материала для клинка была выбрана старая добрая механическая пила из быстрореза. Почему?
Это широко известная и многократно проверенная сталь промышленной закалки. Да, она трудна в обработке, но благодаря красностойкости (способности длительное время выдерживать нагрев без уменьшения твердости) не требует охлаждения.
![]() |
фото: Кудряшова Александра |
Толщина мехпилы 2 мм, этого достаточно для большинства рабочих ножевых задач. Ножи из мехпил легки, хорошо держат заточку и, что немаловажно, полностью легальны: малая толщина клинка отметает любые подозрения на причастность к холодному оружию.
Вообще марок быстрорежущих сталей много, но производитель не всегда указывает конкретную марку, зачастую ограничиваясь клеймом HSS (high speed steel). Новые пилы попадаются редко и стоят дороже.
![]() |
фото: Кудряшова Александра |
Для ножедела новизна мехпилы не имеет никакого значения, поэтому для изготовления ножа можно использовать как новую пилу, так и изрядно поработавшую и даже сломанную. Результат будет мало напоминать исходный материал. Из недостатков можно отметить склонность стали к выкрашиванию при боковой нагрузке и ее подверженность коррозии.
Александр выбрал подходящее полотно мехпилы из быстрореза (HSS made in USSR). Я обрезал лишнее и на наждаке сделал контур будущего ножа, затем обработал заготовку крацовкой — вращающейся стальной щеткой, придав ей благородный черный блеск, и окрасил клинковую часть с двух сторон синим широким маркером, предназначенным для складских работ.
![]() |
фото: Кудряшова Александра |
По краске маркера штангенциркулем разметил линии будущих спусков, уделив особое внимание синхронности их выхода на обух. Полученные линии обвел «волшебным маркером» с серебристой краской, которая есть не что иное, как алюминиевая пудра в полимерной связующей.
Почему именно им? Очень просто. Эта краска выдерживает высокие температуры, хорошо ложится на металл и прочно держится. Краски обычных цветных маркеров при обработке металла выгорают, стираются, осыпаются. А серебрянка держится. Вот и все волшебство.
![]() |
фото: Кудряшова Александра |
Клинок я установил на специальную приспособу для выведения спусков (удешевленный вариант приспособы от Chapay, сделанный самостоятельно из стального уголка). Отметил маркером место, где будут начинаться спуски, и зафиксировал ручными тисками.
Черновой съем металла я выполнял желтым кубитроном II от 3M с зерном Р24 на станке с абразивной лентой (на гриндере). Для равномерности я начинал съем металла от отметки маркером у будущей рукояти и двигался к острию с равномерным несильным нажимом.
![]() |
фото: Кудряшова Александра |
При этом очень важно ровно, параллельно, без перекосов прикладывать к ленте будущий клинок. Я дал Александру немного постоять у станка на начальном этапе, используя специальные приспособления. Вывод спусков — процесс, требующий опыта.
Немного не дойдя до серебристых линий «волшебного маркера», я сменил ленту на абразив Р60 и начал выравнивать линию спусков. Сделал несколько движений от острия к рукояти, создавая прямой угол у начала спусков. Потом уже началась работа над риской спусков.
![]() |
фото: Кудряшова Александра |
Для этого оказалось достаточно работы на абразивах Р80 и Р120. Применять для очень твердых быстрорежущих сталей абразивы Р180 и мельче неоправданно. Это не кубитрон II, и по таким тугим сталям абразивы работают плохо и недолго. При этом важно, чтобы финишная обработка клинка была выполнена на одной ленте, иначе стороны будут выглядеть по-разному.
Нож из быстрореза не требует постоянного охлаждения в процессе обработки, и это один из приятных моментов в его изготовлении. Само собой, нож не стоит перегревать, потому как повышенная температура стали приводит к быстрому забиванию абразива липкими частичками металла — к засаливанию.
![]() |
фото: Кудряшова Александра |
Избыточный прижим металла к абразиву нежелателен по той же причине. Ленту, забитую металлом, которая уже не «грызет», а «лижет», можно освежить. Для этого надо убрать забитые металлом, зализанные вершинки абразива и освободить зерна, лежащие глубже.
Сделать это просто. Нужно взять быстрорезное полотно мехпилы и легко, как напильником, провести им наискосок, навстречу движущейся ленте на месте изгиба (на контактном ролике). Это действие не придаст абразиву первозданную агрессивность, но освежит его и позволит поработать еще.
![]() |
фото: Кудряшова Александра |
После того как первая сторона была выведена в чистовое состояние, я перевернул клинок на приспособе на другую сторону, зафиксировал его и занялся второй стороной. Ее делать всегда труднее, ведь нужно, чтобы она была такой же, как первая.
Кроме того, заготовка видна хуже, больше греется, а контакт с массивной приспособой, выполняющей функцию теплообменника, уже не такой плотный… Однако клинок был готов.
![]() |
фото: Кудряшова Александра |
На войлочном круге с полировальной пастой я исправил следы побежалости металла. Еще раз хочу напомнить, что это была быстрорежущая сталь, твердость которой от нагрева не страдает.
Разметив фломастером места для двух отверстий на хвостовике, я просверлил их шестимиллиметровым перьевым сверлом для кафеля. Надо сказать, что на первом из этих отверстий сверло исчерпало свой ресурс (это было примерно 50-е его отверстие).
![]() |
Без малейшего расстройства я достал из блистера другое дешевое перьевое сверло, досверлил незаконченное первое отверстие и секунд за 40 просверлил второе. Потом сверлом большего диаметра с твердосплавной напайкой снял фаски с отверстий.
А дальше был обед. Подкрепившись рамёном с курицей, приготовленным красавицей-женой, мы приступили к изготовлению рукояти. Для рукояти Александр выбрал палисандр.
![]() |
фото: Кудряшова Александра |
Я обрезал заготовку на ленточной пиле под заданные габариты, приложил к ней хвостовик и просверлил обычным сверлом первое отверстие в деревянной заготовке. Вставил в отверстие шестимиллиметровый штифт, насадил на него отверстие хвостовика и просверлил второе. Отметил маркером, где в рукояти будет край хвостовика, и занялся разметкой для будущей прорези под хвостовик. Пропил под хвостовик выполнил на ленточной пиле.
Я знаю, что конкретное полотно делает пропил шириной 1,5 мм. Мне же был нужен пропил под хвостовик толщиной 2 мм, поэтому я левее заготовки вставил сложенный вдвое лист картона суммарной толщиной 0,5 мм и допилил прорезь до требуемой ширины.
![]() |
фото: Кудряшова Александра |
После этого я занялся приданием заготовке формы рукояти. По замыслу это была прямая рукоять универсального ножа, представляющая в сечении восьмигранник. У меня это был уже не первый нож с восьмигранной рукоятью, которая выглядит строго, но ухватиста, очень удобна и не проворачивается в руке.
Все работы я выполнял на гриндере, используя ленты для дерева. Задал нужные грани и занялся выведением риски с уменьшением зерна абразива. В конце уже вручную выгладил все абразивом скотч брайт, похожим на жесткую плоскую мочалку.
![]() |
фото: Кудряшова Александра |
И вот пришло время монтажа. Измерив толщину рукояти в местах монтажа, я прибавил по 2 миллиметра и отрезал маленьким труборезом кусочки трубочки заданной длины. Хвостовик клинка вставил в прорезь рукояти. Он шел с натягом, так что даже пришлось задействовать ручной реечный пресс (до 600 кг).
Прессом же аккуратно вдавил трубочки в рукоять через хвостовик насквозь. Потом занялся непосредственно развальцовкой.
![]() |
фото: Кудряшова Александра |
Достал набор блестящих шариков от подшипников разного диаметра, положил один маленький шарик на нижнюю площадку пресса, а второй на верхний срез одной из трубочек и растянул края трубочки. Так же поступил и со второй трубочкой.
Выполнял я эту операцию с постепенным увеличением диаметра шариков. Теперь оставалось сделать чистовые операции по развальцовке ювелирным молотком с полированным бойком.
![]() |
фото: Кудряшова Александра |
Банка с натуральным пчелиным воском уже разогрелась на водяной бане. Рукоять ножа отправилась в воск на пропитку и последующее остывание. Пчелиный воск — это натуральный пищевой полимер. Дерево, пропитанное им, не принимает влагу и не скользит в руке.
У меня на кухне все ножи обработаны воском, и им ничего не делается. В воске на водяной бане нож можно держать сколько угодно — хоть час, хоть два, а можно и пять минут.
![]() |
фото: Кудряшова Александра |
Дерево рукояти ножа или приклада ружья всегда хорошо время от времени освежать баллистолом или маслом — льняным, растительным. Альтернативой горячему воску будут натуральные масла, составы на основе латекса, силиконовое масло, специальные масла для дерева (когда-то в Икее продавались), лаки.
У каждого варианта свои плюсы и минусы. Так, недостаток воска состоит в том, что он нежелателен для ножей, при сборке которых применялся клей (он обычно плохо переносит повышенную температуру).
![]() |
фото: Кудряшова Александра |
Натуральные масла долго полимеризуются (навсегда). Баллистол при регулярном применении дает приятную ровную поверхность.
Силиконовые масла не полимеризуются, но хорошо входят в дерево и влагостойки. Лаки выполняют исключительно поверхностную защиту. После остывания воска я снял его излишки с рукояти, отполировал на войлочном круге, а потом вручную бумажной салфеткой.
![]() |
фото: Кудряшова Александра |
Осталось последнее — заточка. Оставлять клинок просто сведенным в ноль нельзя — выкрошится, и это проверено. Нужно сделать небольшой подвод.
Его я делал на российских алмазных брусках (в сторону уменьшения размера зерна), предварительно смочив и натерев их кусочком мыла. Мыльная вода лучше прилипает к камням и лучше смазывает.
![]() |
фото: Кудряшова Александра |
Финишную доводку без нажима кромкой вперед я выполнил с мыльной водой на сланце Green brazilian. Все! Нож бреет. Взяв хорошо высушенное в мастерской тестовое березовое полено (лет 5–6 лежало), я проверил на нем лихим строганием остроту и стойкость режущей кромки, удобство и управляемость ножа.
![]() |
фото: Кудряшова Александра |
Итог: нож склонен злобно зарываться в дерево, режет бодро, в руке удобен, срез дерева блестит, как полированный, а кромка цела и не блестит. В общем, нож можно спокойно отдавать в работу…
![]() |
фото: Кудряшова Александра |
Приятно видеть детский блеск в глазах здорового мужика, разглядывающего новую полезную игрушечку, родившуюся при нем!
Антон Шмидт 11 августа 2017 в 09:52
www.ohotniki.ru
Самодельный нож из пилы по металлу

