Кладка газосиликатных блоков в холодное время года
Проблема строительства в холодное время года упрощается применением газосиликатных блоков. Идеальная геометрия этих материалов позволяет использовать все преимущества клеевой кладки. Газобетонные дома по теплосохранению, качеству внутреннего микроклимата и другим свойствам практически не уступают домам деревянным.
Преимущества газоблочных технологий
Доступная стоимость материалов дополняется несложным монтажом, экономией средств на отказе от обустройства внутренней или наружной теплоизоляции, переносом монтажных работ на осенне-зимний период.
- Газобетон Aerostone и другие аналогичные по параметрам автоклавные блоки могут монтироваться в любое время года.
- Обязательное условие – задействованные материалы должны отвечать требованиям действующих строительных стандартов. Цементно-полимерный клей для газоблоков рекомендуется использовать в температурном диапазоне от +5 до +25°С.
- Блоки Грас Малоярославец, цена которых находится в категории бюджетных строительных материалов, полностью доказали свою пригодность для монтажа в сложных погодных условиях.
При более высоких температурах блоки предварительно увлажняются. Эта мера не позволяет клеевому шву высохнуть до начала твердения.
Заказывайте у нас услугу обратного звонка, и наши специалисты с радостью Вам помогут!
Особенности блочного монтажа в осенне-зимний период
Для монтажа газоблоков при низких температурах используется предварительный подогрев самого материала горячим воздухом или более экономичными инфракрасными обогревателями. Также пользуется спросом повышение морозостойкости клея путем внесения специальных компонентов.
Внимание! Такой состав позволяет производить монтаж блоков при температуре до -10°С.
Для поздней осени предлагается еще один вариант – это применение быстротвердеющего клея. Швы уложенных при дневной плюсовой температуре блоков успевают схватиться до наступления ночных заморозков.
Как показывает практика, предложенные технологии зимнего монтажа газоблочных материалов достаточно эффективны. Возведенные при низкой температуре стены и перегородки по прочности и другим рабочим параметрам не уступают блочным конструкциям летней постройки.
Немногочисленные отрицательные отзывы – это следствие неправильного выбора материалов и допущенных в процессе монтажа ошибок.
Существенное преимущество газобетонных материалов – это возможность самостоятельного монтажа силами самого застройщика. В процессе монтажа газоблоки не создают особых проблем, поскольку обрабатываются простым инструментом.
Какой инструмент способен повысить производительность блочного монтажа?
- Для контроля вертикалей и горизонталей используется строительный уровень и отвес. Производительность блочно-монтажных работ и их качество можно повысить применением специального инструмента. В ассортименте имеются ручные пилы для резки газобетона с победитовыми зубьями, которые не тупятся даже после длительной эксплуатации.
- Инструмент для кладки газосиликатных блоков можно дополнить штроборезом для укладки металлической арматуры и рубанком, с помощью которого можно быстро выполнить зачистку поверхности блока или самой газоблочной конструкции.
- Полезным дополнением к основному перечню может стать угловой шаблон для ровной резки материала и производительная насадка к бытовой дрели, которая применяется для быстрого приготовления клеевого раствора.
При наличии определенных навыков качество выполненной кладки не уступает профессиональному уровню.
Заказывайте уже сейчас качественную кладку от опытных специалистов нашей компании!
строим стены из газобетонных блоков в мороз
Сооружения, возводимые на основе газобетона, очень популярны. Такой способ строительства доступен и относительно прост, что позволяет выполнить все работы самостоятельно даже при отсутствии специальных навыков и умений. Тем не менее, нужно знать некоторые тонкости работы с данным видом строительного материала, а также соблюдать технологию возведения.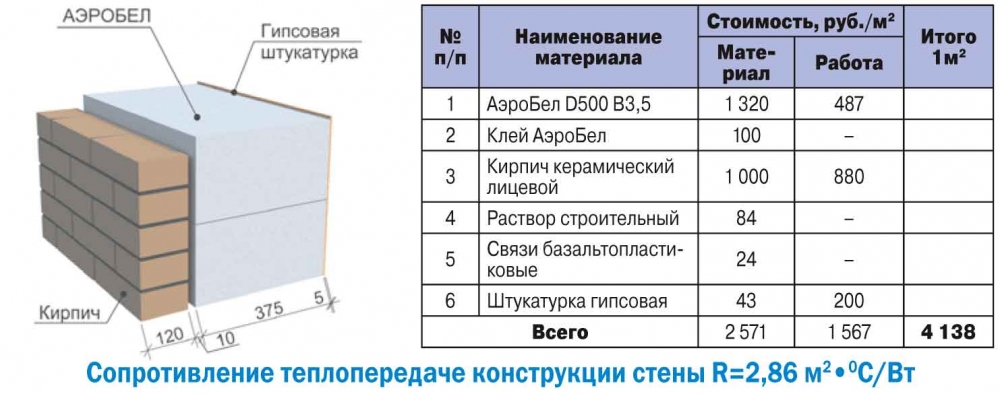
Именно при самостоятельном возведении стен из газобетонных блоков возникает риск не рассчитать свои силы, не уложиться по срокам за теплые летние месяцы, и тем самым заканчивать запланированные работы в осенние холода, а то и в зимние морозы.
Можно ли класть на клей?
Очень важно именно в летний период выполнить обустройство фундаментного основания, которое обязательно должно полностью застыть до наступления первых устойчивых заморозков. Только в этом случае могут успешно применяться технологии зимней кладки.
Важно!
Можно выполнять кладку в морозное время года, соблюдая определенные правила.Низкотемпературные условия способны осложнить строительные работы, которые связаны с затвердением цементных растворов, поэтому в холодный зимний период нужно осуществлять прогрев газобетона, а также использовать специальные противоморозные добавки. Опытные специалисты в строительной сфере рекомендуют совмещать применение химических и физических способов защиты с работами по прогреву укладываемых блоков и раствора.
Использование зимнего клея или добавок
Кладку рекомендуется осуществлять на тонкий слой клеевой смеси для газобетона.
Стандартные показатели расхода такого клеящего состава при толщине в 0,2 см значительно снижены, по сравнению с обычным цементным раствором, что позволяет получить оптимальный уровень теплопроводности.
Качественный зимний клей характеризуется высокой адгезией и влагостойкостью, а также обладает морозоустойчивостью, поэтому может быть использован в процессе шпатлевания и для выравнивания поверхности.
