Что такое газобетон и как его делают
Газобетон — современный энергоэффективный материал для индивидуального строительства. Он относится к ячеистым бетонам т.к. до 85% объема материала занимают пузырьки газа. Газобетон обладает превосходными теплоизоляционными характеристиками, имеет небольшую массу и легко поддается обработке. И самое главное — дом из газобетона можно построить самостоятельно, без посторонней помощи (один человек в день может выложить до 3 кубических метров газобетона). Главное не путать газобетон и пенобетон, это совершенно разные материалы, об этом поговорим в конце репортажа.
Чтобы более подробно увидеть процесс производства газобетона я отправился на завод Ytong в Можайске, начавший свою работу в 2008 году. По объемам произодства газобетона, это самый крупный завод в России. Смотрим!
2. Для производства газобетона используется безопасное сырье: цемент (~20%), известь (~20%), кварцевый песок (~60%), алюминиевая паста (~1%) и вода. Все компоненты смешиваются в определённых пропорциях, которая определяется требуемой прочностью готовой продукции.
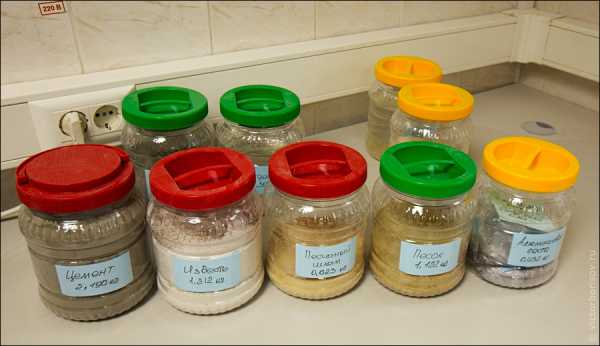
3. Основу газобетона составляет песок, который нужно предварительно обработать.
4. Для этого используются шаровые мельницы.
5. Внутри барабана находятся вот такие шары, которые измельчают песок до превращения в пыль. Это нужно для того, чтобы после формовки блоки было легче обрабатывать.
6. После этого исходное сырье поступает в накопительные бункера на хранение. Затем в газобетоносмесителе происходит смешивание песка, цемента и извести.
7. А непосредственно перед заливкой к уже смешанным компонентам добавляется вода и суспензия алюминиевой пасты. Готовая смесь заливается в специальную прямоугольную форму (стенки формы не имеют жесткого соединения с дном) примерно на 2/3.
8. Именно на этом этапе происходит самое интересное. Алюминиевая паста вступает в реакцию с известью, в результате получается водород. Он образует в сырьевой массе огромное количество пор размером от 0,5 до 2 мм, разномерно распределённых внутри. Поддоны со смесью медленно продвигаются в герметичном помещении с запредельной влажностью (это единственный кадр, который я успел сделать до того, как запотел объектив) до тех пор, пока смесь не увеличится в объеме до верхней кромки поддона.
9. Через некоторое время (2-3 часа) транспортёр переносит форму с застывшей смесью на следующий этап. Показательно, что подъемник только за счёт ваккуума удерживает поддон без дна.
10. Теперь застывшую форму разрезают на блоки равного размера. Сначала в поперечном, а затем продольном направлениях. На заводе одна линия, которая единовременно может производить блоки только одного размера. Для производства блоков другого типоразмера просто заменяют ножи. Большая площадь для складирования готовой продукции позволяет всегда иметь в наличии полный ассортимент продукции.
11. После этого внешняя проверхность блоков шлифуется и затем они прижимаются друг к другу.
12. Кран захватывает поддон с блоками и переносит их на следующий этап производства.
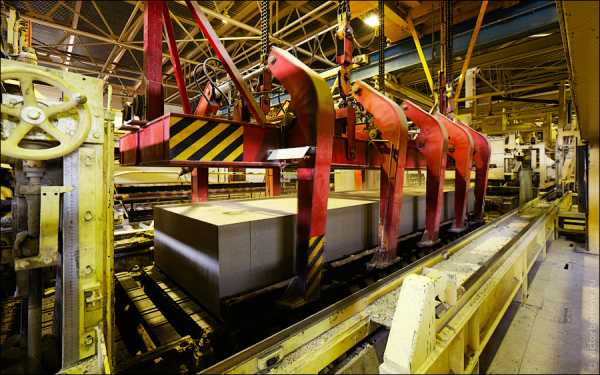
13. И сразу же укладывается новый поддон в основание для следующей партии блоков. Да, очень важный факт — производство на заводе полностью автоматизировано и практически не требует участия человека. Люди работают только на линии упаковки (она пока еще не настолько автоматизирована), складе и в испытательной лаборатории. Всего на заводе работает менее 80 человек (завод работает круглосуточно).
14. Теперь блоки нужно поместить в автоклав. Слева «сырые» блоки, справа уже «готовые». Здесь хочу упомянуть следующий момент, после автоклавирования блоки имеют влажность порядка 30%, которая постепенно (в течение года) упадёт до 5-10%.
15. Автоклавирование очень важный этап, улучшающий свойства газобетонных блоков.
16. Разрезанные блоки помещают в специальные автоклавные камеры, где они в течение 12 часов при повышенном давлении в 12 кг/кв. см. обрабатываются насыщенным паром при температуре 190°C. При этом температура в начале и конце цикла плавно поднимается и опускается в течение определённого времени.
17. Каждый автоклав имеет длину более 30 метров. Использование автоклавирования позволяет повысить прочность газобетонных блоков и уменьшить его последующую усадку (менее 1 мм/м).
18. Каждая партия блоков после автоклавирования отправляется в лабораторию для проверки на соответствие заданным характеристикам. На этом станке нарезаются кубики правильной формы, которые затем отправятся на испытания.
19. А готовые блоки отправляются на линию упаковки. Здесь их складывают в 2 ряда. Позиционирование рядов блоков производят вручную.
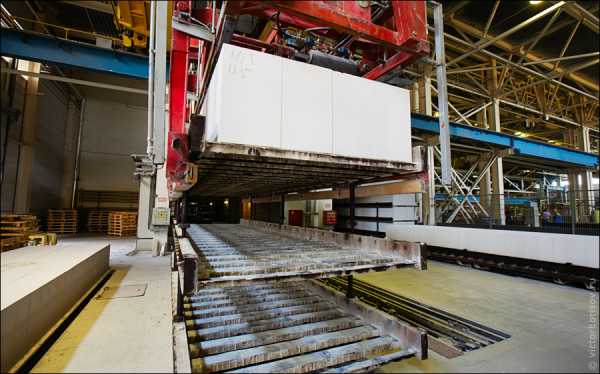
20. Затем их переворачивают на бок под уже установленные деревянные паллеты. После чего блоки запечатываются в плёнку (чтобы защитить их от повреждений) и отправляются на склад.