Всем доброго времени суток !
В данной статье будет рассмотрен способ изготовления ножа, в качестве материала будет использоваться режущее полотно пилы быстрореза .
Приступим к изготовлению !
Берем нашу заготовку и наносим на ней разметку будущей формы клинка. Когда все готово, для удобства зажимаем ее в тиски, и при помощи болгарки с тонким отрезным кругом срезаем лишние части металла по контуру разметки. Для того, чтобы точно подогнать вырезанную форму клинка, согласно нарисованной разметки, нужно дополнительно обработать кромку на наждаке или пройтись по ней зачистным кругом.
Так как поверхность полотна имеет следы ржавчины, которая нам не нужна, убираем ее специальной насадкой для дрели, или же обычной ручной щеткой

После обработки получаем следующее.

Согласно полученной форме клинка на листе бумаги набрасываем будущий дизайн ножа.

Далее изготавливаем больстер для ножа, для этого используем имеющийся кусок латуни, отрезаем деталь нужного размера, затем из полученного куска вырезаем нужную для нас форму.


Затем делаем прорезь для клинка, сверлим отверстия тонким сверлом диаметром 1,8 см, после чего делаем пропил ножовкой по металлу. Далее с обратной стороны рассверливаем прорезь более крупными сверлами, окончательную подгонку делаем при помощи надфилей, так, чтобы хвостовик входил в отверстие с минимальным зазором.


Когда все готово, обжигаем больстер, в данном случае на кухонной плите.


Теперь делаем спуски клинка, для этого используем точило, получилось следующее .


Далее автор использовал болгарку с шлифовальными насадками зернистостью 100 и 600, на которых окончательно довел спуски до желаемого результата. Проводя данную операцию не забываем про технику безопасности, клинок ни в коем случае нельзя ставить против вращения диска, так как это очень опасно и чревато последствиями.


Теперь подбираем древесный материал для рукояти, автор использовал заготовку из фруктовых деревьев, после чего нанес на нее задуманный ранее эскиз, более подробно видно на фото.

Вернемся к нашему больстеру, после того, когда мы произвели обжиг, больстер нужно окончательно зафиксировать на клинке, и скрыть ненужные щели , автором было решено припаять его .
Так как у автора не было достаточно мощного паяльника, он решил использовать другой проверенный способ, с помощью разогретой латунной болванки. Для спайки металла с латунным больстером была взята паяльная кислота , для точной подгонки использовался обрезок от больстера .
Так как больстер нагреть достаточно трудно, была проведена следующая операция – кладем латунную болванку и отрезок от больстера на плиту и нагреваем его, пока эти детали греются, зачищаем место пайки, и наносим паяльную кислоту. Устанавливаем больстер на клинок , затем при помощи нагретой болванки нагреваем его, далее берем предварительно расплавленный оловянный припой и заливаем его в зазор между деталями . Используя латунную болванку и отрезок от больстера постепенной прогреваем детали, таким образом добиваемся равномерного заполнения олова по щелям.
Получаем следующее .

Производим монтаж рукояти ножа.
Для этого берем нашу заготовку , в которой сверлим отверстие, далее при помощи небольшой пилки от лобзика расширяем отверстие. Лишние части рукояти срезаем ножовкой.
Далее фиксируем рукоять при помощи эпоксидной смолы, в которую добавляем опилки .

Кладем ее под пресс, и оставляем сохнуть .

Когда все готово, обтачиваем нашу заготовку, придавая рукояти желаемую форму , для этого автор использовал точильный станок , дрель со шлифовальными насадками, и напильник .
Получаем практически готовый нож .


Автором было решено сделать небольшую доработку, а именно, добавить на рукояти специальный «стеклобой», в качестве материала использовалось все тоже полотно от пилы. Наносим разметку, и вырезаем нашу деталь


Далее делаем паз при помощи ножовки, зазор подгоняем при помощи надфиля.

Затем на рукояти сверлим сквозное отверстие , оно должно совпадать с отверстием на «стеклобое». Когда все готово, ставим «стеклобой» на подготовленное место и фиксируем его цианоакрилатом . В отверстие устанавливаем темлячную трубку.

Нож практически готов, осталось пропитать рукоять льняным маслом, и произвести полировку, а также пошить для него специальные ножны.


Данная статья окончена. Всем спасибо за внимание !
Источник

Получайте на почту подборку новых самоделок. Никакого спама, только полезные идеи!
*Заполняя форму вы соглашаетесь на обработку персональных данных
Становитесь автором сайта, публикуйте собственные статьи, описания самоделок с оплатой за текст. Подробнее здесь.usamodelkina.ru
Нож из дисковой пилы | Мастер-класс своими руками
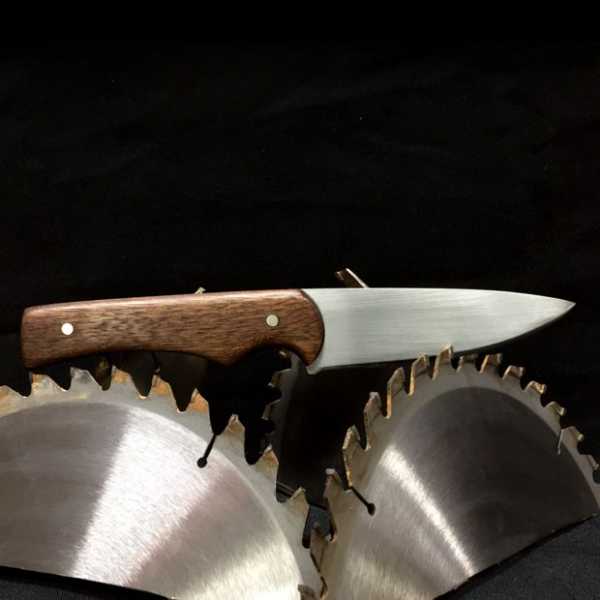
Я решили написать статью о том, как сделать нож. Главная идея заключается в том, что все работы будут проводиться вручную (за исключением сверления и термической обработки). Идея возникла потому, что есть множество статей, где говорится, что для изготовления ножа достаточно иметь под рукой несколько напильников и дрель, или что-то наподобие этого. Мне было интересно узнать, сколько времени займет весь процесс, и не придется ли жульничать и воспользоваться электроинструментами. Создавая нож таким образом я получил прекрасный опыт. Вся работа заняла намного больше времени, чем я ожидал. И по окончанию я проникся новым уважением к людям, которые изготавливают ножи вручную. В целом, я доволен результатом, и надеюсь, что эта статья поможет всем, кто захочет попробовать сделать нож своими руками.
Создание макета ножа

