Тепло -и звукоизоляционная штукатурка |
Тепло -и звукоизоляционная стяжка |
Теплая штукатурка представляет собой многокомпонентную сухую смесь на основе цементного вяжущего фракционированного кварцевого песка, гранулированного пеностекла фракции 2-4 мм, извести и комплекса специальных полимерных добавок. Легкая штукатурка применяется для выравнивания поверхностей и создания теплоизоляционных и звукоизоляционных оснований стен из бетона, кирпича, блоков из пено-, керамзито- и полистирол бетонов снаружи и внутри помещений. Используется для утепления внутренних и фасадных стен малоэтажного и высотного строительства. Штукатурка с вспененными гранулами пеностекла обладает рядом преимуществ по сравнению с штукатурками на пенополистироле. Не содержит горючих и токсичных наполнителей и имеет высокий класс пожаробезопасности. Не теряет теплоизоляционныхx свойств на протяжении нескольких десятков лет. |
Легкая тепло -и звукоизоляционная стяжка представляет собой высококачественный материал на основе гранулированного пеностекла фракции 2-4 мм, портландцемента, композитного гидравлического вяжущего и комплекса полимерных модификаторов. Сухая смесь применяется для устройства облегченных выравнивающих тепло эффективных стяжек пола, прочностью не менее 1,5 МПа толщиной нанесения от 20 до 300 мм под жесткие покрытия (керамическая плитка, керамогранит, паркетная доска, ламинат) в помещениях жилых и общественных зданий. Присутствующее в составе смеси пеностекло снижает коэффициент теплопроводности конечного слоя в несколько раз. Стяжка экономит время проведения работ по сравнению с обычными стяжками на пенополистирольной основе. Тепло-звукоизоляционный пол дает минимальную нагрузку на фундаменты и обеспечивает лучшую тепло- и звукозащиту по сравнению с теплоизоляционными бетонами. Экологически чистый материал. В отличие от стяжек на основе пенополистирольных гранул, не содержит горючих и токсичных материалов, может применяться в местах с повышенными требованием к пожаробезопасности. Также используется: |
Подготовка основания: | |
Перед началом работы необходимо очистить основание от грязи, пыли, жиров, масел и масляных и других красок. Для создания адгезионного слоя перед нанесением штукатурки необходимо загрунтовать поверхность. |
Перед началом работы с материалом все трещины, отверстия и выбоины в основании должны быть заделаны. Поверхность очистить от пыли, грязи, масляных и битумных пятен, краски и т.д. Прогрунтовать основание. |
Приготовление раствора: | |
Высыпать содержимое мешка в ведро и налить воды согласно рецептуре, указанной на мешке (450 мл воды на 1кг сухой смеси). |
Высыпать сухую смесь из мешка в ведро и добавить воды, согласно рецептуре прописанной на мешке (300-320мл на 1кг сухой смеси). Перемешать в течение 2-3 минут. Выдержать смесь 3-5 минут и повторно перемешать. Приготовленный раствор рекомендуется использовать в течение 30 минут. |
Применение: | |
На подготовленное (грунтованное) основание нанести слой штукатурного раствора толщиной до 35 мм, набрасывая кельмой или намазывая соколом снизу и разровнять правилом. После начала схватывания раствора его поверхность смочить водой и загладить металлической кельмой, возможно, также затереть раствор теркой. При требуемой толщине более 35 мм штукатурку наносить послойно. Последующее покрытие (краску, декоративную штукатурку и т.д. |
На подготовленное основание установить маяки. Раствор нанести на поверхность толщиной от 20 до 300 мм разровнять правилом по маякам и загладить. Температура нанесения материала должна быть от +5 до +30 °С. Пешее хождение по стяжке возможно через 72 часа. Последующее финишного покрытие наливного пола производится не ранее чем через 7 суток. При укладке керамогранита и керамической плитки не требуется финишный слой наливного пола. Для жестких напольных покрытий (ламината, паркетной доски и мозаичной плитки) рекомендуется заливка финишного слоя наливного пола 7мм, для мягких напольных покрытий (линолеум и ковролин) рекомендуется заливка 10мм. |
Технические характеристики: | |
|
|
Пеностекло и технологии производства пеностекла
В качестве исходных материалов для получения пеностеклянных блоков может использоваться любой тип стекла, диатомит, трепел, цеолиты, глина и другие виды сырья.
Пеностекло из диатомита или трепела
Технологии производства плитного и насыпного пеностекла из диатомита и трепела готовы к промышленному внедрению.
Пеностекло из диатомита или трепела, 190 кг/м3 Foamed glass from diatomite or tripoli, 190 kg/m3 |
Структура пеностекла из диатомита или трепела, 190 кг/м3 The structure of foamed glass from diatomite or tripoli, 190 kg/m3 |
Пеностеклянный гравий из диатомита или трепела, 1-5мм Foamed glass gravel from diatomite or tripoli, 1-5mm |
Пеностеклянный гравий из диатомита или трепела, 5-10мм Foamed glass gravel from diatomite or tripoli, 5-10mm |
Основные характеристики плитного пеностекла из диатомита и трепела
Средняя плотность, кг/м3 | Коэффициент тепло-проводности, Вт/(м·К), не более | Предел прочности при сжатии, МПа (кг/см2), не менее | Водопоглощение по объему, % |
120 | 0,050 | 0,5 (5) | 10 |
175 | 0,063 | 0,7 (7) | 7 |
190 | 0,067 | 0,8 (8) | 5 |
210 | 0,075 | 1,0 (10) | 4 |
265 | 0,090 | 1,5 (15) | 3 |
Основные характеристики насыпного пеностекла из диатомита и трепела
Фракция, мм | Насыпная плотность, кг/м3 | Прочность при сжатии, кг/см2 | Коэфф.![]() |
5 — 10 | 170-300 | 5-40 | 0.048-0,073 |
2,5 — 5 | 210-350 | 5-40 | 0.055-0,085 |
0,63 — 2,5 | 270-450 | 5-40 | 0.066-0.11 |
0,315 — 0,63 | 350-520 | 5-40 | 0.085-0.13 |
Пеностекло из цеолитов
Технологии производства плитного и насыпного пеностекла из природных цеолитов готовы к промышленному внедрению.