В основе клеящего состава лежит портландцемент, а также мелкозернистый песок. Особенностью является добавление полимерных добавок, улучшающих клеящие способности и показатели пластичности, а также модификаторов, которые минимизируют риск растрескивания.
Особенности
Зимние клеевые смеси в условиях отрицательных температур должны использоваться в первые тридцать минут после разведения горячей водой 60оС. Правильно приготовленный клеящий состав должен иметь температуру в 10-20оС. На блоки клеевой состав наносят с помощью кельмы в форме ковша.
Внимание!
Кладка в мороз предполагает обязательную очистку газобетона от снежной массы и наледи. Также блоки необходимо предварительно прогревать.Подводя итоги:
- При кладке в мороз обязательно использование зимнего клея для газобетона или противоморозных добавок в обычный клей.
- Клеевая смесь разводится горячей водой строго по инструкции, которую необходимо прочитать на упаковке.
- Блоки нужно прогревать непосредственно перед кладкой.
До каких температур можно работать?
Не все противоморозные добавки, выпускаемые на сегодняшний день отечественными и зарубежными производителями, соответствуют ГОСТу 24211-2003.
Справка
Качественный зимний клей для возведения газобетонных стен позволяет производить строительные работы в условиях температурных показателей до минус 10-15°C.При таких же показателях можно использовать кладочные смеси, предназначенные для возведения стен из газобетона в условиях малоэтажного строительства при отрицательных температурных режимах.
Использование стандартных, или так называемых «летних» кладочных смесей с добавлением противоморозной добавки «Антимороз» позволяет гарантированно выполнять строительные работы до температуры минус 15°C.
Не слишком ощутимое удорожание зимнего строительства вследствие приобретения специальных добавок и клеящих составов может быть компенсировано сезонным понижением цен на газобетонные блоки.
Полезное видео
Если вы всё-таки решили строить зимой, обязательно познакомьтесь с предлагаемым видео-сюжетом. Вы получить несколько важных советов от профессионального строителя.
Мы старались написать лучшую статью. Если понравилось — пожалуйста, поделитесь ею с друзьями или оставьте ниже свой комментарий. Спасибо!Отличная статья 58
Кладка стен из газобетона
Кладка последующих рядов несущих стен из газобетона выполняется только после армирования первого ряда блоков. Последующие ряды стены необходимо класть на тонкий слой клеевого раствора.
Кладка на клей возможна только при использовании газобетона с точной геометрией блока (погрешность 1,5мм – 2мм). Оптимальная температура для кладки газобетона находится в пределах от +5°С до +25°С. Если температура более высокая, газобетонные блоки рекомендуется смачивать водой, если температура более низкая в клеевой раствор необходимо добавлять противоморозные добавки.
Качество всей кладки зависит от первого ряда блоков, поэтому когда первый ряд положен, с его плоскости необходимо удалить рубанком все неровности – выступивший клеевой раствор, осколки и пыль. Проверка ровности выполняется при помощи уровня.
При использовании блоков с паз-гребнем, нет надобности формировать вертикальные швы. Это здорово облегчает и ускоряет работу мастера. Стена вырастет на глазах и уже через несколько дней можно можно устраивать армопояс и выполнять монтаж межэтажных перекрытий.
Перед кладкой последующих рядов , следует подготовить клеевой раствор. Клей для газобетона поставляется на строительство в мешках по 25 кг. В среднем расход сухого клеевого состава составляет 1 меш. на 1 м3 кладки газобетона.
Для приготовления клеевого раствора, не потребуется бетономешалка, лопата и песок. Достаточно строительного ведра и дрели с миксером.
Клеевой раствор приготавливается согласно инструкции, имеющейся на упаковке. Необходимо высыпать указанное количество смеси в соответствующий объем воды, и с помощью низкообротной дрели с миксером выполняется перемешивание компонентов. Затем клеевому раствору следует дать постоять несколькло минут, и повторить перемешивание. Полученный раствор должен иметь консистенцию густой сметаны. Использование клеевого раствора в разы снижает трудозатраты при кладке стен из газобетона.
Клеевой раствор необходимо распределять на поверхности блоков при помощи специальной кельмы или широго шпателя с квадратным зубом (размер зуба 3 мм – 4 мм, а шов между блоками не должен превышать 2мм – 3мм).
Ширина кельмы подбираеся согласно ширине блоков, при использовании кельмы достигается равномерное распределение клеевого раствора по всей поверхности блоков (нет потеков по бокам, стена – чистая).
Монтаж очередного ряда следует начинать с одного из углов. Каждый заложенный блок необходимо выровнять, с помощью того же уровня. После закладки углов нужно растянуть, как при монтаже первого ряда, шнур-причалку и полностью заполнить блоками ряд.
Кельмой раствор наносится на верхнюю поверхность не более двух-трех блоков. За время пока раствор остается подвижный, есть время положить очередные блоки и откорректировать их уровень.
Выполняя кладку стен из газобетона, не следует забывать о том, что вертикальные швы должны смещаться по отношению к предыдущему ряду, как минимум на 8 см.
Длина блока около отверстия или углов несущей стены должна быть более или равна 11,5 см.
Ровность кладки следует проверять после каждого положенного ряда. Углы здания проверяют деревянным угольником, а горизонтальность кладки контролируются с помощью уровня и правила. Правило кладут на кладку, сверху на него – уровень, и проверяют горизонт. При наличии незначительных отклонений, необходимо выполнить корректировку. Вертикальность кладки проверяется при помощи уровня, отвеса и 2- х метрового правила. Погрешность отклонения от вертикального уровня на 2-х метрах не должна превышать 1,5 мм — 2 мм. Необходимо помнить, что от ровности кладки газобетона будет зависить расход материалов для наружной и внутренней отделки стен.
В процессе кладки стен из газобетона следует выполнять армирование определенных рядов. Технология кладки газобетона предусматривает обязательное армирование первого ряда блоков, а также армирование каждого пятого ряда кладки и фрагменты ряда под окнами с выпусками в каждую сторону проема по 0,5 метра. Читайте далее об изготовлении и устройстве перемычек над оконными и дверными проемами.