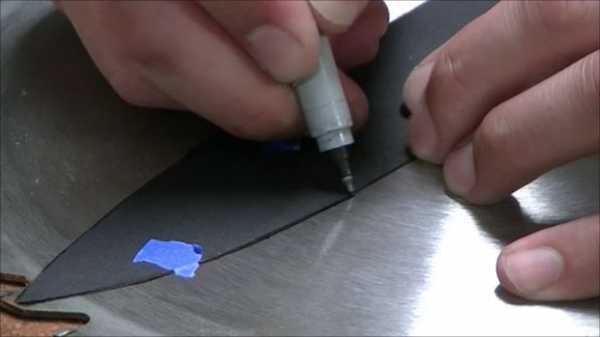

Я попробовал сделать нож максимальной величины, использовав дизайн, контуры которого максимально подходят под размеры диска. Благодаря макету ножа, сделанному мной из плотной бумаги, мне было легко перенести его очертания на поверхность. Для этой процедуры я использовал маркер с тонким стержнем. Это может показаться мелочью, но, по-моему, эта деталь важна. По сравнению с обычным маркером, тонкий оставляет более точную линию. Если линия будет слишком толстой, то при выпиливании заготовки можно будет ошибиться.
Вырезание заготовки

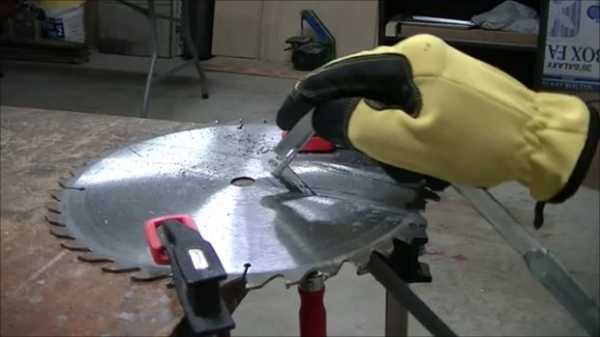

Закрепив диск на рабочем столе, я начал вырезать приблизительную форму лезвия, используя прямые надрезы. Если вы никогда не пользовались ножовкой по металлу, убедитесь, что ее лезвие закреплено правильно, зубья должны быть направлены вперед. Ножовка должна резать при нажиме «от себя».
Выпиливание изгибов

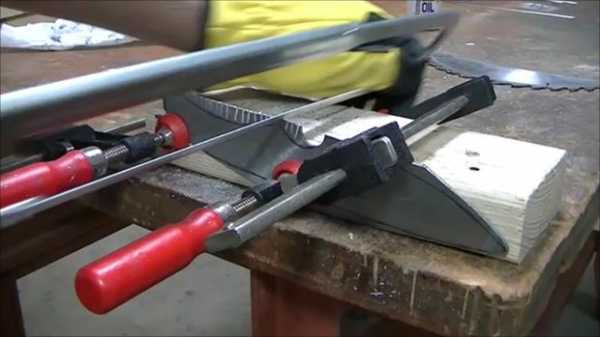


Для того чтобы вырезать изогнутый участок ручки, для удобства пришлось сделать несколько перпендикулярных коротких надрезов вдоль всего изгиба. Затем, работая ножовкой под небольшим углом, я срезал каждый кусок. С помощью коротких надрезов намного легче вырезать изгибы.
Первичная обработка напильником
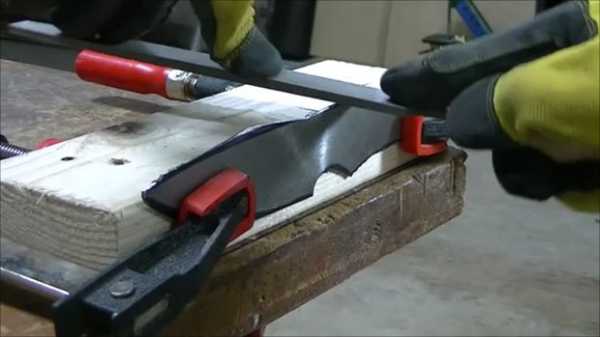



Для улучшения формы заготовки я прикрепил брусок древесины к рабочему столу и зафиксировал на нем лезвие при помощи струбцин. Это позволило обработать края напильником. При этом лезвие было удобно и надежно закреплено. Напильник я использовал еще для определения участков, над которыми нужно больше поработать. Дизайн предусматривал небольшой изгиб обуха, и я прикладывал плоскую часть напильника, чтобы проверить ход работы над этим изгибом. Если бы на обухе был ровный участок, с помощью напильника его можно легко обнаружить.
Придание заготовке окончательной формы



Я использовал несколько видов напильников чтобы максимально приблизиться к форме, выведенной маркером. На этом этапе заготовка начала походить больше на нож и на глаз уже сложней было обнаружить изъяны. Если находилось место, над которым нужно поработать, я корректировал очертание при помощи маркера и затем обрабатывал заготовку до новой линии. Эта линия нужна была, чтобы не перестараться и не испортить дизайн. На последнем фото видно лезвие после придания ему формы при помощи напильника и наждачной бумаги. У меня нет фото, как я шлифую лезвие. На этом этапе были удалены следы, которые оставил напильник. Начинал я с зерна P150 и дошел до P220.
Сверление хвостовика





Изначально я планировал сделать ребро заточки с высокой режущей кромкой, однако мне не захотелось испытывать мои ограниченные способности. Пильный диск изготовлен из достаточно тонкого материала, и мне бы не удалось напильником выточить ребро заточки с режущей кромкой, какое хотелось. К этой теме вернемся позже. На этом этапе я вымерил расположение заклепок, нанес керны и просверлил отверстия при помощи аккумуляторной дрели.
Подготовка к работе с режущей кромкой



Я нанес краску маркером вдоль будущей режущей кромки лезвия. Затем, используя сверло такой же толщины, что и лезвие, я нацарапал отметку точно посередине линии лезвия. На последнем изображении эта линия плохо видна, но она там есть. Эта отметка будет удобной при обработке напильником режущей кромки, чтобы не сделать ее с неровным наклоном.
Формирование режущей кромки

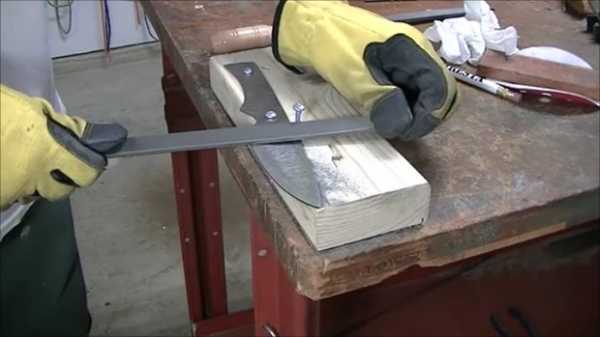


Для формирования режущей кромки я использовал напильник с крупной насечкой, на этом месте я понял, что не обладаю достаточными навыками для ручной выточки ребра заточки. Поэтому я выбрал вариант с более плавным углом, работая напильником от кромки и переходя к обуху. В этом я новичок, поэтому выбрал более консервативный метод снятия припуска. После того как режущая кромка была нормально выточена, я прошелся наждачной бумагой с зерном P220 по всему лезвию.
Готовое лезвие

Вот лезвие после придания формы, обработки напильником, наждачной бумагой. Готовое к термической обработке.
Закаливание




Прежде чем продолжить, я хотел бы отметить, что термообработку можно проводить и на открытом древесном огне, но я бы этого не рекомендовал. Все дело в том, что мне этот способ кажется небезопасным. Поэтому я воспользовался своим мини-горном. Если у вас ничего подобного нет, на самом деле, для термической обработки лезвия можно воспользоваться сторонними услугами. Есть некоторые предприятия, которые готовы выполнить термическую обработку. За деньги, разумеется. Объясню, как я это делал. Развел костер с помощью древесного сырья. В качестве кузнечных мех я использовал фен, присоединенный к трубе. Я включил фен и разогрел уголь до красна. Это не заняло много времени. Я поместил лезвие в костер и нагревал его, пока он не перестало магнититься. Затем закалил его в контейнере с арахисовым маслом. Последнее фото показывает, как выглядит лезвие после закаливания. Несмотря на то, что можно проводить термическую обработку на открытом огне, я ее не рекомендую.
Отпуск