Пеностекло из цеолита (Якутия, Сахалин) Foamed glass from zeolite |
Структура пеностекла из цеолита The structure of foamed glass from zeolite |
Пеностеклянный гравий из цеолита, 1-5мм Foamed glass gravel from zeolite, 1-5mm |
Пеностеклянный гравий из цеолита, 5-10мм Foamed glass gravel from zeolite, 5-10mm |
Основные характеристики плитного пеностекла из цеолитов
Средняя плотность, кг/м3 | Коэффициент тепло-проводности, Вт/(м·К), не более | Предел прочности при сжатии, МПа (кг/см2), не менее | Водопоглощение по объему, % |
130 | 0,050 | 0,5 (5) | 5 |
185 | 0,067 | 1,0 (10) | 5 |
245 | 0,085 | 2,0 (25) | 5 |
Основные характеристики насыпного пеностекла из вспененного цеолита
Фракция, мм | Насыпная плотность, кг/м3 | Прочность при сжатии, кг/см2 | Коэфф.![]() |
5 — 10 | 170-300 | 10-40 | 0.048-0,073 |
2,5 — 5 | 210-350 | 15-50 | 0.055-0,085 |
0,63 — 2,5 | 270-450 | 20-60 | 0.066-0.11 |
0,315 — 0,63 | 350-520 | 30-70 | 0.085-0.13 |
Пеностекло из глины
Пеностекло из глины, 230 кг/м3 Foamed glass from clay, 230 kg/m3 |
Структура пеностекла из глины, 230 кг/м3 The structure of foamed glass from clay, 230 kg/m3 |
Пеностекло — Википедия. Что такое Пеностекло
Блок из пеностекла.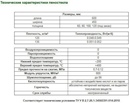
Пеностекло (вспененное стекло, ячеистое стекло) — теплоизоляционный материал, представляющий собой вспененную стекломассу. Для изготовления пеностекла используется способность силикатных стёкол размягчаться и (в случае наличия газообразователя) пениться при температурах около 1000°С. По мере нарастания вязкости при охлаждении вспененной стекломассы до комнатной температуры получившаяся пена приобретает существенную механическую прочность.
История
Считается, что пеностекло было изобретено в 1930-х годах советским академиком И. И. Китайгородским и в США — в начале 1940-х фирмой Corning Glass Work. Вначале предполагалось применять пеностекло в качестве плавающего материала. Но вскоре выяснилось, что оно дополнительно обладает высокими тепло- и звукоизоляционными свойствами, легко подвергается механической обработке и склеиванию. Впервые бетонные плиты с теплоизоляционной прослойкой из пеностекла были применены в 1946 г . при строительстве одного из зданий в Канаде. Этот опыт оказался настолько удачным, что материал сразу же получил всеобщее признание как долговечная изоляция для кровли, перегородок, стен и полов для всех видов построек. Но в СССР широкого распространения оно не получило из-за высокой себестоимости и не отработанной технологии производства этого уникального теплоизоляционного материала.
Так в 1970-х годах пеностекло производилось в СССР на нескольких заводах, но ни на одном из них не выпускалась продукция, способная конкурировать с европейской и американской. Высокая энергоёмкость и большой процент брака неизбежно привели к сворачиванию производства пеностекла на большинстве заводов[источник не указан 1210 дней].
Производство пеностекла
В настоящее время основной технологией производства пеностекла является т. н. «порошковая»: тонкоизмельчённое силикатное стекло (частицы 2 — 10 мкм) смешивается с газообразователем (обычно — углеродом), получившаяся однородная механическая смесь (шихта) в формах, либо на конвейерной ленте поступает в специальную туннельную печь. В результате нагрева до 800—900°С частицы стекла размягчаются до вязко-жидкого состояния, а углерод окисляется с образованием газообразных CO2 и CO, которые и вспенивают стекломассу. Механизм реакции газо- и пенообразования достаточно сложен и не ограничивается только реакцией окисления углерода кислородом воздуха, более важную роль играют окислительно-восстановительные процессы взаимодействия углерода с компонентами размягчённого стекла. Применяют с этой целью отходы обычного стекла или легко спекающиеся горные породы с повышенным содержанием щелочей — трахит, сиенит, нефелин, обсидиан, вулканический туф. В качестве газообразователей применяют каменноугольный кокс, антрацит, известняк, мрамор. Углеродсодержащие газообразователи создают в пеностекле замкнутые поры, а карбонаты — сообщающиеся.[1] Не следует путать пеностекло с продуктами вспенивания водных растворов растворимого стекла. Вспенивание т. н. «жидкого стекла» происходит при температурах около 100—200°С в результате бурного удаления воды из становящегося вязким раствора.
Продукт вспенивания растворимого стекла абсолютно не стоек к действию даже холодной воды, в отличие от пеностекла, химическая стойкость которого сопоставима с исходным листовым или тарным стеклом.
Характеристики
Гранулированное пеностеклоПеностекло выпускают в форме блоков, плит, щебня и гранул. Плотность пеностекла — 110—200 кг/м. куб. Сорбционная влажность пеностекла — 0,2-0,5 %, при ф=97%. Теплопроводность пеностекла — 0,04-0,08 Вт/(м·К) (при +10°С). Паропроницаемость пеностекла — 0-0,005 мг/(м.ч. Па). Предел прочности на сжатие — 0,7-4 МПа. Предел прочности на изгиб — 0,4-0,6 МПа. Температура начала деформации пеностекла — 450°С. Водопоглощение пеностекла 0-5 % от объёма. Шумопоглощение: до 56 Дб. Эффективный диапазон температур: от −260°С до +500°С.[2] Реальный диапазон применения без потери свойств и разрушения пеностекла от −260°С до +230°С
Преимущества
Наряду с отличными теплоизоляционными свойствами и полной экологической и гигиенической безопасностью, пеностекло имеет высокую прочность, негорючесть, удобство обработки и простоту монтажа, способность сохранять эти показатели на протяжении длительного времени постоянными. Материал стоек ко всем обычно применяемым кислотам и их парам, не пропускает воду и водяной пар, не подвержен поражению бактериями и грибками, непроходим для грызунов, не поддерживает горение, не выделяет дым и токсичные вещества.
Применение
Изделия из пеностеклаПеностекло используется главным образом в качестве универсального теплоизолятора: в строительном комплексе; жилищно-коммунальном комплексе; в сельском хозяйстве; энергетике; машиностроении; химической и нефтехимической отраслях; пищевом; бумажном; фармацевтическом и других производствах.
Особенности производства
Производство качественного блочного (плитного) пеностекла (а тем более фасонных изделий из него) справедливо считается весьма технически непростой задачей. Причиной тому является сложность физико-химических процессов непосредственно при вспенивании, а также строгие требования к процессам фиксации и охлаждения (отжига) готовой пены. Так, например, фиксация усложняется тем, что стеклу не свойственно резкое твердение при охлаждении (подобно кристаллизации при переходе воды в лёд), а фиксация пеностекла может сопровождаться такими «мешающими» процессами, как экзотермические реакции в стеклянном расплаве, спонтанная кристаллизация (девитрификация) стекломассы, существенная неоднородность температурного поля во вспененном массиве и т. п. Правильно охладить вспененный блок также непросто — материал обладает крайне низким коэффициентом теплопроводности при известной хрупкости тонких стеклянных ячеек пены. В результате отжиг растягивается на 10 — 15 часов и накладывает существенные ограничения на высоту (толщину) отжигаемых блоков (допустимая скорость охлаждения обратно пропорциональна квадрату толщины). Существенно менее сложным является производство гранулированного пеностекла, массовое производство которого менее требовательно к составу стекла и совершенству теплотехнических агрегатов. Гранулированное пеностекло несколько уступает в теплотехнической эффективности блочному, однако, обладая существенно меньшей ценой, пользуется определённым спросом при производстве лёгких бетонов, выполнении теплоизоляционных засыпок и изготовлении геометрически сложных изделий, включая звукоизоляцию.