21. Склад расположен под открытым небом, здесь всегда есть запас всей выпускаемой продукции. Ежедневно с завода отгружается покупателям более 2000 кубометров блоков.
22. Основная продукция завода это блоки толщиной от 50 до 500 мм с плотностью от 400 до 500 кг/куб.м.
И ещё несколько слов про различия газобетона и пенобетона. Понятно, что газобетон материал новый, но очень многие неосознанно их путают даже не понимая, что их характеристики существенно отличаются.
Во-первых, их различие кроется в названии. Для производства пенобетона используется пена, состоящая их вредных химических веществ (канифоль, клей, едкий натр и т.д.). А в производстве газобетона используется газ, образующийся в результате химической реакции извести и алюминиевой пасты, в результате получается просто водород. То есть газобетон является экологически чистым строительным материалом.
Во-вторых, пенобетон имеет очень низкие прочностные характеристики. А здесь, как известно, имеет место быть обратная зависимость. То есть, чем ниже плотность (и соответственно прочность), тем «теплее» материал. Но если газобетон плотностью D400 (400 кг/кв.м) можно использовать для несущих стен в домах до 3 этажей включительно и он будет обладать классом прочности В2,5 и морозстойкостью F100, то из пенобетона плотностью ниже D600 вообще нельзя делать несущие стены. Следовательно и теплопроводность пенобетона D600 будет значительно выше (то есть «холоднее»), чем газобетона D400.
В-третьих, технология производства пенобетона обычно не подразумевает использования автоклавов и нарезки блоков после застывания. Обычно его заливают сразу в готовые формы, а в результате блоки дают большую усадку (3-5 мм/м) после строительства. Не говоря уже о том, что сам процесс автоклавирования повышает прочность блоков в 3-4 раза.
Немного видео с производства:
Источник
kak-eto-sdelano.ru
Газобетонные блоки — практически идеальный строительный материал
Газобетонные стеновые блоки представляют собой изделия, сделанные из ячеистого бетона. Из чего же состоит газобетонный блок? Для его изготовления берется кварцевый песок, вода и цемент, присутствуют дополнительные компоненты. Блоки делаются в специальных печах, где обеспечено высокое давление и температура.
Что такое газобетон
Этот материал легкий и прочный, но обладает отличными свойствами, в том числе, плотностью и прочностью, теплопроводностью. Многие строители считаются газобетонные блоки идеальными, когда речь идет о строительстве до четырех этажей. Они отлично подходят при возведении стен и перегородок, в монолитном строительстве блоками этой категории можно заполнять проемы.
Газобетон был изобретен давно, но с разработкой новых современных производственных технологий, стали выпускаться усовершенствованные газобетонные блоки различных конструкций и видов.
Состав газобетонных блоков
Производятся современные газобетонные блоки из песка и извести, цемента, алюминиевой пудры. Токсичных веществ готовый материал не выделяет, поэтому по характеристикам его часто сравнивают с деревом.
При том, что блоки имеют дополнительные плюсы – не гниют и не подвержены естественному процессу старения. Материалы, которые входят в состав блоков, экологически чистые. Радиационный фон готового изделия не превышает 11 мкр/ч.
Благодаря простому составу блоки получаются пористыми, поэтому строение будет постоянно дышать пропускать воздух в помещение, от чего находиться в нем будет приятно и комфортно.
Из чего делают газобетонные блоки:
- Смеси цемента и извести;
- Кварцевого песка;
- Алюминиевой пудры;
- Воды;
- В зависимости от особенностей производства могут добавлять смеси, улучшающие свойства газобетона.
Газобетон представляет собой пористый строительный материал, который, чаще всего, прессуется в виде блоков. Главным компонентом для производства является цемент в сочетание с известью, также песок.
Пенобетон и газобетон: существенные отличия
Часто газобетон сравнивают с пенобетоном, более того, эти материалы могу путать. На самом деле они сильно отличаются друг от друга по компонентам, способу производства и основным характеристикам.
Пенобетон — это более дешевый материал, при производстве которого вместо кварцевого песка используются производственные отходы. Пенобетон дозревает на воздухе, а это значит, у него более низкие эксплуатационные качества.
Блоки газобетона будут иметь коэффициент теплопередачи гораздо выше. Поэтому уровень теплоизоляции в готовом строение также будет выше. В среднем при толщине стен от 400 мм от уже будет равен принятым средним показателям.
Газобетон не дает усадку в процессе эксплуатации, а вот от пенобетона усадки надо ожидать. Из всего сказанного становится понятным, почему пенобетон дешевле описываемого материала на 20-25%. Но при покупке более дешевого материала также возрастает риск купить некачественный пенобетон, который в итоге придется заменять более надежными материалами.
В пенобетоне поры распределены не равномерно, они также отличаются по размеру. Также более углубленное внешнее изучение материалов показывает, что первый практически не имеет отклонений в геометрии, а во втором случае такие отклонения могут достигать 10 мм.
Отличать также можно по внешнему виду. Газобетонные блоки по цвету всегда белые, а вот пенобетон более темный и серый. Если разрезать первый вид блока, то будет видна упорядоченная пористая структура и каждая ячейка в точности повторяет другую.
На основании этого можно сделать вывод, что газоблоки все же лучше, чем пеноблоки, хотя и существенно дороже, но за качество всегда приходится платить больше.
На фото идеальная кладка из газобетонных блоков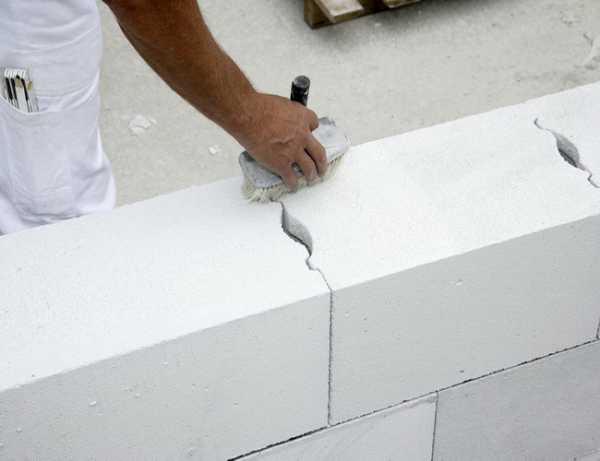
Плюсы газобетонных блоков и их минусы
Основные свойства описываемого материала настолько хороши, что являются важными его плюсами:
- Прочностью и долговечность. Чтобы эти характеристики проявились в полной мере, важно использовать материал правильно: для возведений зданий без каркаса и высотой не более четырнадцати метров. Также его можно смело применять для устройства внутренних стен и перегородок. По сроку службы блоки этого вида можно приравнивать к сроку службы кирпичей. Производитель дает гарантию в 80 лет.