Затем наступило время провести отпуск лезвия. Сперва я очистил наждачной бумагой окалину, которая осталась после закаливания. Я выставил температуру в своей духовой печи на отметке в 190 градусов Цельсия и положил в нее лезвие на 1 час. Час спустя я выключил печь и оставил нож в ней остывать до комнатной температуры не открывая дверь духовки. Можно наблюдать светлый или бронзовый отлив, который лезвие приобретает после отпуска. После этой процедуры я обработал лезвие наждачной бумагой с зерном P220 и затем перешел на P400. На последнем фото я использую наждачную бумагу P400, обвернув ею брусок. Обработку произвожу от хвостовика к острию только в одном направлении. Такая обработка делает поверхность однородной.
Выпиливание заготовки рукояти




Используя лезвие в качестве образца, я нанес очертание рукоятки на деревянном бруске. Рукоять будет из орехового дерева. Здесь снова я воспользовался брусом и струбцинами, и отрезал два куска толщиной в 0,6 сантиметров каждый. В состоянии воодушевления я поторопился с разрезанием дерева. Подожди немного чтобы подумать о порядке действий, и я бы смог выполнить это с меньшими усилиями, и, вероятно, с лучшим результатом. Моей первой ошибкой была обрезка лишней части. Ее можно использовать для зажатия во время резки. Здесь проявилась моя неопытность, и, как следствие, проделан больший объем работы. Хотя, в конечном итоге, и удалось сделать две части, пригодные для рукояти.
Подготовка рукояти к склеиванию



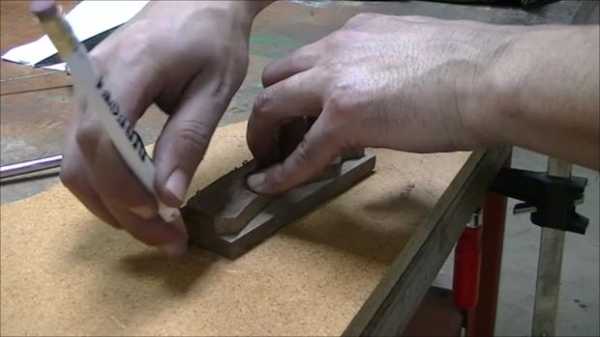

Чтобы рукояти хорошо прилегали к хвостовику после проклейки эпоксидной смолой, при помощи ровной поверхности и наждачной бумаги одну сторону у каждой из частей я сделал максимально плоской. Так точно не будет пробелов после склеивания. На этом месте я также определился с формой рукояти, и чтобы окончательно убедится в этом, я нанес ее примерные очертания. Затем я снова перенес очертания хвостовика на деревянную часть рукояти. Выпилил лобзиком примерную форму на одной из частей, и затем, приложив ее к другой, перенес контур на вторую. Эта операция дала мне возможность сделать примерно одинаковые части, что будет удобным при склейке. На последнем фото изображена примерка, чтобы проверить, все части хвостовика покрываются деревом.
Формирование верхней части рукояти


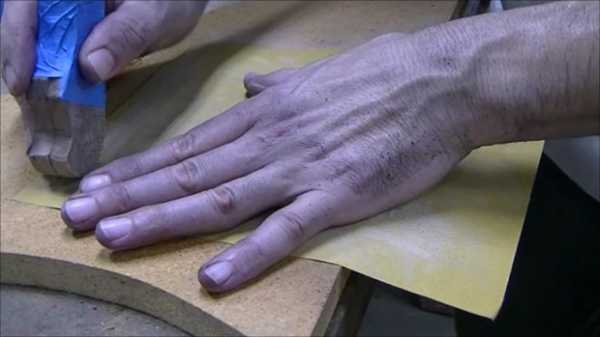

Снова наступило время для работы наждачной бумагой и придания более точной формы. На этом этапе важно окончательно сформировать форму для оковки или верхнюю часть рукояти, потому что после приклеивания, ее будет сложней обрабатывать. А также обрабатывая эти части после склеивания, можно поцарапать клинок. Поэтому я добился окончательного формирования и обработки этой части при помощи наждачной бумаги P800.
Подготовка отверстий для заклепок




Просверлив в дереве одно отверстие для заклепок, я вставил в него сверло подходящего диаметра, чтобы зафиксировать эту ось. Другими словами, это было проделано для фиксации во избежание ошибок при сверлении второго отверстия. Сверление другой стороны рукояти я проделал таким же образом, убедившись, что соответствующие отверстия выстраиваются в одну линию.
Изготовление клепок



В качестве заклепки я использовал стержень из нержавеющей стали диаметром 4,7 миллиметра. Прежде чем наносить слой клея я обработал склеиваемые поверхности ацетоном или алкоголем, для очистки от грязи, пыли или масла.
Нанесение клея



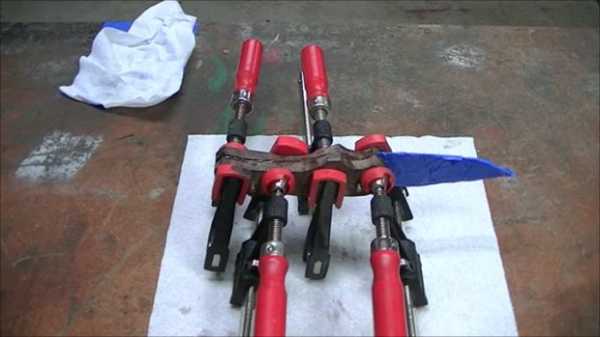
После просыхания, я смешал эпоксидный клей и щедро нанес его на части рукояти и заклепки. Затем я скрепил все при помощи струбцин.
Придание рукояти нужной формы


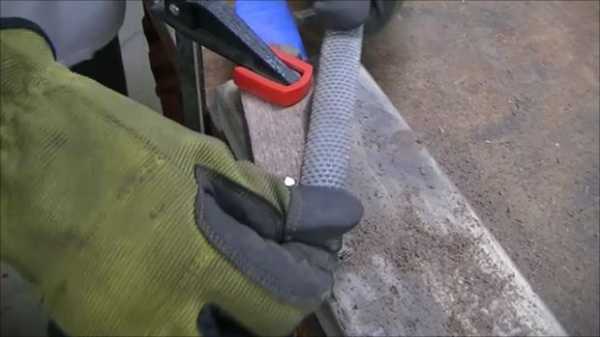

После засыхания эпоксидного клея, я отрезал лишние части заклепок ножовкой по металлу. После этого и приступил к формированию рукояти при помощи рашпиля.
Шлифование рукояти ножа




Рашпилем я придал рукояти примерные очертания. Далее дело оставалось за различными напильниками и наждачной бумагой разной зернистости. Зерно дошло до P600.
Лакирование рукояти

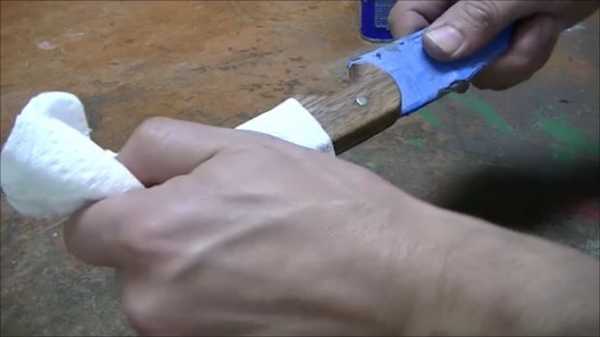

Наконец я привел рукоять в желаемую форму. Прежде чем приступить к лакированию, я очистил ее при помощи ацетона. На рукоять я нанес 5 слоев датского лака.
Заточка клинка


Наконец, я наточил нож об шлифовальный брусок. Он был обернут наждачной бумагой P1000, P1500 и P2000. К нему также был прикреплен кусок кожи. Используя подобный шлифовальный брусок, я могу наточить нож так, что им можно будет бриться.
Готовый нож

Оконченная работа. Хотя процесс был и сложным, награда получилась достойная. Для меня это было что-то вроде обряда посвящения. Процесс изготовления ножа заставляет меняться. Из полученного опыта эти изменения стали моей любимой частью. Я говорю не только о трансформации предметов, но и о личных изменениях. Я овладел новыми навыками и опытом, научился извлекать пользу из собственных ошибок, что определенно сделает меня более лучшим ремесленником. Я надеюсь, что вам будет полезна эта статься, и спасибо, за то, что дочитали ее до конца.
Нож из дисковой пилы своими руками


Я изготовил еще два ножа. Их я делал с использованием электроинструментов. И время, потраченное на изготовление двух ножей, составило одну треть того времени, которое я провел, изготавливая его вручную. На последнем фото видно все ножи вместе.
Смотрите видео изготовления ножа из дисковой пилы своими руками
Original article in English
sdelaysam-svoimirukami.ru
Нож из пилы своими руками: макет, обработка, закаливание
Первые режущие инструменты, изготавливаемые человеком, были сделаны из камня. Предки современных ножей были весьма хрупкими и требовали очень много времени и труда на изготовление. Металлический клинок лишён этих главных недостатков. Сталь обрабатывается сравнительно легко и имеет хорошие физические характеристики.