Кладка из газобетона, инструкция
Быстро, точно, экономно — так, тремя словами, можно описать способ работы со строительной системой YTONG®. Характеристики и преимущества газобетона YTONG® проверены несколькими поколениями профессиональных строителей, поскольку это стеновой материал с 80-летней историей. Чтобы в полной мере ощутить все преимущества этого исключительного материала, необходимо соблюдать рекомендуемый технологический процесс.
Ответы на вопросы, касающиеся принятия оптимальных решений на этапе подготовки и выполнения работ, правильной кладки стен и использования отдельных компонентов системы YTONG®, Вы найдете в данной Инструкции. Она предназначается как для строителей, которые уже имеют опыт работы с системой YTONG®, так и для тех, кто только учится с ней работать. Знание Вами технологических операций облегчит и упростит проведение всех строительных работ и повысит их производительность. Результатом будут высококачественные постройки с прекрасными потребительскими качествами, которые будут долго служить своим владельцам и пользователям.
Использование упаковки
|
Блоки YTONG® поставлются на поддонах, защищенных от влияния атмосферных факторов фирменной термоусадочной пленкой. Во время производства строительных работ рекомендуется распаковывать поддоны и вынимать из них столько блоков, сколько можно уложить в течение одного рабочего дня. Блоки, которые остались на поддоне, нужно укрыть пленкой. | |
|
Пленка может быть успешно использована для защиты сооружаемых стен от воздействия осадков. |
Гидроизоляция фундамента
Перед началом кладки стен необходимо произвести проверку горизонтальности фундамента (плиты, ленточных фундаментов), а также, по необходимости, выравнивание. Допустимое отклонение составляет 30 мм.
|
Перед тем как приступить к кладке стен, следует выполнить гидроизоляцию фундамента. | |
|
Произведите точные обмеры контуров будущих наружных стен в соответствии с проектом! |
Первый ряд стены
Точность укладки первого слоя блоков YTONG® влияет на последующие ряды, а в результате — на точность строительства всего дома, поэтому данной операции необходимо уделить особое внимание!
|
Кладка первого ряда стен начинается с закладывания блока в каждом углу здания. | |
|
Первым закладывается блок в самом высоком углу здания, уровень которого определяется с помощью нивелира. Разница по высоте отдельных углов дома не должна превышать 30 мм. | |
|
Горизонтальное и вертикальное положение блоков контролируется с помощью уровня и при необходимости корректируется резиновым молотком. | |
|
Между установленными угловыми блоками растягиваем шнур-причалку и заполняем ряд. | |
|
Имеющиеся неровности кладки устраняем при помощи шлифовальной доски или рубанка. Мелкие загрязнения и пыль удаляем щеткой. |
Подготовка кладочного раствора
|
Для подготовки раствора YTONG® для тонкошовной кладки требуются простые инструменты: электродрель с установленной перемешивающей лопастью, пластиковая емкость для размешивания раствора и вода. | |
|
В чистую емкость наливаем необходимое количество воды в соответствии с инструкцией, приведенной на упаковке. | |
|
Добавляем сухую растворную смесь YTONG® и размешиваем до однородной массы. | |
|
Рекомендуется затворить водой сразу весь мешок раствора. Этого количества готовой смеси хватает для возведения приблизительно 1,5 м3 кладки газобетонных блоков. | |
|
Консистенция раствора должна быть пластичной, т. |
Резка блоков
|
Длина стен дома чаще всего не бывает кратной длине блока, поэтому появляется необходимость дополнения ее резаными блоками. | |
|
При строительстве частных домов резку блоков YTONG® проще всего осуществлять ручной ножовкой YTONG®. | |
|
Чтобы распил получился более точным, необходимо отметить карандашом линию резки на двух сторонах блока — горизонтальной и вертикальной. | |
|
Чтобы получить гладкую поверхность и обеспечить хорошее сцепление раствора с блоком, поверхность блока выравниваем рубанком или шлифовальной доской. | |
|
При строительстве многоэтажных домов для резки блоков рекомендуется использовать ленточную электропилу, которая обеспечит быстроту и безопасность резки. Блоки размещаются на передвижном столе пилы. |
Кладка несущих стен
К кладке очередных рядов стен следует приступать после схватывания цементного раствора, т.е. спустя 1–2 часа после кладки первого ряда.
Благодаря высокой геометрической точности раз меров блоков YTONG® последующие ряды кладем на раствор YTONG® для тонкошовной кладки.
|
Кладку несущих стен начинаем с закладки угловых блоков. Каждый уложенный блок требует выравнивания не только по горизонтали, но и по вертикали. | |
|
После закладки углов следует растянуть шнур-причалку, как это делалось при кладке первого ряда, и заполнить очередной ряд. | |
|
Наносим раствор YTONG® для тонкошовной кладки на горизонтальную поверхность блока с помощью кельмы YTONG® соответствующей ширины, затем, перевернув кельму, равномерно распределяем по всей поверхности блока. | |
|
Раствор также наносится на вертикальную поверхность блока посредством прижатия кельмы к нижней части вертикальной стенки блока и перемещением ее вверх, не отрывая. | |
|
Очередные ряды наружных углов кладем попеременно, используя перевязку. | |
|
Глубина плашковой перевязки должна составлять не менее 10 см. | |
|
Длина крайних блоков, например, на краях (дверных и оконных) проемов или углов здания должна быть ≥ 11,5 см. | |
|
Имеющиеся неровности кладки устраняем при помощи шлифовальной доски или рубанка. Мелкие загрязнения и пыль удаляем щеткой. |
Связка внешних и внутренних НЕСУЩИХ стен
|
Проверяем кладку в месте будущей стены; имеющиеся неровности устраняем рубанком. Тщательно очищаем поверхность кладки от пыли и загрязнений! | |
|
Несущая внутренняя стена связывается с наружной стеной кладкой при помощи перевязки. Первый ряд блоков кладется на цементно-песчаный раствор толщиной не менее 20 мм. При этом необходимо постоянно проверять совпадение уровней стен по горизонтали. | |
|
Уровень блоков выравнивается с помощью резинового молотка | |
|
Необходимо следить за точностью кладки блока по горизонтали и вертикали. | |
|
Деталь связки внутренней и наружной стен. При кладке используется инструмент YTONG®. | |
|
Раствор также наносится на вертикальную поверхность блока. |