Примечания
Производство пеностекла
Пеностекло — высокопористый ячеистый материал, получаемый спеканием тонкоизмельченного стеклянного порошка и газообразователя. В зависимости от технологии производства пеностекло обладает открытой или закрытой пористостью. Пористость различных видов пеностекла колеблется от 8 0 до 95%, размеры пор могут быть от 0,1 до 5 мм. Пеностекло выпускают в виде плит (блоков) размерами (мм) : длина 200-500; ширина 280-500; толщина 80, 100, 120. На российском рынке представлено пеностекло FOOMGLASS Бельгия) и ГомельГЛАСС (Белоруссия).
В зависимости от назначения пеностекло подразделяется на изоляционно-строительное, применяемое для изоляции стен и кровли жилых, общественных и промышленных зданий, изоляционно-монтажное — для утепления установок с отрицательными температурами, промышленного оборудования и трубопроводов, влагозащитное с водопоглощением не более 2% по объему, легкое для изоляции строительных конструкций и оборудования и гранулированное для засыпной теплоизоляции и как наполнитель пено-пластов. Влагозащитное пеностекло, применяемое в условиях глубокого холода, имеет замкнутые поры.
Пеностекло характеризуется высокой прочностью, хорошими тепло- и звукоизоляционными свойствами, водостойкостью, негорючестью, биостойкостью, низкой теплопроводностью. Теплоизоляционное пеностекло легко поддается механической обработке — пилению, сверлению, шлифованию. Пеностекло можно изготовлять окрашенным в различные цвета и оттенки: от белого до черного. Теплоизоляционное пеностекло -хороший теплоизоляционный материал для стен и перекрытий различных строительных сооружений, а также для изоляции промышленных холодильников и технологического оборудования, работающего при отрицательных температурах, например хранилищ сжиженных газов. Прочность, легкая обрабатываемость, негорючесть создают благоприятные условия для его применения в строительных конструкциях.
Для производства пеностекла используют стекломассу, сваренную из следующих исходных материалов: кварцевого песка, известняка, соды и сульфата натрия. Можно также использовать отходы стекольного производства — стекольный бой или бой стекла следующего химического состава (%): SiО2 — 60-72; СаО-4,5-6; MgO — 1,5-3,5; Na2 О — 13-15; А12О3 — 0 ,8-2; Fe2O3 — 0-2,5; SO3 — 0,4-0,5.
Стекломассу, сваренную в ванной печи, превращают в гранулы. Для этого ее сливают на металлический конвейер и обильно орошают водой.
В качестве газообразователей применяют следующие материалы (% от массы стекла) : антрацит — 1,5-2; кокс — 2-3; торфяной полукокс; известняк или мраморную крошку — 1-1,5; ламповую сажу — 0,2-0,5.
Порошковый способ изготовления пеностекла
Тонко измельченное в порошок стекло с добавкой газообразователя нагревают до 700-850°С; выделяющийся при такой температуре газ вспенивает размягченное стекло. В процессе порообразования вся масса представляет собой пластичную вязкую смесь, в которой равномерно распределен газообразователь, а выделяющийся газ создает устойчивую и равномерную стекольную пену. Образовавшаяся высокопористая структура закрепляется быстрым твердением стекла в процессе охлаждения изделия. Затвердевшее пеностекло отжигают, а затем подвергают механической обработке.
Если в качестве сырья используют бой и отходы стекольного производства, то эти материалы дробят в щековой дробилке, промывают в боемойке и сушат в барабане. После этого стекло измельчают в молотковой дробилке.
Шихту, состоящую из стекломассы и газообразователя, готовят в шаровых двухкамерных мельницах непрерывного действия, где ее дополнительно измельчают до удельной поверхности 6000-7000 см2/г и перемешивают. Чем меньше частицы стеклянного порошка, тем однороднее поры и тем они равномернее распределены в материале. При этом материал получается более прочным. Тонкость помола определяют остатком порошка при просеивании на сите с 10 000 отв./см2; остаток должен быть не более 10% от массы порошка. При более тонком помоле увеличивается расход энергии на помол. Производительность мельницы 1200 кг/ч.
Таблица 4.37
Характеристика теплоизоляционного пеностекла
Показатели |
Пеностекло | ||||
изоляционно-строительное |
изоляционно-монтажное |
влагозащитное |
легкое |
гранулированное (зерна 5-40 мм) | |
Плотность, кг/м3 |
160-250 |
130-160 |
140-180 |
100-130 |
100-140 |
Теплопроводность при температуре 25°С, Вт/ (м* °С) |
0,07-0,086 |
0,058—0,07 |
0,06-0,07 |
0,042-0,055 |
0,04-0,055 |
Объемное водопоглощение, % |
5-15 |
2-5 |
1-2 |
15 |
8 |
Прочность, МПа: на сжатие на изгиб |
0,8-2,0 0,8-1,0 |
0,5-0,8 0,3-0,4 |
1,0-1,5 0,6-0,7 |
0,25-0,6 |
0,1-0,3 |
Предельная температура применения, °С |
— |
От-180 до+400 |
Основная технологическая задача в производстве пеностекла — вспенивание стекольной шихты, в результате чего материал приобретает ячеистое строение. Для вспенивания применяют формы из жаростойкого металла, состоящие из одинаковых полуформ. Нижняя полуформа имеет выдвижное днище, облегчающее извлечение блоков. Перед засыпкой шихты внутренние поверхности форм смазывают составом, приготовленным из каолина, асбеста и воды соответственно в соотношении 2:1:1 (мас. ч.) . Это обеспечивает хорошую выемку блоков из формы. Наполненные шихтой формы поступают в печь вспенивания, где нагреваются до температуры, необходимой для размягчения стекла и разложения или сгорания газообразователя и выделения газа.
Печи вспенивания длиной 18, 6 м и шириной около 3,5 м, относящиеся к туннельным, имеют три зоны: подогрева и вспенивания; резкого охлаждения и стабилизации. Зона подогрева и вспенивания длиной около 10 м снабжена шестью парами горелок; зона резкого охлаждения имеет длину 1,2 м; зона стабилизации длиной около 4 м снабжена четырьмя парами горелок. Отапливаются печи газом или жидким топливом. Формы с шихтой, установленные в один ряд по высоте и в два или три по ширине, перемещаются на роликовом конвейере или на специальных ползунах по металлическим направляющим. При выходе из печи из форм извлекают блоки, которые передают в печь отжига, а формы снова загружают шихтой и направляют в печь для вспенивания.
Топки расположены под подом печи и покрыты сверху металлическими жаростойкими плитами, через которые нагреваются днища форм. С целью обеспечения постоянной заданной температуры в зонах вспенивания и стабилизации горелки расположены в шахматном порядке.
Для отжига блоки устанавливаются на сетчатый конвейер и направляются в конвейерную печь (лер) длиной 30 м и шириной в свету 1,8 м. В печи отжига блоки располагают вертикально (на ребро) в решетчатые кассеты по три в ряд по ширине конвейерной сетки. Скорость движения сетки 0,0 6 м/мин. Общая продолжительность отжига 10 ч, скорость снижения температуры по длине печи отжига 0,5-1°С/мин.