Нож, изготовленный своими руками, это гордость хозяина. При самостоятельном изготовлении подбираются те характеристики, которые необходимы. В первую очередь — это форма лезвия и рукояти. Наиболее качественные клинки, например булатные или из дамасской стали, делаются методом ковки. Материал клинка при этом имеет необходимую твёрдость и содержание углерода.
Нож из дисковой пилы своими руками
Но ковка требует наличия определённого инструмента и навыков. Что же делать, если хочется изготовить свой, уникальный клинок, но под рукой только минимальный набор инструментов? В этом случае следует обратить внимание на дисковую пилу в качестве заготовки для клинка. Металл, из которого изготовлено полотно дисковой пилы хорошо поддаётся закалке и обладает необходимой упругостью, поэтому пила будет оптимальной заготовкой для изготовления ножа своими руками. Самодельный нож из дисковой пилы хорошо держит заточку, не ломается и может смело составить конкуренцию промышленным ножам.

Нож из дисковой пилы своими руками
Создание макета ножа
Первым делом необходимо создать макет будущего ножа из пилы. На этом этапе работ можно определиться с формой лезвия будущего клинка и формой рукояти. Макет лучше всего изготавливать из плотного картона или тонкой фанеры. Можно использовать и плотный пластик. Жёсткое лекало позволит понять как нож из дисковой пилы будет лежать в руке и насколько удобно им будет пользоваться.
При изготовлении макета важно придерживаться следующих правил:
- Необходимо избегать наличия прямых углов. Прямой угол – место концентрации напряжений. Полотно ножа чаще всего ломается или трескается именно в этом месте.
- Форму клинка необходимо выбирать исходя из назначения будущего ножа. Наиболее универсальны формы с прямым или понижающимся обухом. Такой клинок одинаково хорошо может как резать, так и колоть.
- Размеры макета должны соответствовать размеру полотна дисковой пилы.

Заготовка ножа
При изготовлении макета следует также помнить, что нож можно классифицировать как холодное оружие. Всё зависит от формы и размеров. Изготовление и хранение холодного оружия уголовно наказуемо. Поэтому, чтобы не подпадать под статью уголовного кодекса необходимо, создать макет соответствующий следующим правилам:
- Длина клинка или режущей части не должна превышать 9 сантиметров. Превышение этой длины даже на 1 мм позволит отнести самодельный клинок к холодному оружию.
- Нож, имеющий толщину клинка более 2,6 мм, тоже является холодным оружием. Этим параметром можно пренебречь, так как толщина диска пилы обычно составляет 2 мм.
- Твёрдость не должна быть более 42 единиц. Этот параметр относится к закалке, поэтому так же пропускаем его на этапе изготовления лекала.
- Рукоять должна иметь ограничитель, выступающий за её пределы не более чем на полсантиметра. Если ограничитель отсутствует, то подпальцевая выемка должна быть глубиной менее 4 мм.
После того как макет, удовлетворяющий букве закона и личным предпочтениям, нарисован, можно переходить к переносу макета на диск пилы. Лекало прикладывается к диску пилы и обводится маркером. Лучше всего использовать тонкий маркер. Тонкая линия позволит точнее вырезать заготовку и избежать лишней обработки заготовки напильником.
Вырезание и первичная обработка заготовки
Пилить заготовку быстрее всего болгаркой с тонким отрезным диском по металлу. В случае если нет возможности использования болгарки, то можно воспользоваться ручной ножовкой по металлу. Важно правильно установить пилку в ножовку. Зубы пилки должны быть направлены вперёд и ножовка должна резать при движении «от себя».

Вырезание и подготовка заготовки
Сначала с помощью прямых надрезов выпиливается приблизительная форма ножа. Затем выпиливают загибы. Их проще всего выпиливать несколькими косыми надрезами, сходящимися в одной точке. Важно оставлять припуск 2–3 миллиметра до нарисованного контура. Это связано с тем, что при использовании болгарки металл на месте распила перегревается. Сточив 2–3 мм при помощи напильника и наждачной бумаги можно удалить перегретый край металла.
Придание заготовке окончательной формы
Грубая заготовка до окончательной формы доводится при помощи напильника или наждака. Во избежание перегрева будущего ножа из пилы, при обработке его наждаком, необходимо периодически опускать в ёмкость с водой. Это позволит остыть заготовке. При обработке заготовки с помощью напильника дополнительное охлаждение не требуется. Наиболее оптимально будет приблизительно обработать заготовку на наждаке, а затем провести тонкую доводку напильником.

Обработка заготовки ножа
Во время окончательной обработки следует особое внимание уделять плавности загибов. Важно добиться того, чтобы загиб был ровным, без впадин или выпуклостей. Миниатюрные впадины легко проверить напильником. Для этого с помощью маркера закрашивается проверяемый торец заготовки. Далее, проводят напильником с лёгким нажимом вдоль заготовки по всему загибу. В тех местах, где остался след маркера есть впадины.
Обработка продолжается до того момента, как ни одной впадины не останется.
Далее, заготовка очищается от заусениц и шлифуется с помощью наждачной бумаги. Начинать можно с 60 зернистости и достаточно закончить на 320. Заготовка ещё будет подвергаться термической обработке, поэтому чистовая шлифовка клинка будет позднее.
Сверление хвостовика
Ручку на хвостовике можно закрепить при помощи заклёпок или при помощи клея. Наиболее надёжный вариант крепления ручки заключается в использовании заклёпок. Для их установки необходимо сделать в хвостовике отверстия. Отверстия размечаются на хвостовике так, чтобы они находились примерно посередине будущей ручки. Для того чтобы сверло не соскользнуло на начальном этапе сверления – производят кернение отверстий.
Ввиду того, что дисковая пила изготовлена из легированной инструментальной стали, просверлить её будет не так просто. Обычные свёрла для металла тут долго не проживут.
Сверлить следует кобальтовыми свёрлами или сверлом для керамики, имеющим победитовый наконечник.
В процессе сверления важно добавлять масло в зону сверления и не давать сверлу перегреваться.

Просверленная заготовка
Сверление закалённой стали довольно трудная задача. Поэтому можно изготовить отверстия в хвостовике электрохимическим способом. Для этого к заготовке приделывают провод, затем полностью покрывают хвостовик битумной мастикой или пластилином. В местах будущих отверстий защитный слой процарапывают до голого металла. Далее, готовится насыщенный раствор поваренной соли, в который опускают хвостовик клинка с проводом и ненужную металлическую пластинку тоже с проводом. Оба провода подключаются к аккумулятору или автомобильному зарядному устройству. На будущий нож из дисковой пилы подаётся «плюс», на пластину «минус». Процесс травления сопровождается выделением газа. Через 30–50 минут отверстия будут готовы.
Формирование режущей кромки
Перед тем как приступить к формированию режущей кромки, необходимо провести подготовительную работу. Она заключается в нанесении разметки на кромке заготовки. Разметка размещена ровно по центру и служит ориентиром для изготовления симметричного спуска.
Для этого маркером закрашивается кромка, которая будет режущей и, используя сверло, равное по толщине заготовке, процарапывается разметка. Сверло имеет конусную заточку. Поэтому, если расположить сверло и заготовку на одной плоскости, кончик сверла будет ровно посередине.