- Качественная теплоизоляция. В многочисленных порах материала заключен воздух, что обеспечивает отличные свойства по сбережению тепла. Всем строительным нормам дом из газобетонных блоков полностью соответствует. Чем ниже объемный вес газобетона, тем выше будут теплоизоляционные характеристики. Прогреваются дома из описанного вида блоков всего за несколько часов.
- За счет общей легкости блоков нагрузка на фундамент сводиться к минимуму. Один блок заменяет при кладке двадцать кирпичей, это значит, что общее время работ и расход материала сокращается в несколько раз.
- Экологичность. Материалы основные только натуральные и чистые, сам по себе блок также показывает высокие экологические свойства. Вредных веществ он не выделяет. По способности пропускать воздух газобетон сравнивается с деревом. Стены из описываемого материала на ощупь всегда теплые за счет низкой теплопроводности.
- Устойчивость к огню. Проведенные исследования показали, что материал горение не поддерживается, так же, как и сам не горит. На газобетонную стену прямой огонь может воздействовать 3-7 часов и она устоит. Часто блоки этой категории используют, чтобы защищать от огня металлические конструкции.
- Морозостойкость, то есть, способность выдерживать полное замораживание и оттаивания. Мелкие поры материала вытесняют лед и воду. Поэтому около ста циклов сохранность газобетонного блока обеспечена. Если сравнить с кирпичом, он выдерживает только 25 циклов, а пенобетон – всего 35 циклов).
- Удобство обработки. Блоки из описываемого материала можно смело сверлить, колоть и резать. Причем, разрезаются блоки с помощью обычной ручной пилы.
Но любой строительный материал наравне с преимуществами имеет и свои недостатки. Его говорить про газобетон, то тут есть такие свои нюансы. Во-первых, не рекомендуется стоить здание выше трех этажей, потому что материал имеет ограниченную способность к сжатию. Во-вторых, требуется дополнительная внешняя облицовка стен, потому что материал активно впитывает влагу. К третьему минусу относится высокий коэффициент усадки (особенно, у неавтоклавного варианта).
Практически все характеристики описываемого материала являются отличными для строительства. Особенно надо обращать внимание на прочность, из-за которой газобетонные блоки лучше всего использовать для возведения построение не более четырех этаже в высоту.
Как выбрать качественные газобетонные блоки
При подборе стройматериалов важно знать и учитывать такие параметры как теплопроводность, плотность, прочность, звукоизоляция, огнестойкость.
При покупке важно сравнивать эти характеристики, потому что у разных производителей они могут отличаться:
- Коэффициент теплопроводности должен начинаться от 0,075 Вт/(м•К) для блоков плотностью D350 и от 0,25 Вт/(м•К) для блоков марки D700. В доме будет теплее, когда у используемого материала показатель этого коэффициента будет низким.
- Плотность в отношении массы к объему определяется марками от D300-350 до D1200 кг/м?. Чем выше показатель, тем более прочной будет конструкция, более хорошей будет звукоизоляция.
- Любые блоки этой категории должны обладают огнестойкостью, потому что они относятся к материалам негорючим. Перегородка из ячеистого бетона, уже отштукатуренная, в течение нескольких часов может выдерживать огонь не изменяя свой изначальный вид, не утрачивая характеристики.
- Газобетон должен быстро выветривать влагу и выводить водяной пар из помещения, которое отапливается.
Чем выше индекс воздушного шума (определяется в дБ), тем лучшими звукоизоляционными свойствами обладает материал.
С появлением на рынке стройматериалов ячеистых бетонов расширились возможности застройщиков. Те уникальные свойства, которые присущи газобетону, грех не использовать при строительстве жилых и специальных объектов.
Есть ли вред для здоровья
Газобетонные блоки – это совершенно безвредный для здоровья человека материал. Несмотря на то, что материал этот искусственный, он производится из природных компонентов, которые являются совершенно безопасными. Экологичность придают те природные компоненты, из которых блоки состоят.
Этот материал активно используется в современном строительстве, он имеет несущественные минусы. Его можно смело использовать для зданий до четырех этажей высотой. Высота здания не имеет значения, если делать перегородки и несущие стены внутри помещения.
Возведение построек из газобетона сопряжено с некоторыми особенностями. Перед началом работ следует внимательно изучить не только свойства газобетона, но и технологию его укладки. Газоблоки укладываются намного проще, чем кирпичи или шлакоблок.
stroyres.net
что это такое и где применяется
Для строительства зданий применяются различные виды пористых бетонов, отличающихся ячеистой структурой бетонного массива. Многие застройщики и профессиональные строители используют для постройки домов газобетон. Использование композита для изготовления газобетонных блоков снижает сметную стоимость работ, уменьшает нагрузку на фундамент строения, а также позволяет обеспечить комфортный микроклимат в помещении. Рассмотрим свойства и характеристики газобетонных блоков (газоблоков), а также разберемся с технологией их изготовления.
Что такое газобетон и изделия из него
Большинство застройщиков имеет представление, что такое газоблок. Это изделие в виде прямоугольного параллелепипеда, изготовленное из газонаполненного бетона. Газоблок производится по автоклавной технологии с использованием алюминиевого порообразователя.
Газобетон как строительный материал приобрел в последнее десятилетие широкую популярностьОтличительные особенности газобетона:
- равномерное распределение в газобетонном массиве воздушных полостей;
- стабильный диаметр внутренних ячеек;
- концентрация ячеек в газобетонном массиве – до 70%;
- открытая форма воздушных полостей.
Ячеистая структура газобетонного массива повышает способность материала пропускать пар и положительно влияет на его теплоизоляционные свойства. Газобетон легко определить по белому цвету и шероховатой поверхности.
Газобетон отличается:
- плотностью материала;
- областью использования;
- размером воспринимаемых усилий.
В зависимости от указанных особенностей газонаполненный композит (газобетон) делится на следующие разновидности:
- теплоизоляционный;
- конструкционно-теплоизоляционный;
- конструкционный.
Блочная продукция из газобетона имеет различный размер, вес, объем. Количество газобетонных блоков для выполнения кладки несложно определить с помощью онлайн-калькулятора.