Кладка перегородок
|
В соответствии с проектом дома обозначаем на несущей стене место для будущей перегородки. Разметка должна быть строго перпендикулярна фундаменту. | |
|
В месте, где будет перегородка, в клеевой шов вкладывается гибкая связь из нержавеющей стали. Анкеры одним концом монтируются в несущую стену, а другим концом — в шов перегородки. | |
|
Гибкие связи кладки закрепляются в шве гвоздями. Первый ряд блоков кладется на цементно-песчаный раствор. | |
|
При дальнейшей кладке необходимо следить за тем, чтобы раствор укладывался по всей ее ширине. Гибкие связи кладки вкладываются в каждый второй ряд блоков несущей стены. | |
|
Гибкие связи кладки можно монтировать в слой раствора и без гвоздей — путем вдавливания. | |
|
Анкеровка дополнительно возводимой перегородки. Гибкие связи крепятся к несущей кладке дюбелем. Для крепления перегородок к перекрытиям используются гибкие связи кладки или монтажная пена. |
Армирование под оконным проемом
|
Если ширина оконного проема более 1,80 м, то под предполагаемым окном в предпоследнем ряду блоков следует монтировать горизонтальную арматуру. Обозначаем на поверхности блоков планируемую длину оконных проемов. Длина арматуры должна быть длиннее оконного проема не менее чем на 0,5 м с каждой стороны. | |
|
При помощи ручного штробореза YTONG® в средней части кладки блоков делаем пазы, соответствующие длине арматуры. | |
|
Паз должен иметь размеры не менее 40 х 40 мм. | |
|
Тщательно удаляем пыль, которая образовалась при вырезке пазов. Благодаря этому раствор будет иметь лучшее сцепление с блоками. | |
|
Перед заполнением паза раствором и укладкой арматуры необходимо увлажнить паз водой. | |
|
Заполняем цементным раствором подготовленный паз до половины глубины. Для этого можно использовать и раствор YTONG® для тонкошовной кладки блоков. | |
|
Вкладываем в паз стальной стержень (арматуру), лучше всего — из профилированной стали диаметром не менее 6 мм. | |
|
После погружения стержня в цементный раствор полностью заполняем паз раствором, при необходимости удаляем мастерком его излишек. Выравниваем поверхность кладки, удаляем щёткой загрязнения и пыль. | |
|
Для продолжения работы нет необходимости в технологическом перерыве. | |
|
Приступаем к кладке очередного ряда блоков, который будет находиться непосредственно под оконным проемом. При этом необходимо следить за перевязкой блоков минимум на 10 см. | |
|
Блоки кладутся на тонкий слой раствора YTONG® для тонкошовной кладки. |
Перемычки YTONG® для несущих и ненесущих внешних и внутренних стен
|
Перемычки имеют высоту 125 мм и достигают своей несущей способности перекрытием как минимум одним рядом кладки блоков YTONG®. Необходимая ширина перекрытия получается из комбинации готовых перемычек YTONG® разной ширины. Глубина опоры составляет минимум 250 мм. В местах опирания перемычки укладываются на раствор YTONG® для тонкошовной кладки. | |
|
Для наружной стены толщиной 50 см можно использовать две перемычки шириной 175 мм и перемычку с шириной 150 мм. (Альтернативно — четыре перемычки с шириной 125 мм) | |
|
Перемычка укладывается так, чтобы напечатанная на ней стрелка указывала вверх. | |
|
При использовании комбинаций из перемычек связывание между ними осуществляется за счет раствора YTONG® для тонкошовной кладки. | |
|
Укладывание следующей перемычки. | |
|
Все перемычки должны плотно прилегать друг к другу. | |
|
Положение перемычки регулируется при помощи резинового молотка. | |
|
Укладывание следующей перемычки. | |
|
Укладывание следующей перемычки. | |
|
Неровности на поверхности перемычек выравниваются рубанком YTONG®. | |
|
После этого поверхность должна быть очищена щеткой от грязи и пыли | |
|
Если перемычки укладываются на блоки со стандартной высотой, то для достижения требуемой высоты стены может потребоваться выравнивающий слой из блоков. | |
|
Также перемычка может быть уложена на блоки с предварительным выпилом. Глубина опирания не менее 250 мм. | |
|
Максимальная длина перемычки должна составлять не более 1,25 м. При большей длине требуются дополнительные опоры. | |
|
Блоки укладываются на перемычку на раствор YTONG® для тонкошовной кладки. Вертикальные стыки при этом также осуществляются с применением тонкошовного раствора (вне зависимости от наличия системы «паз-гребень»). | |
|
Обратите внимание на то, что необходимо распределять раствор в стыках по всей поверхности блоков. | |
|
Блоки выравниваются при помощи резинового молотка. | |
|
Перемычки приобретают несущую способность после затвердевания раствора YTONG® для тонкошовной кладки. После затвердевания раствора поддержка монтажа может быть удалена. |
Перемычки из U-образных блоков YTONG®
|
U-образные блоки YTONG® являются элементами опалубки для железобетона. Железобетонная часть должна иметь соответствующее проведенным расчетам армирование. Для армирования лучше всего подходит пространственный арматурный каркас. | |
|
U-образные блоки YTONG® укладываются на подготовленное горизонтальное основание. Эту функцию отлично выполняет доска или брус. Основание должно иметь надежную опору, чтобы во время заливки перемычка не прогибалась. | |
|
U-образные блоки YTONG® укладываются на подготовленное основание так, чтобы глубина опирания перемычки составляла не менее 250 мм. | |
|
Вертикальные швы межд U-образными блоками заполняются раствором YTONG® для тонкошовной кладки блоков. | |
|
Проверяем ровность кладки U-образных блоков YTONG®. | |
|
Блоки выравниваются с помощью резинового молотка. | |
|
Закладываем и фиксируем арматурные каркасы. | |
|
Арматурные каркасы укладываются ближе к внутренней грани U-перемычки. | |
|
Между внешней стенкой U-перемычки и арматурным каркасом вкладывается теплоизоляция. | |
|
Изображение правильно подготовленной перед бетонированием перемычки из U-образных блоков YTONG®. | |
|
Перед началом бетонирования смачиваем водой U-перемычку. | |
|
Для бетонирования применяем бетон установленного проектом класса. | |
|
Тщательно уплотняем бетон. | |
|
Выравниваем поверхность залитого бетона. |
Перемычка приобретает несущую способность только после полного затвердевания бетона.
Удаление временных опор допускается только после достижения несущей способности перемычки.