Опиловка готовых блоков производится на конвейере , снабженном по краям дисковыми алмазными пилами. Упаковка блоков осуществляется в деревянную решетчатую тару, куда они укладываются на торец, в один ряд по высоте, по семь блоков в ряду. Хранение пеностекла предусматривается в крытых неотапливаемых складах.
Рассмотренная технология, состоящая из вспенивания и отжига в различных печах, называется двух-стадийной. Для вспенивания и отжига применяют также одностадийную технологию производства пеностекла в туннельной печи. На вагонетку устанавливается 20 форм по пять рядов по высоте без перевязки. В каждую форму засыпается шихта.
Общее время вспенивания и отжига 21-22 ч. Температурный режим характеризуется быстрым подъемом температуры до 800-830°С, непродолжительной выдержкой при наивысших значениях температуры и значительным периодом отжига пеностекла, который заключается в его медленном охлаждении. Благодаря отжигу происходит равномерное сокращение объема блоков, что предохраняет их от вредных напряжений и растрескивания.
Конвейерный способ производства пеностекла
Способ заключается в том, что материал спекается без форм на пластинчатом конвейере из жаростойких элементов или из металлической жаростойкой ленты в печи вспенивания. При выходе из печи от непрерывно движущегося бруса отрезают куски определенной длины, которые автоматически подаются в печь отжига. Чтобы придать плитам из пеностекла точные размеры и товарный вид, их подвергают механической обработке на опиловочных или шлифовальных станках, которые оборудованы пылеотса-сывающими устройствами. Режут плиты на маятниковых или каретных пилах.
Двухстадийный способ производства пеностекла наиболее совершенный по сравнению с одностадийным и конвейерным, так как пеностекло получается высокого качества при хороших технико-экономических показателях.
Для снижения плотности и получения легкого пеностекла вспениванию подвергают гранулированную пенообразующую смесь, полученную путем гидратации стеклянного порошка. Продолжительность нагрева и вспенивания при этом сокращается. Такой способ приготовления пенообразующей смеси расширяет сырьевую базу, так как позволяет использовать в качестве сырья отходы стекольного производства и утильный стеклобой. Основное технологическое оборудование (мельницы, печи вспенивания и отжига) остается без изменений. При вспенивании такой гранулированной пенообразующей смеси получают гранулированное пеностекло во вращающихся печах.
ПРОИЗВОДСТВО ТЕПЛОИЗОЛЯЦИОННЫХ ПЛАСТМАСС (ПЕНОПЛАСТОВ)
Теплоизоляционные материалы на основе пластмасс изготовляют из различных полимеров. Наибольшее значение для тепловой изоляции в строительстве и промышленности имеют пенопласты, полученные на основе полистирольных, полиуретановых, феноло-формальдегидных, мочевиноформальдегидных и полихлорвиниловых полимеров (смол). Пенопласты характеризуются высокими теплоизоляционными свойствами в сочетании с хорошими прочностными показателями.
По строению они имеют преимущественно замкнутые поры. Их называют газонаполненными пластмассами, так как технология получения пенопластов основана на вспенивании полимеров газами, которые образуются либо в результате химических реакций между составляющими материал компонентами (химический способ), либо выделяются при разложении минеральных и органических газообразователей или при испарении жидкого вспенивающегося вещества.
Свойства пенопластов в зависимости от вида полимера и способов производства колеблются в широких пределах: плотность 10-150 кг/м3; теплопроводность при температуре (20±5) °С — 0,023-0,052 Вт/ (м- °С) ; прочность 0,05-4,0 МПа; объемное водопоглощение 2-70%. Пенопласты по горючести относятся к категории трудногорючих (фенолоформальдегидные) и горючих. Последние могут быть самозатухающимися — при удалении пламени перестают гореть (например, некоторые пенополиуретаны, полихлорвиниловые).
Пенопласты широко применяют для изоляции трубопроводов и оборудования, утепления строительных ограждающих конструкций, в холодильной технике. Особенно высок экономический эффект от их использования в области глубокого холода. Температура применения пенопластов в зависимости от вида смолы находится в пределах от -180 до +150°С.
Применение пенопластов для изоляции трубопроводов и оборудования значительно повышает теплотехническую эффективность и индустриальность теплоизоляционных конструкций, что позволяет на 10-15% снизить тепловые потери, повысить производительность труда в два раза и улучшить санитарные условия работ на монтаже.
ПОЛИСТИРОЛЬНЫЙ ПЕНОПЛАСТ
Полистирольный пенопласт (ГОСТ 15588) представляет собой формованный плитный материал, который состоит из склеенных между собой частиц-гранул вспененного суспензионного (зернистого) полистирола. Каждая изолированная частица не сообщается одна с другой и состоит из ячеек, содержащих газ или смесь газов и разделенных тонкими стенками полимера. Частицы полистирола похожи на бисер, поэтому такой материал называют бисерным полистиролом. Из полистирольного пенопласта изготовляют плиты, а также полуцилиндры.
Плиты выпускают двух видов: ПСБ-С — с добавкой антипирена и ПСБ — без антипирена. Плиты с добавкой антипирена не должны поддерживать самостоятельного горения в течение более 5 с после удаления источника огня. Выпускают также полуцилиндры только с добавкой антипирена. Размеры плит (мм) : длина 900-2000 с интервалом 50 мм; ширина 500-1200 с интервалом 50 мм; толщина (высота) 25, 33, 50 и 100. Размеры полуцилиндров (мм) : длина 1000; толщина 50-90.
Технология. Производство изделий из полистирола характеризуется тем, что при нагревании выше 80°С полистирол переходит из стеклообразного состояния в эластичное, а порофор (газообразователь, входящий в состав гранул полистирола) при температуре выше 2 8°С переходит из жидкого состояния в газообразное.
Под давлением газа размягченные гранулы полистирола увеличиваются в объеме в 10-20 раз. Степень увеличения размера гранул зависит от температуры нагрева и становится максимальной при температуре 95-100°С. Теплоносителем служит горячая вода, пар или нагретый воздух.
Технология производства пенополистирола состоит из двух основных стадий: предварительное вспенивание, после которого материал сохраняет зернистое сыпучее состояние, и окончательное вспенивание в форме, в процессе которого гранулы склеиваются между собой. Технологию производства выполняют периодическим и непрерывным способами формования.
Исходное сырье — суспензионный вспенивающийся полистирол — поступает на склад сырья в мешках или контейнерах, где хранится при температуре не ниже +10°С. С помощью пневмотранспорта полистирол направляется в расходный бункер, а затем — в предвспениватель.
Предварительное вспенивание, проводимое для снижения плотности изделий и сокращения продолжительности вспенивания, осуществляется в шнеко-вых или барабанных аппаратах.