Приспособление для нарезания кромки
Затем, используя напильник с крупной насечкой, можно приступить к формированию режущей кромки. При отсутствии должного навыка для создания ровной кромки, можно воспользоваться простым приспособлением. Оно состоит из основания, уголка и направляющей с площадкой для наждачной бумаги. На площадку с направляющей наклеивается наждачная бумага зернистостью 180. В уголке должно быть заранее просверлено несколько отверстий вертикально одно над другим. Нож плашмя закрепляется на основании и направляющая вставляется в отверстие на той высоте, чтобы угол между плоскостью основания и площадкой с наждачной бумагой был таким, который выбрали для формирования спусков. Универсальным является угол от 22 до 30 градусов.
Сделав ровный спуск до середины толщины заготовки, нож переворачивают, дальше делают такой же спуск на обратной стороне. Используя такое нехитрое приспособление, можно легко сформировать ровный клинок.
Готовое лезвие
Таким образом, получается готовое лезвие с заданным углом заточки. Но на данном этапе лезвие готово лишь только условно. Оно не имеет нужной закалки для того, чтобы уверенно держать заточку. А также оно не прошло процедуру отпуска для уменьшения хрупкости. По сути, это полуфабрикат ножа из пилы, которым уже можно пользоваться, но лучше сделать ещё несколько шагов.

Готовое лезвие
Закаливание
Термическая обработка позволит придать ножу необходимую твёрдость, он не будет тупиться в процессе эксплуатации.
Для закалки нож из пилы необходимо нагреть до температуры 750–920 градусов. Если не набрать такую температуру, то сталь не будет закалённой, а если нагреть слишком сильно, то клинок будет излишне хрупким.
В домашних условиях определить точную температуру не представляется возможным. Однако тут есть выход. Для контроля температуры подойдёт простой магнит. Как только заготовка для клинка перестанет магнититься – она нагрета до нужной температуры.
После того как температура заготовки достигла нужных пределов, её необходимо выдержать в таком состоянии примерно 1-1,5 минуты на каждый 1 мм толщины. В случае самодельного ножа из пилы, время выдержки для закалки составляет 3–5 минут. Этого будет достаточно. Дальше заготовка опускается в предварительно подогретое до 50 градусов растительное или машинное масло. Эту процедуру следует выполнять осторожно. Пары масла могут вспыхнуть от раскалённой заготовки, поэтому под рукой необходимо иметь огнетушитель.

Закалка ножа
Немного о горне для закалки. Если воспользоваться промышленным оборудованием не представляется возможным, то горн можно изготовить своими руками. Для этого необходимо развести костёр таких размеров, чтобы была возможность равномерно прогреть заготовку. Далее, как дрова прогорят и появятся угли, на них помещают самодельный нож. В качестве кузнечных мехов можно использовать бытовой фен или насос для накачки матрасов.
Отпуск
После закалки клинок необходимо отпустить. Эта процедура производится с целью снижения хрупкости, а также придания ножу из пилы высокой упругости. Для отпуска клинок очищают наждачной бумагой от окалины, образовавшейся в процессе закалки, и помещают в обычную духовку, разогретую до 190 градусов. Там клинок выдерживается в течение часа, затем подогрев духовки отключают.
Нож должен плавно остыть до комнатной температуры.
После этой процедуры заготовка имеет необходимую твёрдость и упругость.

Отпуск лезвия в духовке
Выпиливание заготовки рукояти и подготовка к склеиванию
Для завершения работы с ножом необходимо изготовить рукоять. Тут могут быть различные вариации материалов, используемых в качестве рукояти. Наиболее популярный материал – это дерево. Деревянная рукоять пропитывается льняным маслом для предотвращения пагубного воздействия на неё влаги.
Выбирается ровная дощечка из дерева понравившихся пород. Толщина дощечки должна быть не менее полсантиметра для удобства. Толстую дощечку можно распилить вдоль. Используя заготовку ножа как лекало, на дощечку наносится разметка, включая отверстия под заклёпки. Для хорошего прилегания будущей рукояти к хвостовику, необходимо вывести плоскость прилегания с помощью наждачной бумаги.

Заготовка рукояти
Формирование верхней части рукояти
Верхняя часть рукояти подготавливается заранее по той причине, что после приклеивания рукояти к хвостовику, обработка верхней части будет затруднена. Также в процессе обработки можно поцарапать лезвие, что крайне нежелательно. По разметке, нанесённой в процессе подготовки, сверлятся отверстия под заклёпки. В них вставляется пруток подходящего диаметра. Он позволяет жёстко соединить обе части заготовки и не даст им сдвигаться в процессе обработки.

Готовая рукоять для ножа
Формирование происходит с помощью напильников и наждачной бумаги. На этом этапе важно помнить про допустимые размеры ограничителя, подпальцевой выемки.
Финальная обработка проводится с помощью наждачной бумаги зернистостью 800. Перед склеиванием все детали необходимо тщательно обезжирить. Это можно сделать ацетоном или растворителем. После высыхания обезжиривателя можно наносить клей или эпоксидную смолу.
Изготовление клепок
Клеевое крепление рукоятки к хвостовику не является надёжным. Во избежание поломки рукояти, деревянные пластины необходимо скрепить клёпками. Клёпки делаются из металла, который не подвержен коррозии. Это могут быть сплавы цветных металлов или нержавеющая сталь. Также в качестве клёпок можно использовать медную или латунную трубку.
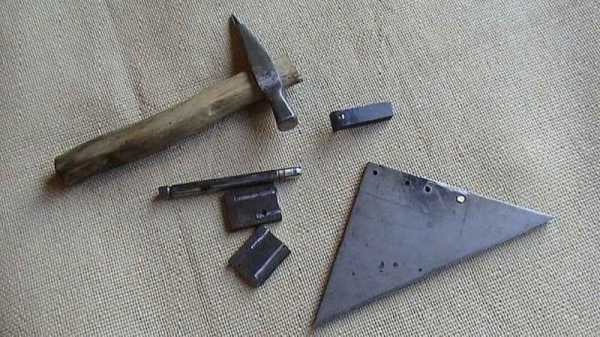
Изготовление клепок для ножа
Из прутка подходящей длины отпиливается заготовка будущей клёпки. Она должна быть на 2–3 миллиметра длиннее толщины рукояти. Зажав клёпку в тисках, с помощью молотка развальцовываем один конец. Должен получиться как бы грибок на одном конце прутка. Далее, клёпка, предварительно смазанная эпоксидным клеем, вставляется в отверстия в ручке и так же развальцовывается с другой стороны рукояти. Для развальцовки клёпки, изготовленной из трубки, лучше всего будет воспользоваться шариком от подшипника.
Придание рукояти нужной формы
После того как клей высохнет, приступают к обработке рукояти. Сначала с помощью надфиля стачивают выступающие части клепки. Затем грубым рашпилем заготовке из дерева придают форму. Сначала формируют профиль рукоятки ножа. Стачивают дерево до момента, пока не будет появляться металл хвостовика. Затем стачивают острые углы и придают рукояти форму, которая хорошо лежит в руке.
Шлифование и лакирование рукояти ножа
Финишная шлифовка производится с помощью наждачной бумаги. Постепенно увеличивая зернистость необходимо убрать все грубые риски от бумаги более крупной зернистости. Достаточно завершить процесс шлифовки рукояти ножа бумагой 600 зернистости. Последним этапом в изготовлении ручки будет её пропитка.
Существует несколько способов пропитки рукояти для её лучшего сохранения. Это пропитка маслами, пропитка воском или покрытие лаком.
Каждый из способов имеет свои преимущества и недостатки. Так, например, воск необходимо предварительно растопить нагрев его, а нагрев пагубно сказывается на прочности клея, которым склеена рукоятка. Масла необходимо периодически обновлять. А лак носит только функцию поверхностной защиты.
Заточка клинка
Финальной чертой при изготовлении ножа из дисковой пилы будет его финишная заточка. Для этого лучше всего использовать шлифовальный брусок, изготовленный из деревянной дощечки. На ровные дощечки наклеивается наждачная бумага зернистостью 1000, 1500 и 2000 по одной зернистости на каждую сторону. Также к дощечке приклеивается кусок кожи для правки заточки. Немного потренировавшись, а так же набравшись навыка можно наточить нож так, что он будет резать бумагу на весу и брить волос.