Газобетон не слишком сложен в производстве, однако для достижения высокого качества требует высокотехнологичного оборудованияИз чего изготовлен газоблок
Производство газобетона осуществляется по автоклавной технологии с использованием следующих компонентов:
- цемента с маркировкой М400 или М500, применяемого в качестве вяжущего ингредиента. Концентрация не превышает 35–45%;
- просеянного кварцевого песка, используемого как заполнитель. Содержание заполнителя в газобетонной смеси достигает 40–45%;
- гашеной извести, участвующей в реакции порообразования. При концентрации от 12 до 18% достигается требуемый размер воздушных ячеек;
- порошка алюминия, выполняющего функцию порообразующего вещества. Порообразователь добавляется в количестве до 1%;
- кальциевого хлорида в объеме 0,2% и силиката кальция в количестве 2,5%, вводимых для обеспечения требуемой структуры газобетонного массива;
- воды, подогретой до 55–60 градусов Цельсия. Вода добавляется согласно рецептуре до достижения требуемой кондиции газобетонного состава.
Основными компонентами, входящими в его состав, являютсяПроцентное соотношение вводимых ингредиентов уточняется экспериментальным путем. Количество добавляемых компонентов влияет на прочностные свойства и структуру газобетона.
Технология производства газобетона
Для производства газонаполненных композитов применяются специальные емкости – автоклавы. Они представляют собой резервуары с внутренним давлением свыше 8 атм и температурой насыщающего газобетон пара, достигающей 160 градусов Цельсия.
Технология изготовления газобетонных блоков предусматривает следующие этапы:
- Дробление кварцевого песка в измельчителях с помощью металлических шаров.
- Взвешивание и дозирование компонентов согласно используемой рецептуре.
- Засыпку цемента, кварцевого песка и извести в емкость и последующее их смешивание.
- Добавление в газобетонную смесь алюминиевой суспензии вместе с нагретой водой.
- Заливку газобетонного состава в формовочные емкости (литформы).
Форма заполняется композитом на 60–70% от общего объема, так как состав в результате химической реакции увеличивается в объеме и достигает ее верхнего уровня. В формах алюминиевый наполнитель реагирует с известью. При этом выделяется газ, способствующий формированию пористой структуры. В результате образуются воздушные ячейки размером от 0,5 до 3 мм, равномерно распределенные по объему газобетонного массива.
Дальнейшая последовательность действий предусматривает:
- Разрезание затвердевшего массива на блоки требуемых размеров.
- Сбор излишков состава для повторного применения.
- Укладку разрезанных блоков на поддоны и загрузку в автоклавную емкость.
После газообразования и приобретения изначальной прочности газобетонная масса режется на отдельные блоки
- Извлечение газобетонных изделий из автоклавного резервуара.
- Укладку на готовую продукцию полиэтиленовой пленки.
- Транспортировку блоков на склад готовой продукции.
Проверка характеристик газобетона проводится на лабораторных образцах. Автоматизированный контроль процесса пропарки обеспечивает требуемую технологией температуру и влажность, гарантирующие необходимые характеристики газоблоков.
Возможно, также, производство газоблоков по неавтоклавной технологии. Однако изготовленные таким образом газобетонные блоки обладают уменьшенной прочностью. Они также характеризуются увеличенной усадкой, что сказывается на качестве кладки газобетонных блоков. Обеспечить однородную структуру воздушных полостей и требуемые эксплуатационные свойства позволяет исключительно автоклавный способ изготовления.
Где применяются газоблоки
Изделия стеновые неармированные, изготовленные из газобетона, а также перегородочные элементы и теплоизоляционные панели применяются в области частного и промышленного строительства.
Свойства газобетона и технология строительства предусматривают возможность применения пористого стройматериала для следующих целей:
При строительстве частного дома можно обойтись без подъемных механизмов, а темп строительства увеличивается- постройки несущих стен и межкомнатных перегородок. Применяются газобетонные изделия марки D 500, способные воспринимать значительные усилия;
- теплоизоляции кирпичных и железобетонных стен с фасадной стороны здания. Используется материал с маркировкой D300, D400 или D500;
- строительства заборных ограждений. Такие конструкции оперативно возводятся и не требуют больших расходов;
- сооружения армированного пояса по периметру стен. Применяются газобетонные изделия u-образной формы, усиленные арматурой;
- изготовления монолитных перемычек для различных проемов. Используются профильные изделия из газобетона.
Повышенные показатели теплоизоляции, габаритные размеры и высокая морозостойкость позволяют применять газоблок для возведения жилых строений, постройки гаражных помещений и строительства бань. Материал популярен благодаря надежности и долговечности. Однако стены из блоков нуждаются в гидроизоляционной защите. Запас прочности обеспечивает возможность строить дома из газоблоков высотой в три этажа.
Недостатки и достоинства газоблоков
Начнем с преимуществ газобетона. Главные плюсы:
- увеличенные габариты при небольшом весе;
- отсутствие необходимости применения грузоподъемной техники;
- простота кладки блоков на клеевой состав;
- ускоренные темпы возведения стен и перегородок;
- высокие теплоизоляционные характеристики;
- минимальные допуски размеров, правильная форма изделий;
- повышенные звукоизоляционные характеристики;
- стойкость к открытому огню и повышенной температуре;
- экологическая чистота газобетонного материала;
- легкость механической обработки газобетона;
- стойкость к холоду и температурным колебаниям;
- способность пропускать пар из помещения;
- продолжительный срок использования.
Слабые стороны газобетона:
- хрупкость;
- гигроскопичность;
- необходимость использования для кладки специального клея;
- сложность фиксации в пористом материале крепежных метизов.
Благодаря комплексу достоинств газобетон широко применяют в индивидуальном и производственном строительстве для решения различных задач.
Рекомендации по выбору газоблоков
Приобретая блоки, обратите внимание на следующие моменты:
- наличие сертификата соответствия;
- отсутствие сколов и трещин на блоке;
- условия хранения.
Стоит посмотреть видео, как выбрать газосиликатные изделия. Консультация профессионалов поможет в принятии решения.
Влияет ли газобетон на здоровье
Отвечая на вопрос об экологичности газобетона, отметим:
- материал изготавливается из экологически чистого сырья;
- в процессе эксплуатации не происходит выделение токсичных веществ;
- входящая в состав газоблока известь превращается в ходе реакции в кальциевый силикат, безвредный для окружающих.
Вывод – газобетон безвреден для здоровья людей.
Рекомендации
Газобетонные блоки автоклавного твердения целесообразно использовать для строительства. Принимая решение о применении материала, следует изучить его свойства и разобраться, чем отличаются газосиликатные блоки от газобетонных. Решая строить из пеноблоков, учтите, что главное отличие газобетона и пенобетона в технологии производства, влияющей на структуру массива и качество стройматериала. Определяясь с выбором материала для постройки дома, изучите также производство фибробетона. Желая использовать пескобетон, что это такое разберитесь досконально.