Шнековый аппарат имеет винтовой конвейер, заключенный в паровую рубашку, шнековый дозатор с бункером, редуктор и электродвигатель. Суспензионный полистирол подается из бункера через дозатор на винтовой шнек, где перемещается до выходного отверстия. В конвейер одновременно через отверстия в корпусе подается пар под давлением около 0,1 МПа, который нагревает полистирол до температуры 95-102°С. Время вспенивания 1-2 мин. Производительность шнекового аппарата до 2,5 м3/ч в зависимости от свойства полистирола.
По такому же принципу гранулы полистирола вспениваются в вертикальном барабанном аппарате, снабженном лопастной мешалкой с частотой вращения 60 мин»1. Днище барабана обогревается паром, который подается одновременно с гранулятом в нижнюю часть рабочего объема предвспенивателя. Гранулят, перемешиваясь и нагреваясь, вспенивается и поднимается вверх, вытесняемый непрерывно поступающим более тяжелым, еще не вспененным гранулятом. Температура в аппарате 92-100°С. Предварительно вспененные гранулы полистирола через разгрузочное окно поступают во второй барабан, где материал подсушивается горячим воздухом температурой 4 0°С. При небольшом объеме производства применяют вспениватели периодического действия, например ванны с водой, подогретой до 95-98 °С.
После предварительного вспенивания гранулы полистирола охлаждаются и выдерживаются не менее 16 ч для выравнивания давления с окружающей средой; одновременно материал подсушивается при температуре не более 40°С. Так как предварительное вспенивание обеспечивает получение насыпной плотности гранул не менее 15 кг/м3, применяют иногда повторное вспенивание, позволяющее снизить плотность до 10 кг/м3.
Окончательное вспенивание полистирола производится в перфорированных стационарных формах из алюминия или нержавеющей стали, куда через специальные отверстия подается пар.
Формы могут быть и передвижными. Такие формы с засыпанным полистиролом собирают в пакет и направляют в автоклав, куда подается пар, и изделия нагреваются до температуры 95-100°С. Окончательное вспенивание продолжается 1-2 мин. После вспенивания изделия охлаждают в течение 10 мин.
Данный способ формования изделий называется периодическим. В последние годы широкое распространение получает формование полистирольного пенопласта периодическим способом в крупногабаритных формах, в которых изготовляют блоки размерами около 4×1х0,5 м. После загрузки полистирола крышку формы закрывают и подают сухой насыщенный пар в течение 130 с. Применение влажного пара обусловливает увеличение цикла пропаривания. Под действием пара предварительно вспененные гранулы, помещенные в замкнутый объем, нагреваются, дополнительно расширяются и сплавляются между собой, образуя изделие с равномерной ячеистой структурой.
Общая продолжительность процесса спекания гранул полистирола в блок 4-5 мин при температуре 102-112°С. По окончании пропаривания блок охлаждается в течение 45-55 мин в зависимости от плотности получаемого пенополистирола. В процессе охлаждения происходит выравнивание давления внутри блока с окружающей средой.
После охлаждения блока крышка формы открывается с помощью гидроцилиндров и готовый блок с помощью гидротолкателей выталкивается из формы. После вылеживания в течение двух суток блоки поступают на пост резки, где с помощью нагретых металлических проволок или полос разрезаются на плиты и полуцилиндры требуемых, размеров.
Резка полуцилиндров на конвейерной установке с ленточными копирами (нихромовая лента толщиной 1-2 мм) производится в такой последовательности: на направляющие устанавливается плита (блок) пенопласта, которая под действием захватов перемещается, входит в соприкосновение с нагретой нихромо-вой лентой копира и разрезается на несколько полуцилиндров заданных размеров. Ролики обеспечивают плотное прижатие плиты к базовой поверхности копира. Напряжение на зажимах нихромовой ленты можно регулировать от 0 до 12,5 В; максимальная сила тока 140 А; температура ленты — 350-480°С.
Отходы, образующиеся после резки на изделия, поступают на дробилку по переработке отходов, откуда крошка подается в бункер и вводится в качестве добавки в формуемый блок. Непрерывное формование производят на конвейерных линиях, в пакетных формователях, карусельных машинах. Технология производства состоит из тех же операций, что и при периодическом способе формования. Пенопласт получается в виде непрерывной ленты толщиной 50-100 мм или в виде блоков объемом 0,3 м3.
Машина для непрерывного формования полистирольного пенопласта состоит из горизонтального конвейера, который образует формующий желоб с тремя зонами (загрузки, формования, охлаждения). Из бункера гранулы винтовым конвейером загружаются на непрерывно движущуюся со скоростью до 18,5 м/мин ленту. Проходя зону формования, полистирол вспенивается под воздействием пара температурой 105-120°С. Из формовочной зоны материал поступает в зону охлаждения, где охлаждается воздухом до температуры 40°С. Затем плиты разрезают по длине и ширине пилами. Вся установка автоматизирована и обслуживается тремя операторами. Производительность машины 18-20 м3/ч.
Пакетный формователь состоит из 24 форм, передвигающихся в вертикальной шахте снизу вверх. Форма заполняется предварительно вспененными гранулами, и вспенивание осуществляется перегретым паром температурой 103-112°С в течение 1 мин. Перемещаясь на высоту одной формы, изделие поступает в зону охлаждения. Время охлаждения около 20 мин. Производительность пакетного формователя 3 м3/ч. Кроме вспенивания полистирола, в формах или на непрерывных линиях применяют способ вспенивания полистирола непосредственно в полости строительных конструкций — стеновых или кровельных панелей. Гранулы нагреваются паром или токами высокой частоты, а затем охлаждаются до температуры 40°С.
Оборудование для производства полистирольного пенопласта ООО «СтройМеханика»
Процесс вспенивания ПСВ гранул условно можно разделить на два этапа: предварительное вспенивание; высушивание (вылеживание) вспененных гранул для их дальнейшего использования. Описание оборудования по этим этапам приведено в разделе «Технология пенополистиролбетона».
Производство блоков полистирола. Формовочный агрегат представляет собой стальную конструкцию прямоугольной формы с двойными стенками. Внутренние стенки перфорированы по всей поверхности для обеспечения возможности поступления пара.
Технологический цикл функционирования формовочного агрегата протекает следующим образом. Закрываются двери и затворы камеры, подается пар для ее разогрева. Открывается спускной клапан с последующим сливом конденсата. Открывается верхний борт, и в формовочный агрегат загружается порциями материал. После чего он герметично закрывается.
Далее в камеры подается пар, при этом линия слива конденсата должна быть обязательно открыта, что дает возможность пару пройти через всю толщу материала и одновременно со сливом конденсата произвести формовку. Содержание линии слива конденсата в открытом состоянии позволяет стабилизировать давление на значении, близком к атмосферному. Это, в свою очередь, обеспечивает оптимальное распределение пара по всему объему материала.
Перекрывается линия слива конденсата. Снова подается пар, и агрегат выводится на рабочее давление (ориентировочно 0,5 кгс/см2) , по достижении заданной величины давления начинается отсчет времени, предусмотренного для стабилизации материала.