Заточка клинка
Вот так вот, имея минимум инструмента и навыка, но обладая необходимыми знаниями, можно изготовить отличный нож из дисковой пилы. Характеристики самодельного ножа из дисковой пилы зачастую выше магазинных аналогов в бюджетном сегменте. На диске пилы, после изготовления одного ножа, ещё осталось место? Следует изготовить ещё один нож!
Если вы нашли ошибку, пожалуйста, выделите фрагмент текста и нажмите Ctrl+Enter.
stankiexpert.ru
Делаем качественный нож из пилы за два с половиной часа
Со стороны кажется, что сделать нож легко, что это лишь заточенная стальная полоса да деревянная ручка. Но когда дело доходит до практики, картина резко меняется. Главное в этом процессе — знание и опыт. Когда знаешь, все просто, когда нет опыта, все сложно.

Недавно я выложил в интернете фотографию с семью клинками, сделанными за один день в стахановском порыве.
Александр Кудряшов в комментарии попросил рассказать, как я делаю ровные и симметричные спуски.
В ответ я пошутил: «Это просто: берешь «волшебный маркер», рисуешь ровные спуски, произносишь чудесные слова, и ровные спуски готовы».
Но шутка ли это на самом деле? Шутка, конечно, но истина где-то рядом.
Позднее я предложил приехать и на практике увидеть, как делаются правильные спуски и весь нож целиком. И это предложение было принято.
По моей задумке Александр должен был сам немного поучаствовать в изготовлении: выбрать заготовку под клинок, материал для рукояти, предпочтительную длину клинка и рукояти. С нашего эксперимента Александр должен был уехать с готовым, добротным, а главное, рабочим ножом.
Приехал Александр нарядный, в светлых штанах песочного цвета и флисовой куртке цвета койот, что совершенно не подходило для предстоящей работы. Пришлось выдать ему рабочие штаны и камуфляжную рубашку на случай, если испачкается. Все подошло идеально — мы с ним одних габаритов.
В мастерской работы пошли по заранее намеченному плану. В качестве материала для клинка была выбрана старая добрая механическая пила из быстрореза. Почему?
Это широко известная и многократно проверенная сталь промышленной закалки. Да, она трудна в обработке, но благодаря красностойкости (способности длительное время выдерживать нагрев без уменьшения твердости) не требует охлаждения.
![]() |
фото: Кудряшова Александра |
Толщина мехпилы 2 мм, этого достаточно для большинства рабочих ножевых задач. Ножи из мехпил легки, хорошо держат заточку и, что немаловажно, полностью легальны: малая толщина клинка отметает любые подозрения на причастность к холодному оружию.
Вообще марок быстрорежущих сталей много, но производитель не всегда указывает конкретную марку, зачастую ограничиваясь клеймом HSS (high speed steel). Новые пилы попадаются редко и стоят дороже.
![]() |
фото: Кудряшова Александра |
Для ножедела новизна мехпилы не имеет никакого значения, поэтому для изготовления ножа можно использовать как новую пилу, так и изрядно поработавшую и даже сломанную. Результат будет мало напоминать исходный материал. Из недостатков можно отметить склонность стали к выкрашиванию при боковой нагрузке и ее подверженность коррозии.
Александр выбрал подходящее полотно мехпилы из быстрореза (HSS made in USSR). Я обрезал лишнее и на наждаке сделал контур будущего ножа, затем обработал заготовку крацовкой — вращающейся стальной щеткой, придав ей благородный черный блеск, и окрасил клинковую часть с двух сторон синим широким маркером, предназначенным для складских работ.
![]() |
фото: Кудряшова Александра |
По краске маркера штангенциркулем разметил линии будущих спусков, уделив особое внимание синхронности их выхода на обух. Полученные линии обвел «волшебным маркером» с серебристой краской, которая есть не что иное, как алюминиевая пудра в полимерной связующей.
Почему именно им? Очень просто. Эта краска выдерживает высокие температуры, хорошо ложится на металл и прочно держится. Краски обычных цветных маркеров при обработке металла выгорают, стираются, осыпаются. А серебрянка держится. Вот и все волшебство.
![]() |
фото: Кудряшова Александра |
Клинок я установил на специальную приспособу для выведения спусков (удешевленный вариант приспособы от Chapay, сделанный самостоятельно из стального уголка). Отметил маркером место, где будут начинаться спуски, и зафиксировал ручными тисками.
Черновой съем металла я выполнял желтым кубитроном II от 3M с зерном Р24 на станке с абразивной лентой (на гриндере). Для равномерности я начинал съем металла от отметки маркером у будущей рукояти и двигался к острию с равномерным несильным нажимом.
![]() |
фото: Кудряшова Александра |
При этом очень важно ровно, параллельно, без перекосов прикладывать к ленте будущий клинок. Я дал Александру немного постоять у станка на начальном этапе, используя специальные приспособления. Вывод спусков — процесс, требующий опыта.
Немного не дойдя до серебристых линий «волшебного маркера», я сменил ленту на абразив Р60 и начал выравнивать линию спусков. Сделал несколько движений от острия к рукояти, создавая прямой угол у начала спусков. Потом уже началась работа над риской спусков.
![]() |
фото: Кудряшова Александра |
Для этого оказалось достаточно работы на абразивах Р80 и Р120. Применять для очень твердых быстрорежущих сталей абразивы Р180 и мельче неоправданно. Это не кубитрон II, и по таким тугим сталям абразивы работают плохо и недолго. При этом важно, чтобы финишная обработка клинка была выполнена на одной ленте, иначе стороны будут выглядеть по-разному.
Нож из быстрореза не требует постоянного охлаждения в процессе обработки, и это один из приятных моментов в его изготовлении. Само собой, нож не стоит перегревать, потому как повышенная температура стали приводит к быстрому забиванию абразива липкими частичками металла — к засаливанию.
![]() |
фото: Кудряшова Александра |
Избыточный прижим металла к абразиву нежелателен по той же причине. Ленту, забитую металлом, которая уже не «грызет», а «лижет», можно освежить. Для этого надо убрать забитые металлом, зализанные вершинки абразива и освободить зерна, лежащие глубже.
Сделать это просто. Нужно взять быстрорезное полотно мехпилы и легко, как напильником, провести им наискосок, навстречу движущейся ленте на месте изгиба (на контактном ролике). Это действие не придаст абразиву первозданную агрессивность, но освежит его и позволит поработать еще.
![]() |
фото: Кудряшова Александра |
После того как первая сторона была выведена в чистовое состояние, я перевернул клинок на приспособе на другую сторону, зафиксировал его и занялся второй стороной. Ее делать всегда труднее, ведь нужно, чтобы она была такой же, как первая.
Кроме того, заготовка видна хуже, больше греется, а контакт с массивной приспособой, выполняющей функцию теплообменника, уже не такой плотный… Однако клинок был готов.
![]() |
фото: Кудряшова Александра |
На войлочном круге с полировальной пастой я исправил следы побежалости металла. Еще раз хочу напомнить, что это была быстрорежущая сталь, твердость которой от нагрева не страдает.
Разметив фломастером места для двух отверстий на хвостовике, я просверлил их шестимиллиметровым перьевым сверлом для кафеля. Надо сказать, что на первом из этих отверстий сверло исчерпало свой ресурс (это было примерно 50-е его отверстие).
![]() |
фото: Кудряшова Александра |
Без малейшего расстройства я достал из блистера другое дешевое перьевое сверло, досверлил незаконченное первое отверстие и секунд за 40 просверлил второе. Потом сверлом большего диаметра с твердосплавной напайкой снял фаски с отверстий.
А дальше был обед. Подкрепившись рамёном с курицей, приготовленным красавицей-женой, мы приступили к изготовлению рукояти. Для рукояти Александр выбрал палисандр.
![]() |
фото: Кудряшова Александра |
Я обрезал заготовку на ленточной пиле под заданные габариты, приложил к ней хвостовик и просверлил обычным сверлом первое отверстие в деревянной заготовке. Вставил в отверстие шестимиллиметровый штифт, насадил на него отверстие хвостовика и просверлил второе. Отметил маркером, где в рукояти будет край хвостовика, и занялся разметкой для будущей прорези под хвостовик. Пропил под хвостовик выполнил на ленточной пиле.
Я знаю, что конкретное полотно делает пропил шириной 1,5 мм. Мне же был нужен пропил под хвостовик толщиной 2 мм, поэтому я левее заготовки вставил сложенный вдвое лист картона суммарной толщиной 0,5 мм и допилил прорезь до требуемой ширины.
![]() |
фото: Кудряшова Александра |
После этого я занялся приданием заготовке формы рукояти. По замыслу это была прямая рукоять универсального ножа, представляющая в сечении восьмигранник. У меня это был уже не первый нож с восьмигранной рукоятью, которая выглядит строго, но ухватиста, очень удобна и не проворачивается в руке.
Все работы я выполнял на гриндере, используя ленты для дерева. Задал нужные грани и занялся выведением риски с уменьшением зерна абразива. В конце уже вручную выгладил все абразивом скотч брайт, похожим на жесткую плоскую мочалку.
![]() |
фото: Кудряшова Александра |
И вот пришло время монтажа. Измерив толщину рукояти в местах монтажа, я прибавил по 2 миллиметра и отрезал маленьким труборезом кусочки трубочки заданной длины. Хвостовик клинка вставил в прорезь рукояти. Он шел с натягом, так что даже пришлось задействовать ручной реечный пресс (до 600 кг).
Прессом же аккуратно вдавил трубочки в рукоять через хвостовик насквозь. Потом занялся непосредственно развальцовкой.
![]() |
фото: Кудряшова Александра |
Достал набор блестящих шариков от подшипников разного диаметра, положил один маленький шарик на нижнюю площадку пресса, а второй на верхний срез одной из трубочек и растянул края трубочки. Так же поступил и со второй трубочкой.
Выполнял я эту операцию с постепенным увеличением диаметра шариков. Теперь оставалось сделать чистовые операции по развальцовке ювелирным молотком с полированным бойком.
![]() |
фото: Кудряшова Александра |
Банка с натуральным пчелиным воском уже разогрелась на водяной бане. Рукоять ножа отправилась в воск на пропитку и последующее остывание. Пчелиный воск — это натуральный пищевой полимер. Дерево, пропитанное им, не принимает влагу и не скользит в руке.
У меня на кухне все ножи обработаны воском, и им ничего не делается. В воске на водяной бане нож можно держать сколько угодно — хоть час, хоть два, а можно и пять минут.
![]() |
фото: Кудряшова Александра |
Дерево рукояти ножа или приклада ружья всегда хорошо время от времени освежать баллистолом или маслом — льняным, растительным. Альтернативой горячему воску будут натуральные масла, составы на основе латекса, силиконовое масло, специальные масла для дерева (когда-то в Икее продавались), лаки.
У каждого варианта свои плюсы и минусы. Так, недостаток воска состоит в том, что он нежелателен для ножей, при сборке которых применялся клей (он обычно плохо переносит повышенную температуру).
![]() |
фото: Кудряшова Александра |
Натуральные масла долго полимеризуются (навсегда). Баллистол при регулярном применении дает приятную ровную поверхность.
Силиконовые масла не полимеризуются, но хорошо входят в дерево и влагостойки. Лаки выполняют исключительно поверхностную защиту. После остывания воска я снял его излишки с рукояти, отполировал на войлочном круге, а потом вручную бумажной салфеткой.
![]() |
фото: Кудряшова Александра |
Осталось последнее — заточка. Оставлять клинок просто сведенным в ноль нельзя — выкрошится, и это проверено. Нужно сделать небольшой подвод.
Его я делал на российских алмазных брусках (в сторону уменьшения размера зерна), предварительно смочив и натерев их кусочком мыла. Мыльная вода лучше прилипает к камням и лучше смазывает.
![]() |
фото: Кудряшова Александра |
Финишную доводку без нажима кромкой вперед я выполнил с мыльной водой на сланце Green brazilian. Все! Нож бреет. Взяв хорошо высушенное в мастерской тестовое березовое полено (лет 5–6 лежало), я проверил на нем лихим строганием остроту и стойкость режущей кромки, удобство и управляемость ножа.
![]() |
фото: Кудряшова Александра |
Итог: нож склонен злобно зарываться в дерево, режет бодро, в руке удобен, срез дерева блестит, как полированный, а кромка цела и не блестит. В общем, нож можно спокойно отдавать в работу…
![]() |
фото: Кудряшова Александра |
Приятно видеть детский блеск в глазах здорового мужика, разглядывающего новую полезную игрушечку, родившуюся при нем!
polza-sovet.ru
Мачете из пилы