Решая, из какого материала лучше строить дом, выбирайте материал, обладающий повышенной прочностью, теплоизоляционными свойствами и морозостойкостью. Указанным критериям в полном объеме соответствует газобетон.
Подводим итоги
Газоблоки – современный стройматериал, обладающий комплексом достоинств и повышенными эксплуатационными характеристиками. Его используют для возведения частных домов и объектов промышленного назначения благодаря рабочим характеристикам, приемлемой цене и ускоренным темпам строительных мероприятий.
pobetony.expert
Из чего делают газоблоки?
Газоблоки – это современный строительный материал, отличающийся высоким качеством и надежностью. Но при этом такие изделия отличаются рядом отличительных особенностей.
Особенности газоблоков
Такой строительный материал отличается:
- отличной теплоизоляцией – он не пропускает холод в помещение и не выпускает тепло;
- пожаробезопасностью – такие изделия выдерживают воздействия высоких температур без повреждений;
- долговечностью – они не разрушаются с течением времени.
При всех своих преимуществах он еще и достаточно дешев в производстве, что делает его приоритетным выбором в большинстве случаев.
Как и из чего производятся газоблоки?
Технология создания газоблоков достаточно проста и включает в себя:
- воду;
- цемент;
- мелкий наполнитель;
- порообразователь.
Вода может использоваться самая обычная водопроводная или питьевая, но при этом в некоторых случаях предпочитают техническую воду. При этом она должна забираться из поверхностных источников, быть несоленой и иметь жесткость не выше средней, не содержать в своем составе различных примесей, в частности нефти, масел, жиров. Жидкость нагревается до 40-60 градусов, и эта температура поддерживается во время производства.
Также используется портландцемент марок М500Д0 и М400Д20. При этом нежелательно использовать продукцию, в которой содержатся минеральные добавки и вкрапления, отличающиеся гидрофобными характеристиками.
В смесь также добавляется песок, в качестве основного заполнителя. В роли наполнителей могут выступать различные минеральные добавки, в частности известняковая или доломитовая мука, получаемая с тепловых станций зола-унос, доменные шлаки или золошлаковые смеси.
Затем добавляется алюминиевый порошок, обеспечивающий образование пор. Дополнительно добавляется специальный порошок, который помогает частицам пудры распределиться по смеси.
В зависимости от требуемых характеристик могут быть дополнительные химические добавки. Они определяют скорость набора прочности, процесс газообразования или иначе изменяют готовое изделие.
Готовый и застывший массив газобетона отличается первое время достаточно пластичностью, чтоб провести его нарезку и придать необходимую форму. После этого в течение восьми часов он набирает прочность под специальным колпаком. Затем его можно использовать в строительстве, так как он отличается всеми необходимыми характеристиками.
www.hugebuilding.ru
виды, изготовление в домашних условиях, видео
Газобетон – это искусственный камень, который используют для возведения стен в индивидуальном строительстве. Он подходит для сооружения несущих конструкций, внутренних перегородок и заполнения межкаркасных пространств. Газоблоки не дают большой нагрузки на фундамент, поскольку имеют ячеистую структуру и малый вес. Это экономичный стройматериал, обладающий высокими теплоизоляционными свойствами.
Оглавление:
- Особенности и виды стройматериала
- Пропорции компонентов
- Методика производства своими руками
Состав и способ получения газобетона
Существует несколько типов классификации ячеистого бетона: в зависимости от назначения, формы, технологии производства и состава.
1. По способу обработки различают автоклавный и неавтоклавный газобетон.
2. По назначению газоблоки могут быть теплоизоляционным, конструкционным или конструкционно-теплоизоляционным. Они имеют определенную маркировку, например, газобетон d500 относится к классу конструкционно-теплоизоляционных блоков.
3. По форм-фактору делятся на U-образные, прямые и паз-гребневые.
Газоблоки изготавливают из песка, цемента, извести, воды, гипса и алюминиевой пудры. Также в производстве могут использоваться вторичные и побочные промышленные материалы, такие как шлак и зола. В зависимости от состава газобетона, его классифицируют на:
- цементный;
- шлаковый;
- известковый;
- зольный;
- смешанный.
В искусственно синтезированный камень строительная смесь преобразуется лишь при определенных условиях. Для его получения используют технологию автоклавного затвердения. В этом случае состав застывает под влиянием насыщенного пара и высокого давления, меняя свою структуру. В смеси образуется минерал тоберморит, который придает материалу прочность. Таким образом получают автоклавный газобетон.
Бетон, затвердевающий в естественных условиях, называют неавтоклавным. Он имеет ячеистую структуру, но отличается по своим свойствам от газоблоков, изготовленных по специальной технологии. Этот стройматериал больше подвержен усадке при эксплуатации, поэтому его целесообразно применять в случае небольших нагрузок. Чтобы увеличить прочностные характеристики неавтоклавных блоков, в исходный состав добавляют различные армирующие вещества и наполнители. Снизить усадочную деформацию позволяет применение полиамидных пластмасс при армировании.
Производство неавтоклавных блоков не требует дорогостоящего оборудования, поэтому их можно сделать самому.
Газобетон своими руками
Процесс производства состоит из нескольких этапов:
- подбор и смешивание компонентов;
- заполнение форм раствором;
- выдержка состава для набора прочности;
- извлечение из форм.
В универсальном составе для получения газобетона содержится цемент, песок, известь, алюминиевая пудра. Исходные добавки и их пропорции могут меняться, в зависимости от наличия сырья и требований к готовому стройматериалу. Например, в автоклавном производстве песок иногда заменяют золой или шлаком. А для получения стройматериала с меньшей плотностью можно делать газобетоны на основе смол ТЭС.
При изготовлении газобетона в домашних условиях необходимо правильно рассчитать соотношение расходных материалов и учесть особенности укладки и погрешности замеров. Но существуют и стандартные рецепты смеси для газоблоков, в которых указаны следующие пропорции:
- Цемент – 50-70 %;
- Вода – 0,25-0,8 %;
- Газообразователь – 0,04-0,09 %;
- Известь – 1-5 %;
- Песок – 20-40 %.
Данные вещества используются и при автоклавном производстве. Ориентируясь на приведенное в рецептуре соотношение, можно рассчитать приблизительное количество компонентов, которые войдут в состав на 1 м3 газобетона:
- Портландцемент – 90 кг;
- Вода – 300 л;
- Газообразователь – 0,5 кг;
- Известь – 35 кг;
- Песок – 375 кг.
Однако идеального состава в домашних условиях можно добиться лишь опытным путем, поскольку многое зависит от качества исходных компонентов. Повлиять на течение химической реакции может как температура воды, так и марка цемента.