Соединение кладки из газобетона YTONG® с другими материалами
Соединение блоков YTONG® с кладкой ограждающих стен из кирпича
|
При строительстве многослойных стен кладка ограждающей стены (как правило, из кирпича) крепится к несущей стене из блоков YTONG® при помощи гибких анкеров. Анкеры выполняются из нержавеющей или оцинкованной стали и устанавливаются из расчета всреднем не менее 5 шт. на 1 кв. м. Анкер размещается в шве между блоками YTONG® в процессе кладки стены, а затем, при возведении кирпичной стенки, отгибается и заводится в соответствующий шов кирпичной стены. | |
|
Крепление ограждающей кирпичной кладки к стене из газобетонных блоков YTONG® осуществляется при помощи специальных анкеров с передвижными влагозащитными шайбами. |
Соединение блоков YTONG® с железобетоном
|
Часто однослойные стены из блоков YTONG® используются как заполнение железобетонного каркаса. При этом места примыкания блоков к железобетону заполняются цементно-песчаным раствором. | |
|
Соединение стены, заполняющей каркас, с ж/б колонной или перпендикулярной ж/б стеной выполняется при помощи металлических связей, располагаемых через каждые 2-3 слоя блоков YTONG®. При этом одна часть связи помещается в шве кладки из блоков и крепится специальными гвоздями, а вторая часть крепится к боковой поверхности столба или стены. |
Примыкание блоков YTONG® к перекрытиям
|
Места примыкания блоков YTONG® к перекрытиям или балкам каркасной конструкции заполняются монтажной пеной, благодаря чему стена приобретает дополнительную устойчивость. |
Практический совет: как получить гладкую и ровную стену
|
Образовавшиеся при кладке блоков щели или неровности заполняем раствором, который получаем при смешивании раствора для тонкошовной кладки YTONG® с пылью, оставшейся после резки блоков YTONG®, или специальным раствором, предназначенным для этой цели. | |
|
Избыток раствора удаляем после его затвердения при помощи куска блока YTONG®. |
Монтаж сборно-монолитного перекрытия YTONG®
Складирование материалов
Балки складируются на ровной поверхности не более чем в 6 рядов.
Первый ряд балок укладывается на деревянные бруски толщиной не менее 5 см, шириной не менее 10 см. Расстояние между прокладками не более 1,5 метров, расстояние от концов балки до первой прокладки не более 1 метра. Каждый следующий ряд балок складируется на деревянные прокладки, толщина которых не менее 4 см и ширина не менее 8 см. Прокладки всех рядов балок должны быть расположены на одной вертикали.
«T»-образные блоки должны укладываться на ровное основание. Паллеты должны храниться на ровной, очень устойчивой поверхности, не более чем в двух уровнях. Блоки следует защищать от дождя и снега.
Монтаж сборных конструкций
Внимание! Перед началом работ следует помнить о том, что при монтаже нельзя использовать сильно поврежденные элементы (треснутая бетонная пята балки, деформированная или лопнувшая арматура, сломанный блок, блок с отломанным зубцом).
Монтаж балок производится вручную или с применением средств малой механизации.
При монтаже балки укладываются на очищенную горизонтальную поверхность стены. Если на верхней части кладки из блоков YTONG® имеются небольшие неровности, то их необходимо сгладить при помощи рубанка и создать ровную горизонтальную поверхность для опоры. В случае наличия ярко выраженных неровностей (более 15 мм), а также при пролётах более 6 м, рекомендуется использовать бетонную или цементно-песчаную стяжку М-100 толщиной не менее 50 мм, армированную согласно проекту.
Организация временных опор
|
Балки на время монтажа и бетонирования должны иметь промежуточные временные опоры — телескопические стойки и профильные трубы 80х40х3 мм в качестве подпорных реек. Несущая способность перекрытия, на которое передают нагрузку временные опоры, должна быть не менее 400 кг/м². | |
|
При отсутствии инвентарных телескопических стоек допускается использовать деревянные монтажные опоры в виде столбов диаметром 140-160 мм или брусков. Профильные металлические трубы допускается заменять подпорными рейками из досок сечением не менее 50х120 мм (или бруски размером не менее 100х100 мм), установленными горизонтально ребром вверх и закрепленными на опорных столбах или инвентарных телескопических стойках. | |
|
При этом расстояние между подпорными рейками и расстояние между опорными столбами (стойками), удерживающими одну и ту же подпорную рейку, должны быть не более 1,6 м. При использовании в качестве подпорок деревянных брусков или досок необходимо обеспечить прочность формы опорной конструкции за счет диагонального укрепления столбов с помощью прибитых досок в двух непараллельных направлениях. |
При возведении конструкций перекрытия в многоэтажных зданиях опоры под перекрытия устанавливаются соосно, т.е. опоры на каждом этаже здания должны устанавливаться ПО ОДНОЙ ОСИ.
Не рекомендуется ставить опоры на замeрзший грунт.
Чтобы обезопасить опорную конструкцию от погружения в землю и распределить нагрузку на нижнее перекрытие, под столбы необходимо уложить подкладки.
Перед началом сбора перекрытия необходимо произвести проверку правильности установки опорной конструкции!
Внимание! Запрещается использовать в качестве подпорных реек доски, имеющие сучковатую структуру, выходящую на опорную поверхность.
Внимание! Запрещается производить наращивание стоек из двух или более коротких досок. Таким образом, стойка должна быть изготовлена из единого элемента.
Монтаж Т-образных блоков YTONG® (блоков перекрытия)
|
Т-образные блоки YTONG® укладываются вручную вдоль продольного направления балок. Зазор между соседними блоками должен быть минимальным. | |
|
Первый и последний блоки перекрытия между двумя балками должны быть подогнаны к внутреннему краю опорной стены. Возможен вынос блока на стену при соблюдении достаточной ширины и армирования монолитного пояса, определенных проектом. | |
|
Блоки-вкладыши первого (от стены) ряда сборно-монолитного перекрытия опираются одной стороной на балку, а другой на стену или ригель. Минимальная зона опоры составляет 20 мм. Размеры блоков перекрытия разрешается корректировать путем распиливания. Блок с обработанным линейным размером всегда укладывается только крайним поверх стены с выносом минимум 20 мм. Для перемещения по уложенным блокам-вкладышам необходимо организовать настилы из досок толщиной не менее 30 мм или фанеры толщиной не менее 20 мм. На перекрытие, которое находится в состоянии установки, нельзя складировать стройматериал. | |
|
Если толщина внутренних несущих стен меньше 25 см, не рекомендуется укладывать балки в одну линию. При большей толщине стены балки можно укладывать в одну линию. | |
|
После монтажа сборных элементов перекрытия на верхние стержни арматуры балок укладывается арматурная сетка 100х100х5 мм. Ее положение, высота установки и связь с верхней арматурой балки определяется проектом. Стыковка отдельных сеток между собой осуществляются с нахлестом шириной не менее 150 мм. |
Монолитный пояс
Монолитный пояс — это элемент, связывающий несущие стены здания по всему периметру. Он фиксирует всю конструкцию здания, придавая ей пространственную жесткость. Монолитный пояс обычно устраивается в уровне межэтажного перекрытия и всегда выполняется замкнутым. Правильно собранный монолитный пояс способен воспринимать и распределять возникающие опасные нагрузки на стеновую коробку здания.