Линия слива конденсата открывается, и конденсат пара сливается. При этом давление внутри камеры приводится в соответствии с давлением снаружи ее. Время открывания линии сброса используется также как время охлаждения блока. Открываются двери. Блоки извлекаются из агрегата, взвешиваются и удаляются из рабочей зоны. По истечению кратковременного периода охлаждения блоки укладываются в склад для хранения на период, длительность которого зависит от области применения продукции, которая будет изготавливаться из этого материала.
По завершении вызревания блок подлежит резке на листы различной толщины. Для проведения этих операций используется установка для резки. С помощью разогретых струн диаметром 0,5 мм выполняется резка блока по высоте от 0 до 400 мм. Присутствие незначительного количества дыма обусловливается неверной установкой скорости реза и температуры струны. Скорость резки определяется плотностью, шириной реза и диаметром струны, которые в этом случае составляют 0,5 мм.
В непосредственной близости от установки рекомендуется постоянно держать в наличии огнетушители с двуокисью углерода.
Складирование плит пенополистирола должно осуществляться согласно п. 5.7 ГОСТ 15588. При формировании пакетов должны соблюдаться требования ГОСТ 21929 и ГОСТ 24510.
Блок-форма для производства пенопластовых блоков 2050х1050х500 входит в комплект технологического оборудования для стендового производства плит из полистирола и предназначена для изготовления блоков полистирольного пенопласта путем термоформования предварительно вспененных гранул полистирола.
Работа с блок-формой осуществляется следующим образом. В полость формования блока засыпаются гранулы пенополистирола. Установка закрывается и в полости бортов подается водяной пар, который через перфорации в стенках вступает в контакт с предварительно вспененными гранулами полистирола. Под действием водяного пара гранулы повторно вспениваются (увеличиваются в объеме) и вследствие замкнутого объема спрессовываются (спекаются) . По окончании цикла формования установка охлаждается водой, подаваемой в полости бортов, раскрывается, блок извлекается и транспортируется на технологическое вылеживание. В блок-форме единовременно формуется только один блок.
Технические характеристики блок-формы
Габаритные размеры, мм:
блок-формы ………………………………………. 2200х1600х1250
получаемого блока ………………………………. 2050х1050х500
Технологический цикл, мин ………………………………… 10
Производительность, м3/ч…………………………………… до 5
Максимальное давление внутри установки, кПа …. до 50
Блок-форма для производства пенопластовых блоков 1050x1050x500 также, как и предыдущая, входит в комплект технологического оборудования для стендового производства плит из полистирола и имеет тоже предназначение.
Технические характеристики блок-формы
Габаритные размеры, мм:
блок-формы …………………………………….. 1230х1600х1250
получаемого блока………………………………. 1050х1050х500
Технологический цикл, мин ……………………………………… 10
Производительность, м3/ч……………………………………… до 2,5
Максимальное давление установки, кПа…………………. до 50
Водокольцевой вакуумный насос типа ВВН предназначен для удаления (откачки) водяного пара из блок-формы с целью ускорения процесса ее распалубки. Рабочая жидкость — вода.
Проточная часть водокольцевых вакуумных насосов типа ВВН изготавливается, в зависимости от исполнения, из чугуна, титана, коррозионностойких сплавов, углеродистой стали. В рабочем пространстве агрегата отсутствуют трущиеся части.
Зазоры между вращающимся ротором и неподвижным корпусом уплотнены водяным кольцом. Мощность привода насоса 7,5 кВт.
Станок для продольной резки блока пенополистирола. Состав устройства: металлическая конструкция с рабочей поверхностью; механизм подачи блока пенополистирола; тележка металлическая; устройство для продольной резки блока пенополистирола. Для работы одного стола необходим трансформатор, который предназначен для нагрева режущий проволоки. Для одновременной работы двух и более столов требуется трансформатор соответствующей мощности.
Технические характеристики
Количество одновременных резов ……………………………… 10
Шаг реза, мм …………………………………………………………….. 10
Напряжение, В ………… ………………………………………. 220/380
Потребляемая мощность, кВт ………………………………….. 6,0
Масса, кг ……………………………………………………………………. 90
Габаритные размеры, мм………………………. 3000х1500х1300
Средняя производительность, м3/ч………………………………. 15
Максимальные размеры
разрезаемого блока, мм ………………………… 2000х1000х500
Плотность, кг/м3………………………………………………………………………………… 10-30
Точность резки, мм………………………………………………….. ±0,5
Минимальная толщина плит, мм ………………………………… 10
Станок для поперечной резки блока пенополистирола. Состав устройства: металлическая конструкция с рабочей поверхностью; подставка для изделия; подвижная каретка; резательное устройство. Для работы одного стола необходим трансформатор, который предназначен для нагрева режущий проволоки. Для одновременной работы двух и более столов требуется трансформатор соответствующей мощности.
Технические характеристики
Количество одновременных резов ……………………………… 1
Напряжение, В …………………………………………………. 220/380
Потребляемая мощность, кВт ………………………………….. 0,5
Масса, кг…………………………………………………………………… 65
Габаритные размеры, мм………………………… 1180х850х1850
Средняя производительность, м3/ч……………………………. 30
Максимальные размеры разрезаемого
блока, мм . …………………………………………….. 2000х1000х500
Плотность, кг/м3………………………………………………………………………………… 10-30
Точность резки, мм………………………………………………….. ±0,5
Оборудование для производства полистирольного пенопласта «ВЯТКА СтройДеталь»
Оборудование предназначено для получения пенопласта, теплоизоляционных плит с плотностью 15-50 кг/м3 по ГОСТ 1558 8 «Плиты пенополистирольные. Технические условия». Для изготовления пенополисти-рольных плит используется полистирол вспенивающийся марок ПСВ-С или ПСВ по ОСТ 301-05-202-92Е.
Комплект оборудования: предвспениватель; бункер выдержки гранул; блок-форма; компрессор блок-формы; установка вакуумирования; установка резки блоков на плиты; дробилка отходов; добавочный бункер для вторсырья.
Предприятие поставляет оборудование для производства теплоизоляционных плит из пенополистирола мощностью 9000 м3/год (при использовании одной блок-формы модели УНФБ-05 и односменной работе) и 18000 м3/год (при использовании двух блок-форм или при двухсменной работе) .
Вспениватель предварительный. Модель ПВ-1. Предвспениватель входит в комплект технологического оборудования для стендового производства плитного пенополистирола по ГОСТ 15588-86. Он предназначен для первичного вспенивания гранул полистирола вспенивающегося нерассеянного ПСВ-СВ-НМ, рассеянного ПСВ-СВ-Р марок 1, 2, 3, 6 и др. методом тепловой обработки. В качестве теплоносителя используется водяной пар.