Инструкция по самостоятельному изготовлению неавтоклавного газобетона
Для получения газоблока дома не потребуются сложная аппаратура и инструменты. Главное – четко следовать пунктам приведенного ниже пошагового руководства и использовать компоненты в определенном соотношении, а не «на глаз».
1. Исходя из указанных пропорций вычислить необходимое количество ингредиентов.
2. В первую очередь, необходимо смешать портландцемент с предварительно просеянным песком.
3. В полученную смесь влить воду и все тщательно перемешать.
4. Добавить в раствор другие компоненты. Алюминиевая пудра всыпается в последнюю очередь. В приготовлении как неавтоклавного, так и автоклавного газобетона одинаково важен процесс смешивания ингредиентов. Для равномерного распределения воздушных пузырьков лучше использовать бетономешалку.
5. Полученный раствор разливается в специальные формы, которые изготавливаются из металлических листов или деревянных досок. Чтобы застывший газобетон было легче достать, лучше использовать разборные конструкции. Кроме того, форму рекомендуют смазывать машинным маслом, разведенным с водой.
6. Заливать смесь нужно наполовину, поскольку она в процессе химической реакции расширяется практически вдвое. Этот процесс занимает около шести часов, после чего можно выравнивать блоки, срезая выступившую массу.
Формирование в этом случае длится дольше, чем для автоклавного газобетона – требуется не менее 12 часов, чтобы смесь затвердела. Для ускорения процесса застывания состава рекомендуют добавить растворимые соединения натрия (соду) на этапе приготовления раствора. Марочную прочность материал набирает после 28 дней выдержки. Готовый неавтоклавный газоблок, приготовленный своими руками, подходит для малоэтажного строительства, например, для возведения одноэтажного дома или гаража.
stroitel-list.ru
Газобетон своими руками в домашних условиях: технология
Газобетон – это универсальный материал, который обладает отменными прочностными характеристиками и является простым в монтаже. Поэтому материал широко применяется в строительстве. Для экономии денежных средств на этом процессе рекомендовано изготовление газобетона своими руками в домашних условиях.
Что такое газобетон и каковы его характеристики
Перед применением газобетона для возведения домов и других построек на участке, рекомендовано предварительно определить его характеристики.
Основные свойства и качества
Соответственно мировым стандартам качества и ГОСТу материал должен обладать перечнем определенных качеств. Качественный материал должен выдерживать 35-100 циклов заморозки и разморозки. Показатель теплопроводности газобетона составляет 0,09-0,38. Плотность материала составляет Д300-Д1200. Средний показатель паропроницаемости – 0,2. Усадка газобетона составляет 0,3 миллиметра на квадратный метр.
Виды материала и изделий из него
Соответственно характеристикам газобетона его разделяют на: теплоизоляционный, конструкционный, конструкционно-теплоизоляционный.
Теплоизоляционный газобетон имеет плотность от 300 до 400. Он имеет низкую теплопроводность и характеризуется незначитекльным весом. Применение материала рекомендуется для теплоизоляции помещений.
Конструкционный газобетон обладает отменными прочностными характеристиками и имеет плотность от 1000 до 1200. Благодаря высокому коэффициенту теплопроводности предоставляется возможность его применения в качестве утеплителя.
Наиболее популярным является конструкционно-теплоизоляционный газобетон. Он характеризуется плотностью 400-900. С его применением возводятся стены и перегородки.
Сильные стороны строений возведенных из газобетона
Материал широко применяется в строительстве благодаря наличию большого количества преимуществ:
- Для производства материала используется песок, известь, цемент, алюминиевая пудра и вода, что обеспечивает экологичность материала.
- Газобетон имеет небольшой вес, что упрощает процесс его укладки.
- Благодаря большим размерам газоблоков ускоряется процесс возведения газобетона.
- Материал характеризуется высоким уровнем стойкости к возгоранию.
- Газобетон является стойким к морозам, что позволяет его применять в суровых климатических условиях.
- Благодаря универсальному составу материала предоставляется возможность его распиловки и шлифовки.
- Газобетон позволяет использовать разнообразные материалы для отделки зданий внутри и снаружи.
- Такие показатели, как прочность и теплопроводность, являются оптимальными.
- Производство материала осуществляется различными компаниями, что позволяет клиенту выбрать наиболее приемлемый вариант для себя.
- Материал обладает паропроницаемыми свойствами, что позволяет обеспечить оптимальный микроклимат в помещении.
- Газобетон обладает хорошими звукоизоляционными свойствами, что обеспечивает комфортное пребывание в помещении.
Газобетонный дом имеет высокие эксплуатационные характеристики, что объясняется большим количеством преимуществ материала.
Недостатки изделий и их устранение
Перед тем, как сделать газобетон в домашних условиях, рекомендовано определить его недостатки. Материал является гигроскопичным, что приводит к усиленному водопоглощению. При отрицательных температурах накопленная в блоках влага кристаллизируется, что приводит к их разрушению.
Для того чтобы решить эту проблему нужно стены из газобетонных блоков облицовывать. С этой целью используется кирпич, металлопрофиль, дерево и другие отделочные материалы.
Производство газоблока своими руками
Технология производства газобетона в домашних условиях требует от мастера придерживаться определенных правил. Этот процесс состоит из нескольких этапов.
Необходимый набор оборудования и материалов
Перед тем, как изготавливать газобетон, нужно подготовить материалы и инструменты. Бетон делается из смеси таких материалов:
- Песок. Рекомендуется отдавать предпочтение кварцевому песку, который предварительно проходит процесс промывки и высушивания.
- Цемент. Высокопрочный материал получается при использовании цемента, который имеет марку более 400.
- Чистой воды.
- Негашеной извести.
- Алюминиевой пудры, каустической соды, сульфата натрия.
Формы
Перед тем, как делают газобетон, подготавливают формы. В строительных магазинах можно купить готовые изделия. Для экономии денежных средств их создают самостоятельно. Изначально изготавливают пенал из деревянных досок. В него вставляют перемычки, с помощью которых обеспечивается разделение каркаса на отсеки. Изготовление форм может проводиться из влагонепроницаемой фанеры. Для того чтобы зафиксировать доски, в них предварительно нужно сделать пропилы.
Размеры ячеек должны совпадать с размерами, которые в соответствии с проектом должен иметь готовый блок. Для того чтобы ускорить производственный процесс, рекомендовано провести одновременное сооружение нескольких форм. Для того чтобы исключить возможность прилипания раствора к формам, их нужно предварительно смазать специальным средством. В домашних условиях рекомендовано применение отработанного машинного масла, которое разводится водой в соотношении 1:3.