|
В перекрытиях длиной до 6 метров для армирования монолитного пояса монтируем минимум 3 продольных стержня Ø10 мм. Диаметр проволоки для хомутов = 4,5 мм, расстояние между хомутами = 250 мм. В перекрытиях большей длины для армирования монолитного пояса монтируем минимум 4 продольных стержня Ø12 мм. Диаметр проволоки для хомутов = 5,5 мм, расстояние между хомутами = 300 мм. | |
|
Монолитный пояс укладывается в уровне перекрытия и бетонируется одновременно с перекрытием. Продольную арматуру пояса необходимо последовательно связывать внахлест (длина нахлеста минимум 900 мм), также возможна сварка. Особо важной является стыковка арматуры в углах. |
Конструкция перекрытия
- Стеновой блок YTONG®
- Конструкция пола
- Бетонная заливка (В20), армированная сеткой
- Блок перекрытия YTONG®
- Штукатурка
- Балка перекрытия YTONG®
- Монолитный пояс
- Зона опоры блока перекрытия (мин. 20 мм)
Бетонирование
Внимание! Бетонирование производится при температуре выше +5°С!
|
Перед началом бетонирования сборно-монолитных перекрытий необходимо произвести контрольный осмотр опорных элементов конструкции на предмет соответствия их требованиям настоящей инструкции. |
Внимание! Перед бетонированием все поверхности элементов перекрытия необходимо очистить от мусора и пыли. В противном случае блоки-вкладыши могут не схватиться с бетоном.
Перед бетонированием перекрытие необходимо увлажнить.
|
Бетонирование монолитной части производится мелкозернистым (максимальная величина зерен — 10 мм) тяжелым бетоном классом не ниже В20 с использованием бетононасоса, крана с бадьей или тележек. При бетонировании следует избегать излишних концентрированных нагрузок, которые могут возникнуть при подаче большого количества бетонной смеси в одно место перекрытия. | |
|
Уплотняем бетон штыкованием или утрамбовываем с помощью вибратора. |
Арматура несущих балок, бетонной заливки и монолитного пояса должна быть перед бетонированием очищена от грязи, пыли и коррозии.
В случае возникновения визуального прогиба конструкции (прогиба опорных стоек или подпорных реек) при заливке бетоном работы на данном участке необходимо немедленно прекратить. Дальнейшие работы допускается проводить только после выяснения причин и устранения всех недоделок.
|
Бетонирование перекрытия ведется захватками. Ширина захватки не менее 620 мм. |
Внимание! Бетонирование захватки должно быть проведено за одну рабочую смену.
На период схватывания уложенную бетонную смесь необходимо предохранять от пересыхания и периодически увлажнять.
Внимание! Запрещается производить дополнительные укрепления опорных элементов во время проведения бетонирования данного участка перекрытия.
Внимание! При проведении бетонирования перекрытий КАТЕГОРИЧЕСКИ запрещается нахождение людей под перекрытиями!!!
Cнятие опор
Снятие промежуточных опор допускается только в том случае, если бетон набрал 70% проектной прочности. При средней температуре выше 10 градусов снимать опоры можно через 10 дней, от 5 до 10 градусов — через 20 дней.
При снятии опор необходимо следить за тем, чтобы не были повреждены отдельные фрагменты перекрытий, особенно блоки.
Полностью опорную конструкцию можно снять уже по истечении 28 дней, когда бетон достигнет нормативной прочности 20 МПа.
Прокладка внутренних коммуникаций
|
Отверстия для электрических розеток и выключателей высверливаются при помощи безударной низкооборотной дрели с нужной насадкой. | |
|
Наносим на стену линии прокладки внутренней проводки и коммуникаций. Для получения прямолинейных пазов прибиваем к стене направляющую доску. Пазы удобнее всего сделать с помощью ручного штробореза YTONG®, который направляется вдоль доски YTONG®. | |
|
Укладка проводки в газобетонных блоках |
Подготовка ниш
|
При подготовке ниш сначала помечаем на блоках размеры выреза. | |
|
Ручной или электрической ленточной пилой делаем перпендикулярные врезки на необходимом расстоянии друг от друга. | |
|
По горизонтали обозначенные места вырубаются молотком-киркой. | |
|
Ниша подготовлена и может быть использована, например, для канализационного стояка. |
Вследствие ослабления теплоизоляции не рекомендуется делать ниши в наружных стенах.
Раствор и инструменты YTONG®
|
Раствор YTONG® для тонкошовной кладки Благодаря минимальным отклонениям геометрических размеров блоков YTONG® их кладка легко производится на тонкослойный клеевой раствор. Наряду с увеличением скорости выполнения кладочных работ благодаря тонкослойной технологии выполнения швов, уменьшение толщины швов улучшает теплоизоляционные храктеристики стеновой кладки. | |
|
Кельма С помощью кельм, соответствующих толщине блоков, наносится тонкослойный клеевой раствор YTONG®. | |
|
Ножовка для ячеистого бетона Ножовка для ячеистого бетона YTONG® служит для быстрого изготовления доборных блоков, выступов и т.д. | |
|
Штроборез (резец) Штроборез служит для быстрого изготовления каналов, например, для прокладки электропроводки. | |
|
Рубанок для ячеистого бетона Предназначен для выравнивания существенных неровностей кладки. | |
|
Шлифовальная доска для ячеистого бетона Служит для удаления возможных шероховатостей на горизонтальной поверхности стены. | |
|
Уголок YTONG® Предназначен для ровного распиливания изделий из ячеистого бетона. | |
|
Шнур строительный YTONG® Применяется, как ориентир во время кладки стен и монтаже различных конструкций. Катушка 100 м. | |
|
Киянка YTONG® Специальный резиновый молоток для работы с газобетонными блоками. Обращаем внимание: металлический молоток серьeзно повреждает блоки. Для работы настоятельно рекомендуем использовать резиновый молоток. | |
|
Уровень YTONG® Используется для контроля уровней горизонтальных и вертикальных плоскостей. Длина 80 см. | |
|
Шпатель YTONG® Служит для заполнения сколов, щелей, неровностей и швов кладки изделий из ячеистого бетона. Длина 60 мм. |
Как класть газоблок
Как класть газоблок?