Технические характеристики
Номинальная производительность за один цикл, м3 … 1,0
Производительность, м3/ч. ……………не менее 10
Полезный объем (вместимость) , м3. ……………………………………………. 1,2
Марки получаемого пенопласта
по плотности………………………………………………. 15, 25, 35, 50
Средняя плотность получаемой
вспененной крошки, кг/м3 ……………………………………. 11-40
Рабочее (избыточное)
давление пара, МПа………………………….. не более 0,01-0,03
Частота вращения активатора, об./мин………………………….. 90
Рабочая температура пара, °С …………………………. 100-108
Потребление пара для предвспенивания с учетом формования блока пенопласта блок-формой при максимальной производительности
блок-формы 4,5 м3/ч) , кг/ч………………………………. 160-200
Габаритные размеры, мм. ……………………… 1100x1050x2800
Масса, кг…………………………………………………………………… 530
Количество электродвигателей на установке, шт…………… 1
Номинальная мощность привода, кВт…………………………… 4
Модель и типоразмер мотор-редуктора (вертикальное исполнение) 4МЦ2С-100. Обслуживает установку один человек. Давление, обеспечиваемое парогенерирующим оборудованием, — 5-6 атм, паропроизводительность не менее 200 кг/ч (при max производительности блок-формы) . Ток переменный трехфазный; напряжение 380 В.
Установка непрерывного формования блоков. Модель УНФБ-05 (патент № 40019)
Технические характеристики
Размеры производимого блока
высота х толщина) , мм …………………… не менее 1000х504
Производительность за один цикл, м3. ………………………………………. 0,5
Длина блока, формируемая за один цикл, мм……………. 1000
Производительность установки, м3/ч. ………..до 4,5
Число циклов в 1 ч:
без вакуумирования………………………………………………… 3;
с вакуумированием ………………………………………………… 9
Рабочее (избыточное) давление пара в паровой рубашке
блок-формы, МПа…………………………………………………… 0,03
Температура пара в рабочей камере формы, °С . . . 104-108
Давление, обеспечиваемое парогенерирующим
оборудованием, атм…………………………………………………… 5-7
Паропроизводительность (при работе
с вакуумированием), кг/ч…………… ……………. не менее 200
Потребление пара для формования с учетом предвспенивания (при максимальной
производительности) , кг/ч…………………………………. 160-200
Расход сжатого воздуха пневмоцилиндрами, м3/ч. … 0,5
Номинальное рабочее давление
пневмоцилиндров, атм……………………………………………….. 10
Габаритные размеры, мм…………………………. 710х3780х2210
Марки получаемых блоков по ГОСТ 15588 — 15, 25, 35. Пневмоцилиндры итальянского производства «CAMOZZI». Для работы пневмосистемы блок-формы необходим компрессор 10 атм, производительностью не менее 0,16 м3/мин; объем ресивера 60 л. Исполнение загрузочного клапана и узла, выталкивающего блок, -пневматическое. Обслуживает установку один человек.
Установка непрерывного формования блоков. Модель УНФБ. Входит в комплект технологического оборудования для стендового производства плитного пенополистирола по ГО
Что такое пена высокой плотности? (с иллюстрациями)
Пена высокой плотности — это тип пенополиуретана, который состоит из большого количества открытых ячеек или пузырьков, которые плотно упакованы вместе. Результатом этой более высокой концентрации или плотности является то, что воздух может легче проходить через отверстия в ячейках, что значительно упрощает создание удобной набивки для подушек, матрасов и других подобных продуктов. Плотность пены этого типа также имеет тенденцию сохранять свою форму с большей эффективностью, что позволяет ей возвращаться к нормальным размерам, когда любой объект поднимается с поверхности пены.
Матрасы могут быть изготовлены из пеноматериала высокой плотности.
Один из лучших способов понять, как работает пена высокой плотности, — рассмотреть матрас, который изготовлен с использованием этого продукта. Структурная пена, используемая в матрасе, позволяет ему соответствовать контурам человека, спящего на матрасе.В то же время пена обеспечивает поддержку, которая позволяет позвоночнику оставаться в естественном положении, снимая нагрузку на спину и шею. В результате этого смягчающего эффекта человек может наслаждаться более глубоким и восстановительным сном и с большей вероятностью проснется, чувствуя себя отдохнувшим и отдохнувшим.
Подушки и подушки могут быть изготовлены из пеноматериала высокой плотности. В отличие от некоторых других продуктов, пена высокой плотности имеет способность восстанавливать первоначальную форму вскоре после того, как любой груз снимается с продукта. Например, матрас, сделанный из этой пены, обеспечивает идеальную поддержку спящего, но быстро возвращается к своему первоначальному виду после того, как человек встает. Такие матрасы будут сохранять форму долгие годы, обеспечивая более длительный период активного использования, чем матрасы из других материалов.
Есть несколько других распространенных применений пены высокой плотности.Подушки и подушки часто делают из этого продукта. Обивочная пена высокой плотности позволяет диванам и стульям обеспечивать комфортное сидение в течение многих лет, прежде чем под обивкой начнут появляться провисания или вмятины. Изделие также можно использовать для обивки стен в звукозаписывающих кабинах и в других помещениях, помогая с высокой эффективностью приглушать шумы.
С точки зрения стоимости изделия, изготовленные из пенопласта высокой плотности, как правило, конкурентоспособны по сравнению с изделиями, изготовленными из других материалов. Часто срок службы изделий из пены может быть равен сроку службы изделий, изготовленных из других материалов, или даже превышать его. По этой причине использование этого продукта для набивки или в качестве основного материала в ряде продуктов является практичным и экономичным для производителей, а также доступным по цене и предлагает долгосрочное обслуживание потребителей.
FOAM-iT! ™ 10 Информация о продукте | Smooth-On, Inc.
Smooth-On’s FOAM-iT! ™ серии — это двухкомпонентные жесткие вспененные материалы, получаемые из вспененных материалов, которые универсальны и просты в использовании. Части A и B измеряются и смешиваются в равных количествах по объему. Затем смесь выливают в форму или другую форму (при необходимости наносят разделительный состав). Смесь во много раз увеличится в исходном объеме (в зависимости от того, какой продукт FOAM-iT! ™ вы используете) и разовьет однородную структуру ячеек.FOAM-IT! ™ 10 теряет липкость примерно за 4–6,5 минут, развивает прочность при обработке за 20 минут и полное отверждение за 2 часа.
FOAM-iT! ™ можно использовать в качестве материала для прямой отливки, материала для засыпки полых отливок (повышает конструкционную прочность) или в качестве герметизирующего материала и т. Д. Они могут быть окрашены в цвет с помощью SO-Strong ™, UVO ™ или Красители IGNITE ™ используются в различных областях искусства / ремесел, промышленного дизайна и создания специальных эффектов.
› Нажмите здесь, чтобы увидеть другие продукты из жесткого пенопласта FOAM-iT! ™.
Инструкции
ПОДГОТОВКА — Хранить и использовать при комнатной температуре (73 ° F / 23 ° C). Используйте в помещении с низкой влажностью (ниже 50% относительной влажности). Емкости для смешивания должны иметь прямые стенки и плоское дно. Палочки для смешивания должны быть плоскими и жесткими с определенными краями, чтобы можно было соскребать стенки и дно емкости для смешивания. Необходима хорошая вентиляция (размер комнаты). Срок годности этого продукта ограничен, и его следует использовать как можно скорее. Надевайте защитные очки, длинные рукава и резиновые перчатки, чтобы свести к минимуму риск загрязнения.