Для того чтобы ускорить изготовление газобетона можно использовать мобильные установки, которые состоят из компрессора, смесителя и соединительных рукавов. Предварительно подготавливаются приспособления, с помощью которых удаляются излишки бетона.
Приготовление раствора
Процесс изготовления газобетона в домашних условиях начинается с приготовления раствора. Количество используемых компонентов зависит от того, какой плотности материал пользователь хочет получить. Рассмотри вариант приготовления раствора для газобетона, плотностью 1600 килограмм на метр кубический. Для этого понадобится 1100 килограмм песка и 400 килограмм цемента. Компоненты тщательно перемешиваются. К ним нужно добавить 5 кг извести. Также в раствор добавляются такие добавки, как каустическая сода, алюминиевая пудра и сульфат натрия.
После тщательного перемешивания всех сухих компонентов, они заливаются 189 литрами воды. После перемешивания состава до однородности его можно использовать для заливки.
Заливка
После смазывания форм специальным составом, в них заливается раствор. При этом нужно следить, чтобы формы не заливались до краев, так как при застывании смесь вспучивается и излишки будут вылизать наружу. Формы нужно заливать до половины. После заливки материала наблюдается появление процесса газообразования. На следующем этапе проводится удаление излишков смеси с применением металлических струн. Процедура проводиться по истечению 5-6 часов после заливки.
Спустя 18 часов после заливки можно проводить распалубку изделий. Для того чтобы газобетонные блоки лучше отходили, нужно немного постучать по формам. По истечению месяца газобетон обретет техническую прочность. Затвердевание блоков наблюдается не только в помещениях, но и на открытых площадках.
Сравнение изделий самостоятельного и заводского выпуска
При производстве газобетонных блоков своими руками они затвердевают гидратационно, а на производстве – автоклавно. Эти материалы отличаются между собой по техническим и физическим параметрам. На производстве изготавливаются блоки стационарным и конвейерным способом. При использовании второго варианта снижается необходимость в участии человека к минимуму. В домашнем производстве материала человек принимает постоянное и непосредственное участие.
Рентабельность производства
На рентабельность изготовления блоков влияют разнообразные факторы. Она зависит от:
- Стоимости сырья;
- Вложений на покупку оборудования;
- Количества производственных отходов;
- Желаемого объема;
- Цели производства.
Специалисты провели расчеты в соответствии с показателями, в соответствии с которыми было установлено, что сделать газобетонные блоки своими руками дороже, чем приобрести готовый материал. Кроме того, этот процесс требует затрат сил и времени.
Газобетонные блоки – это универсальный строительный материал, который широко применяется для возведения зданий. Приобрести его можно на заводах и в строительных магазинах. Также можно провести изготовление блоков своими руками, предварительно рассчитав рентабельность этого процесса.
1beton.info
Технологический процесс производства газобетонных блоков
Сегодня технология производства газобетонных блоков интересует всех, кто планирует строить загородный дом или открывать бизнес по производству ячеистых бетонов. Ведь этот строительный материал является очень удачным выбором в плане прочностных и теплоизоляционных характеристик, и к тому же изготовление газобетона может быть достаточно выгодным бизнес-проектом.
Что нужно знать о ячеистом бетоне?
Газобетон представляет собой искусственный камень с микроскопическими воздушными порами. Еще одно его название — автоклавный ячеистый бетон, и оно само по себе говорит о технологии его производства. Газоблоки обладают прекрасными энергосберегающими характеристиками именно благодаря своей пористой структуре. Кроме того, они отличаются относительно небольшим весом, в том числе по сравнению с кирпичом и другими видами строительной керамики.
Газобетонные блоки — это строительный материал, который может использоваться как для возведения внутренних перегородок, так и для несущих конструкций. Он не подойдет для высотных зданий или промышленных объектов, но в индивидуальном строительстве он прекрасно себя зарекомендовал. Относительно легкие газоблоки не оказывают большой нагрузки на фундамент, что позволяет сократить расходы на устройство основания. Кроме того, они обладают большими размерами, и это позволяет ускорить процесс строительства.
Состав газобетонных блоков
Все перечисленные преимущества этого строительного материала обусловлены его составом. Все, из чего состоит газобетон, — это цемент, кварцевый песок и газообразователь, в роли которого выступает алюминиевая пудра. Некоторые производители добавляют в состав гипс, известь, золу, другие ингредиенты.
Таким образом, газобетон делается на основе сухих компонентов, которые размешиваются с водой. Для этих целей подходит любая техническая чистая вода, соответствующая требованиям ГОСТа 23732-79. При этом важна температура воды. Желательно, чтобы она была не ниже 45°С, поскольку это ускорит твердение блоков, повысит их прочность, а для предприятия это выгодно тем, что увеличится производительность линии в целом. Таким образом, многие производители подогревают воду, поскольку более высокая температура означает лучшее качество материала. А еще это помогает уменьшить количество используемого цемента, поскольку нагрев воды стимулирует активность сухих компонентов смеси.
Производство газобетона требует довольно серьезного подхода к выбору песка. Теоретически для этих целей подойдет как карьерный, так и речной песок, но важно, чтобы в нем содержалось как можно меньше илистых или глиняных частиц. Также важно выбрать размер зерен — не более 2 мм. Технология производства газобетона автоклавным способом позволяет заменить песок шлаком или золой, полученным от металлургических производств. Золы ТЭС помогают получить газобетон с меньшей плотностью. Это помогает дополнительно сократить расходы на производство материала.
Для изготовления газобетонных блоков необходим портландцемент марок М400 и М500. Лучше всего, чтобы портландцемент соответствовал требованиям ГОСТа 10178-85. А вот алюминиевая пудра должна быть марок ПАП-1 или ПАП-2 — она и выполняет роль газообразователя. Иногда для тех же целей применяется специальная паста. Это может быть и суспензия, поскольку пылевидный алюминий не так удобен при замешивании раствора. Могут применяться и суспензии на его основе.
На чем основано действие алюминиевого порошка? Он вступает в реакцию с цементным или известковым раствором, обладающим свойствами щелочи, и в ходе этого химического процесса образуются соли (алюминаты) кальция и газообразный водород, обеспечивающий формирование пор.
Для производства газобетона очень важно сделать правильный расчет расхода по каждому компоненту исходного сырья. Существуют стандартные рекомендации для автоклавных газоблоков. Исходя из такой рецептуры, на весь объем смеси берут 50-70% цемента, 0,04-0,09% алюминиевого порошка и до 20-40% песка. Кроме того, понадобятся вода (0,25-0,8%) и известь (1-5%). Таким образом, для того чтобы получить 1 кубометр газобетона, нужно взять до 90 кг цемента, до 300 л воды, извести — 35 кг, песка — 375 кг, алюминиевого порошка — 0,5 кг. Но это количество может быть скорректировано уже в условиях конкретного производства в зависимости от качественных характеристик самого сырья.