Как класть газоблок?
Работа с газоблоком достаточно простая, но, как и любое строительство, требует соблюдения технологии. Рассмотрим, как правильно класть газоблоки.
Кладка газоблока своими руками
Для начала работ, кроме самого стройматериала, потребуется монтажный раствор, арматура, необходимый инструмент (штроборез, киянка, шпатель, уровень, отвес, уголок для причалки и т. д.).
Для прочного соединения блоков без толстых швов используется специальный клей. На него усаживаются все ряды газобетонной кладки, кроме первого — он соединяется с основанием цементно-песчаным раствором. Его изготавливают из цемента марки М600 и песка в пропорции 1:3, разводя водой до вязкой однородной консистенции
Перед началом работ важно определить самую высокую точку фундамента. Для этого по углам основания выставляются маяки. Если есть даже минимальные перепад высот, его можно компенсировать слоем раствора. Там, где фундамент выше, раствора наносится меньше. На низшей точке укладывается слой потолще. Главное — вывести кладку первого ряда в одну ровную плоскость.
Перед началом застройки фундамент обязательно покрывается слоем рубероида для гидроизляции.
Правильная кладка газоблока начинается с выведения угла. Обычно выстраивается пара-тройка рядов угловой конструкции, её проверяют с помощью уровня и отвеса.
Далее между блоками первого и второго ряда крепится специальный уголок и натягивается причалка, по которой можно сверять горизонтальность кладки. Она обозначит верхнюю границу ряда. Корректировать положение блоков во всех плоскостях легко резиновым молоточком (киянкой). Высота ровняется утапливанием блоков в раствор или добавлением смеси, когда высоты не хватает. Ориентироваться нужно на слой шва в среднем 2-3 см. Клееные швы будут в 10 раз тоньше — по 2-3 мм.
Далее цепным методом блоки выкладываются друг за другом. Если в их конструкции не предусмотрено пазогребневое соединение, клей обязательно наносится на торцы изделий. При соединении паз-гребень клеем должны промазываться наружный и внешний вертикальный шов, чтобы впоследствии он не продувался.
Кладка первого ряда газоблоков должна быть идеально ровной, так как является основой для всего будущего строения. Даже небольшой крен может привести к быстрому появлению трещин и разрушению стены.
Чтобы раствор полностью схватился, рекомендуется выждать пару часов и приступать к армированию первого ряда. Есть два варианта. Либо поверх блоков укладывается базальтовая сетка (ссылка на статью Применение базальтовой сетки) с утапливанием клей. Либо в газоблоках делаются две параллельные штробы, в них размещается металлическая арматура диаметром 8 мм. Так опоясывается весь периметр. Обратите внимание, что арматура должна полностью утапливаться в клей, чтобы не началась коррозия.
Укрепление газобетона арматурой проводится в первом ряду, в последнем, в ряду укладки межэтажных перекрытий, над и под оконными проёмами. Также армируют каждый четвёртый ряд кладки. В сейсмоактивных зонах, при использовании газобетона малой плотности, а также при строительстве из газоблоков цоколя или подвала проводится вертикальное армирование.
При кладке газоблока своими руками должна соблюдаться правильная перевязка. Вертикальные швы не должны совпадать в рядах, для этого блоки кладутся со смещением в пол-изделия.
В местах соединения внешних и внутренних стен нужно делать сопряжение. В качестве жёстких связей используется тот же газобетон — делается перевязка.
Также можно применять стальную арматуру. Когда стены имеют разную нагрузку, устраивают гибкие связи с помощью базальтовых или композитных стержней.
Выше мы упоминали, что межэтажные перекрытия должны опираться на армированный ряд или пояс. При этом торцы железобетонных плит для лучшей теплоизоляции закрываются доборными блоками, а швы — промазываются раствором.
Зная эти основы, как класть газоблоки, вы сможете построить долговечный, прочный и тёплый дом. А купить все необходимые материалы для него легко в ТД «Пораблок». У нас представлен автоклавный газобетон разных габаритов и плотности, также в наличии стальная и базальтовая арматура, клей для кладки из газобетона. Оформляйте заказ прямо на сайте!
Как правильно класть газобетонные блоки
Сопряжено возведение построек из газобетона с некоторыми особенностями. Ячеистые бетоны обладают существенными отличиями от кирпича или шлакоблока. Поэтому наивно полагать, что вот так просто построить можно дом из относительно не дорогостоящих газобетонных блоков. Поэтому полагать наивно, что можно поострить вот так дом из относительно дешевых газобетонных блоков. Следует перед началом работ изучить внимательно не только качества газобетона, но и его технологию укладки. Также немаловажно знать условия, при которых получиться конструкция максимально долговечной и надежной.
Как правильно класть газобетонные блоки
Укладываются газоблоки намного проще, чем шлакоблок или кирпичи. Объясняется это наличием практически ровных поверхностей этих блоков, даже при наличии весьма небольших выступов ил прочих изъянов, газоблоки выравниваются легко в одном ряду с помощью обыкновенных режущих инструментов, поскольку его распиливать можно даже обыкновенной ножовкой или пилой.
Начинают монтаж газобетонных блоков с угла, который выше всех расположен. Проверяется гидроуровнем каждый уложенный ряд.
Начинается строительство с фундамента. Как правило, далека его поверхность от идеала. После укладки гидроизоляции, с этой целью, покрывают фундамент слоем цементного раствора. Кладут на этот раствор первый ряд. Благодаря толстому относительно слою раствора добиваются идеальной ровности блоков первого ряда. Нижние поверхности первого ряда блоков увлажняют для предотвращения всасывания ими из раствора влаги.