Поскольку нет двух совершенно одинаковых приложений, рекомендуется небольшое тестовое приложение для определения пригодности для вашего проекта, если производительность этого материала находится под вопросом.
ВАЖНО: Срок хранения продукта сокращается после открытия. Оставшийся продукт следует использовать как можно скорее. Немедленное закрытие крышек на обеих емкостях после выдачи продукта поможет продлить срок хранения неиспользованного продукта. XTEND-IT ™ Dry Gas Blanket (можно приобрести у Smooth-On) значительно продлит срок хранения неиспользованных жидких уретановых продуктов.
НАНЕСЕНИЕ ВЫПУСКАЮЩЕГО СРЕДСТВА — Пенополиуретан является адгезивным и может прилипать / связываться со многими поверхностями. Мы рекомендуем Ease Release 2831 для удаления уретановой пены с большинства поверхностей. Если нанесение смазки особенно сложно (например, отделение уретановой пены из уретанового каучука), мы рекомендуем нанесение Universal Mold Release с последующим нанесением Ease Release 2831.
ПРЕДУПРЕЖДЕНИЕ: Не используйте сам по себе Universal Mold Release или любые другие смазки на основе силикона.Это разрушит пену.
ИЗМЕРЕНИЕ И СМЕШИВАНИЕ — Жидкие уретаны чувствительны к влаге и впитывают атмосферную влагу. Инструменты и емкости для смешивания должны быть чистыми, из металла, стекла или пластика. Материалы следует хранить и использовать в теплой среде (73 ° F / 23 ° C). Знайте соотношение компонентов продукта FOAM-iT! ™, который вы используете. После внесения нужного количества частей A и B в емкость для смешивания, тщательно перемешайте в течение 45 секунд. Перемешайте быстро, убедившись, что вы несколько раз поскребли стенки и дно емкости для смешивания. Будьте осторожны, чтобы не выплеснуть материал с низкой вязкостью из контейнера. Помните, пена схватывается быстро. Не допускайте задержек между смешиванием и заливкой.
Заливка и отверждение — Для достижения наилучших результатов вылейте смесь в одну точку в самой нижней точке защитного поля и дайте смеси достичь своего уровня. Оставьте место в защитном поле, чтобы пена увеличивалась до своего предельного объема.Перед работой дайте пене застыть не менее 20 минут (FOAM-iT! ™ 10 SLOW — 1 час). Время отверждения будет зависеть от массы и конфигурации формы.
Массовая концентрация / конфигурация пресс-формы — Одновременная заливка больших количеств в определенные конфигурации пресс-формы (например, цилиндр) может вызвать избыточное тепло и привести к расколу (трещинам). Постепенная заливка слоями может решить эту проблему.
Улучшение качества поверхности и минимизация пустот с помощью противодавления — Закрывание полости формы доской с предварительно просверленными отверстиями улучшит чистоту поверхности некоторых пен. Для получения дополнительной информации посмотрите видео на smooth-on.com/backpressure
Полностью отвержденная пена FOAM-iT! ™ Пену можно шлифовать, обрабатывать, сверлить и т. Д. (Используйте респиратор, одобренный NIOSH). Пену также можно загрунтовать и / или покрасить.
Пенополиэтилен
| ТАРТ, s.r.o.
Вспененный полиэтилен (EPE) является водонепроницаемым, механически устойчивым, защищает от повторяющихся ударов, чрезвычайно химически стойким и полностью пригоден для вторичной переработки. Он используется в основном для защитной упаковки мебели, электроники, автомобильных запчастей и других товаров.
Преимущества вспененного полиэтилена
- выглядит эффектно,
- отличная гибкость, низкая теплопроводность
- химическая стойкость,
- сопротивление механическому удару,
- охрана труда и окружающей среды,
- простота обработки и долговечность,
- полностью перерабатывается (не содержит галогенов, сульфатов, силиконов, кадмия, свинца .
..)
Типичные области применения пенополиэтилена
- защита изделия от истирания,
- защита краев и углов продукта,
- шаг продукта,
- теплоизоляция, подкладка для напольного покрытия,
- тепло- и звукоизоляция крыш и стен зданий,
- защитная теплоизоляция для теплиц, парников и конюшен,
- теплоизоляция трубопроводных систем,
- производство матов.
Технические характеристики пенополиэтилена
Пенополиэтилен- может поставляться шириной и длиной по желанию заказчика
- пенополиэтилен толщиной до 100 мм,
- по запросу возможно изготовление листов, пакетов и кромок из этого материала.
Пенополиэтилен в рулонах | Пенополиэтилен — листы |
— Толщина: 0,8 — 10 мм — Ширина: 1000 и 1500 мм — Длина: 50-700 м — Плотность: 18-21 кг / м 3 | Толщина: 0,8 — 100 мм Ширина: 120–1000 мм Длина: 150–2000 мм |
Пенополиэтилен — мешки | |
— Толщина: 0,8 — 2 мм |
Кромки из вспененного полиэтилена (ЭПЭ)
- защита углов и краев чувствительных к повреждениям изделий (листовое стекло, мебель, острые края.
….)
- легкий, гибкий, устойчивый к повреждениям, литой,
- подходит для многоразового использования,
- выпускается стандартной плотностью от 30 до 45 кг / м3 3 ,
- возможность изготовления угловой фурнитуры по индивидуальному заказу,
- можно использовать несколько раз подряд,
Виды пенополиэтилена:
PLASTOCELL — вспененный полиэтилен (EPE)
— это вспененный полиэтилен, ламинированный полиэтиленом высокой плотности толщиной 10 мкм,
- толщина: от 1 мм до 5 мм,
- ширина рулона 1000 мм, 1200 мм, 1500 мм,
- длина рулона 500 м,
- другие возможные варианты: мешки.
STRATOCELL ® — вспененный полиэтилен (EPE)
— пенополиэтилен низкой плотности без сетки, идеален для множественной защиты продукта
— поглощает повторяющиеся удары по изделию и при этом существенно не теряет своих защитных свойств.
- слоистая ламинация — нанесение тепла Стандартная серия
- : Stratocell® E и Stratocell® S Специальная серия
- : Stratocell® FC, Stratocell® 35, Stratocell® 65 и Stratocell® 100.
- стандартные размеры листа: 1200 мм x 2000 мм
- дополнительные листы могут поставляться длиной от 1500 до 3000 мм
- толщина: 25-50 мм.
CELL-AIRE — Вспененный полиэтилен (EPE)
- производство полиэтилена низкой плотности (LDPE) без примеси веществ на основе CFCs;
- многоразового использования и вторичной переработки,
- с закрытыми ячейками без сетчатой структуры,
- поставляемая толщина: 0,7 мм, 1.0 мм, 1,5 мм, 2,5 мм и 4,0 мм
CUSHION-PLY — вспененный полиэтилен (EPE)
- высокоэффективный вспененный полиэтилен низкой плотности
- может заменить полиуретановые листы, пенополистирол и картонные складные коробки
- поставляется толщиной 40 мм, плотностью 16 кг / м3
- можно прессовать и сваривать горячим воздухом.