Какое оборудование понадобится?
Технология изготовления газобетона относительно проста. Тем не менее кустарными методами здесь обойтись не получится. Нужно приобрести специальное оборудование, которое обычно заказывают в комплексе у производителя или его официального представителя, — это наиболее выгодный вариант. Это не одна какая-то установка, это целый автоматизированный мини-завод. Иногда производитель даже предоставляет услуги специалиста, который проконсультирует относительно монтажа такой линии, поможет ее наладить и подобрать оптимальный состав для смеси, используемой для такого оборудования.
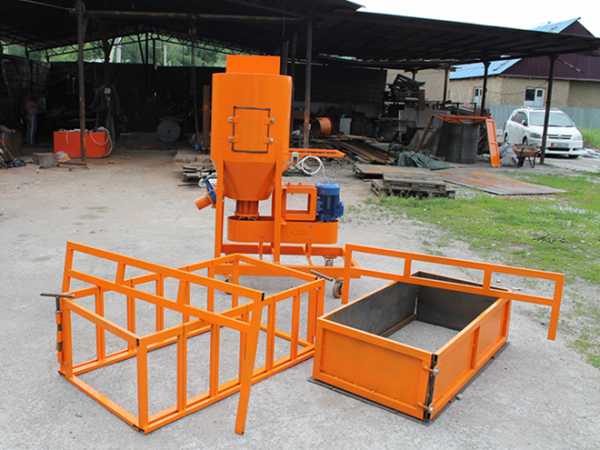
Мини-завод по производству неавтоклавного газобетона
В линию входят различные устройства, и теоретически каждое из них можно купить по отдельности, если по каким-то причинам одно выйдет из строя. Речь идет о таких вещах, как формы и предназначенные для их транспортировки передвижные поддоны, устройства для резки готовых блоков, смесители для газобетона, дозаторы для сыпучих материалов и т.д. Но главное — это печь-автоклав, ведь речь идет именно о производстве автоклавных газоблоков, отличающихся наиболее высокими качественными характеристиками.
Оборудование для производства газобетона делится на несколько типов. Выбор конкретного варианта зависит от требуемой суточной производительности, от того, сколько работников планирует нанимать предприниматель, и как будут организованы смены. Возможны следующие варианты:
- Стационарные линии обладают суточной производительностью до 60 кубометров готовой продукции. Как правило, для них нужны складские и производственные помещения площадью не менее 500 м². Главной особенностью таких линий является то, что формы подъезжают к стационарно установленному смесителю и там заполняются раствором, после чего выполняются все остальные технологические этапы. Это очень простая технология, для того чтобы обслуживать такую линию, достаточно нанять одного дополнительного работника.
- Конвейерные линии нужны там, где требуется большая производительность — до 75-150 м³ в сутки. Здесь производство осуществляется более быстрыми темпами (конечно, сроки созревания изделия не меняются, от линии это не зависит). Однако конвейерные линии требуют больших по площади производственных помещений, а для их обслуживания понадобится не менее 8 человек, хотя большинство технологических процессов здесь происходит в автоматическом режиме.
- Мини-линии не могут похвастаться высокой производительностью, до 15 кубометров готовых блоков в сутки. Отличием от стационарных линий является то, что движется в них смеситель, а формы установлены стационарно. Главное преимущество — им не нужны большие производственные площади, достаточно 140-160 м², так что в качестве стартового варианта они пользуются популярностью.
В частном строительстве часто используют мобильные установки, которые нужны для самостоятельного изготовления газоблоков. Это окупается, причем по расчетам специалистов расходы на строительство снижаются примерно на 30%. Мобильные установки поставляются в комплекте с компрессором. Работают они даже от бытовой электросети.
Этапы производства
Газобетон бывает двух видов — автоклавный или неавтоклавный. Последний вариант стоит дешевле, хотя полученный материал и отличается более низкой прочностью. Тем не менее из-за того, что себестоимость его изготовления ниже (не нужно покупать автоклав, содержать его, платить дополнительно за энергию), он является довольно популярным вариантом, поэтому его стоит рассмотреть подробнее. Если предприниматель намерен выпускать неавтоклавный газобетон, технология производства для него должна сводиться к следующим основным этапам:
- Точная дозировка всех описанных выше компонентов, а затем тщательное их перемешивание. При наличии соответствующего оборудования этот этап отнимает не более 10 минут.
- Подготовленную массу с помощью специального оборудования выгружают в специальные формы (их заполняют только наполовину, поскольку смесь будет увеличиваться в объеме в процессе газообразования). Этот процесс будет протекать в течение 4-х часов. За это время смесь заполняет отведенный ей в форме объем, а иногда даже его ей бывает мало. Тогда через 2 часа излишки можно будет убрать.
- Процесс выдержки изделий занимает около 16 часов, и по истечении этого срока происходит их распалубка и перегрузка на поддоны, где они будут набирать так называемую отпускную прочность. Этот этап отнимает еще 2-3 дня. После этого изделия можно отправлять на склад, но продавать их еще рано, поскольку свою марочную прочность они наберут только на 28-е сутки.
Изготовление газобетонных блоков с применением автоклава на первых этапах практически ничем не отличается от описанной выше технологии. Сначала нужно отмерить необходимое количество всех компонентов (желательно, чтобы это было сделано с помощью дозаторов, это поможет повысить точность). Затем всю эту массу загружают в смеситель и тщательно перемешивают. Иногда специалисты для этих целей предлагают использовать бетономешалку. Затем вводят газообразователь — это происходит через 10-15 минут перемешивания исходных ингредиентов. Алюминиевый порошок в любом случае вступает в реакцию с раствором, для этого ему не нужно автоклавирование.
Полуфабрикат разливают по формам, выдерживают положенные 4-6 часов, после чего производится нарезка газоблоков. До набора прочности они должны полежать еще 10-18 часов.
Но самое важное — знать, как делают автоклавирование после всех описанных выше процедур. Сформированные блоки перегружают в специальную печь, в герметичную камеру, где при высокой температуре каждый блок обрабатывают насыщенным водяным паром. Давление при этом также должно быть высоким — до 12 кг/см².
Неавтоклавный бетон сушат в естественных условиях, но для автоклавных изделий этого не нужно. Тем не менее и их нужно держать около 28-30 суток на складе, где они будут набирать марочную прочность.
Мало знать, как делать газобетон, нужно еще суметь доставить его потребителю. Для этого газоблоки пакуют в специальную термоусадочную пленку и транспортируют на деревянных поддонах.
kamedom.ru