Этот мачете проектировался и изготавливался для использования в походах. Он пригодится чтобы нарубить сучьев, или высечь какой нибудь кустарник, ветви деревьев, и т.д..
Приступим к изготовлению.
Материал:
1.Старая пила по дереву.
2.Верёвка (2,5-3 м.).

Инструмент:
1.Болгарка.
2.Линейка.
3.Карандаши.
4.Наждачная бумага.
Начнём.
Для начала я начертил вот такой незамысловатый чертёж будущего мачете, который каждый может сделать под себя. Сейчас я вам наглядно покажу как это делать.

К примеру, длина рукоятки должна быть в длину ваших восьми пальцев.

Ширина рукояти должна соответствовать толщине двух пальцев.

Длинна лезвия, от острия до начала рукояти должна быть в длину от вашего сжатого кулака до локтя.

Ширина от начала скругления до острия должна составить 10 см, как ваша ладонь.

На конце рукояти проделываем вот такой выступ, как на фото.

И начинаем вырезать болгаркой по нашему чертежу, соблюдая технику безопасности.

В итоге у нас получилась вот такая заготовка, уже почти похожая на мачете.

С нашей заготовки снимаем все заусенцы по всему контуру, в плоть до мелких выступов.

На болгарку я поставил более толстый диск и зачистил мачете с одной и другой стороны. Лучше всего это сделать при помощи шлифовального станка.

В итоге вот что должно получиться.

Переходим почти к главному процесу, это — ЗАТОЧКА . Затачивать нужно по углом 25 градусов, с одной и другой стороны. Лучше всего это сделать при помощи специального станка.

Вот что у меня получилось. Не судите строго, делаю я это в первый РАЗ.

Затачивать нужно НЕ до самой рукояти, а лишь только отступив 2 см., как на фото.

Я взял мелкую наждачку и финально зачистил наш мачете, практически до блеска. Ещё можно отполировать до изящного блеска на специальном станке.

Как-то так и должно получиться.

В качестве рукояти я задействую небольшой отрезок шнура, длинной в два метра.

Вот сам процесс намотки шнура на рукоять. Для начала сложим вот таким образом как на фото, эту нужно для утолщения рукояти.

С другой стороны делаем так-же самое, к концу рукояти должно образоваться вот такая петля как на фотографии.

Начинаем наматывать шнур, виток к витку, предварительно можно смочить сам шнур, а когда он высохнет он как-бы стянется.

Когда уже намотали шнур, продеваем его в петлю, и делаем один виток.

И тоже продеваем во вторую петлю. И затягиваем.

Оставшеюся петлю нужно очень сильно затянуть, я сделал при помощи ключа. Когда мы затянем петлю наша рукоять из шнура будет очень крепко «сидеть» на ручке.

Оставшийся шнур можно связать в узлы, или сделать какой-нибудь держатель.

В итоге у нас получился вот такой мачете из старой пилы. Этим мачете хорошо рубить кустарник, небольшие сучья, а так-же резать рыбу, мясо и т.д..


Получайте на почту подборку новых самоделок. Никакого спама, только полезные идеи!
*Заполняя форму вы соглашаетесь на обработку персональных данных
Становитесь автором сайта, публикуйте собственные статьи, описания самоделок с оплатой за текст. Подробнее здесь.usamodelkina.ru
Ножи из пилы своими руками
В этой статье, я покажу, как сделать нож своими руками из старого круга пилы своими руками. Главное для ножа — хороший металл. Для этого мы возьмем старый добрый круг для циркулярной пилы. Материал достаточно надежный, может выдерживать высокие нагрузки, не лопается. А что нам еще нужно?
Готовим макет клинка, обрисовываем на металле. Вырезаем будущий клинок. Стачиваем само лезвие, на резаке, как показано на фото.
Приступим к закаливанию. Для этого разжигаем костер в мангале. Добиваемся максимальной температуры, добавляем древесный уголь. Далее держим клинок в самом жаре примерно один час. После чего окунаем раскаленный клинок в воду (специально подготовленная банка).
Далее нам нужно изготовить рукоять, вырезать на держателе средину металла, для более надежной фиксации.
Далее, с помощью наждачной бумаги и прочих инструментов (резаки и т.д.) формируем нормальную деревянную ручку ножа.
Резаком также можно сделать дополнительный орнамент.
Вот собственно и все. Также, было сделано специальную кобуру из кожи, но об этом в следующий раз. Напоследок несколько фото готового изделия.
sdelay.tv