Калькулятор газобетонных блоков
В сети можно найти большое количество ресурсов, которые дают возможность осуществить расчет необходимого количества газобетонных блоков. Вам для этого необходимо указать следующие данные вашего строения:
- Площадь дверей и окон, которые размещаются на перегородках.
- Габариты блоков, которые применяются для создания перегородок.
- Суммарная длина всех внутридомовых перегородок.
- Площадь окон и дверей.
- Стоимость одного кубического метра материала.
- Габариты самого блока, который использовать будете вы.
- Высота стен
- Общая протяженность наружных стен.
Помогут вам данные расчеты подсчитать точное количество газоблоков, а также их приблизительную стоимость.
Краткая инструкция по кладке
Обязательно уложен должен быть первый ряд блоков на слой гидроизоляции, который материал защитит от подсоса из фундамента влаги. Укладывается самый первый ряд блоков не на клей, а на обыкновенный цементный раствор. Желательно кладку начинать с углов, между ними протянув разметочный шнур.
Если в ряду в оставшийся промежуток обладает меньшей длиной, чем целый блок, то осуществляют вырезание блока по заданным размерам. Укладываются очередные ряды на клеевой раствор с обязательной перевязкой, как при кладке обычного кирпича. Производится нанесение клея на газоблоки специальной кареткой или шпателем, ширина которой равняется ширине кладки. Также желательно боковые стороны блоков промазывать клеем, особенно, если последующая отделка одной из сторон помещения отсутствовать будет.
Не должен быть толстым слой клея, поскольку обеспечивает он превосходное соединение швов даже при самом минимальном расходе. Достаточно разные цены на клей и зависят полностью от его объема, а также марки производителя.
Производится выравнивание блоков по уровню деревянным или резиновым молотком.
Армирование кладки
Необходимо уяснить, что не укрепляет кладку армирование, а только предотвращает появление на стенах трещин. Тем не менее, рекомендована данная операция при сооружении любого крупного объекта. Не все ряды армируются, а лишь некоторые, наиболее уязвимые участки. Это зоны под опорными проемами, первый ряд кладки, опорные зоны, места расположения перемычек. Армируется по длине верхняя часть газоблоков.
Двух видов может быть материал для армирования:
- Каркас из двух рядов стальной проволоки, между собой жестко между собой соединенных более тонкими перемычками. Одним слоем укладывается каркас.
- Стальная арматура сечением 6-8 миллиметров. Требует армирование укладки параллельных двух рядов арматуры.
Необходимо перед закладкой арматуры в газобетоне прорезать штробы. Используют для этого обыкновенный штроборез. Очищают от пыли штробы и наполняют их клеем. Затем укладывают в них армировочный материал, удаляя при этом остатки клея.
Что необходимо при монтаже газобетонных блоков
Обеспечивает гидроизоляция газобетона защиту от влаги блоков, поэтому между фундаментом и стенами ее наличие должно быть обязательно. Гидроизоляция может быть обмазочная или рулонная.
Уверенно удерживает газобетон в себе всевозможные виды крепежа. В стенах превосходно держатся саморезы, анкеры всевозможных конструкций и пластмассовые дюбели. Могут быть сердечники дюбелей как пластмассовые, так и металлические. Держатся немного хуже в блоках забивные гвозди, но если подвесить на них что-либо, то не беспокоиться можно насчет надежности этого крепления.
Для того чтобы в газобетоне проделать штробу применяют ручные и электрические штроборезы. Особенностями ручного инструмента являются низкая стоимость и потребность прикладывания всевозможных для работы физических усилий. Комфортнее и быстрее работать электрическими моделями, но и стоят они больше.
Применяется для кладки специализированный раствор, который покупается в сухом виде и разводится при помощи воды. Можно, конечно же, газоблоки укладывать на цементном обыкновенном растворе. Однако качество подобной кладки будет очень сомнительным вследствие возможного появления мостиков холода.
Как правильно штукатурить газобетон
Для того чтобы защитить газобетон от образования усадки и трещин необходимо ограничить к нему поступление влаги. Газобетонные блоки для этого штукатурят. Однако выполнять данную работу стоит правильно, иначе только можно испортить всю работу.
Высокой паропроницаемостью должен обладать штукатурный раствор во избежание накопления внутри дома сырости. Производится вначале обязательное покрытие стен специальной грунтовкой на основе акрила. Повышает он адгезию штукатурки и прохождению воздуха не препятствует.
Затем наносится на стены раствор, в который и утапливается армирующая сетка. Наносится после этого финишный штукатурный слой. Стены зачищаются после его высыхания и окрашиваются фасадной краской, которая располагает особенными качествами паропроницаемости.
Технология строительства из газобетонных блоков
Рекомендуется выполнять строительство любых сооружений из газобетона при теплой погоде, более +5 градусов, но при этом не выше +25. Если в жару приходиться работать, то нужно смачивать водой поверхности блоков. При работе в холодное время необходимо в клеящий состав добавлять специальные противоморозные присадки.
Готовится клей для кладки перед непосредственным началом работы. Вливается в сухую смесь вода и тщательно перемешивается до необходимой густоты. Используются для укладки наружных стен газоблоки 375-400 миллиметров толщиной, соответственно, такой же и будет толщина готовой стены. Все перегородки, если необходимы они, выкладываются блоками 200-250 миллиметров.
Не должно быть между стоящими рядом блоками перепадов уровня. Приведут перепады к образованию мостиков холода и вертикальных трещин. Для выравнивания ряда, после его укладки, осуществляется зачистка поверхности газобетона при помощи специального рубанка.
Укладка газоблоков: основные моменты при работе
Возвести любое строение можно в короткие сроки, если использовать такой строительный материал, как газобетон. Небольшой вес, легкость в обработке и большие размеры газоблоков – все эти свойства позволяют возвести дом своими руками в максимально короткое время.
Учитывая все преимущества газобетона и пеноблоков, разработаны основные требования и рекомендации:
- Применение газоблоков, соответствующих требованиям ГОСТа.
- Кладка газобетона производится тремя способами: одним блоком с применением порядовой цепной перевязки, два блока — вертикальная порядовая перевязка и два блока со связью слоев дюбелями или анкерными пластинами.
- Кладка из газобетона производится на клеевую смесь.
Какие блоки использовать
Класть стены рекомендуются газобетоном, соответствующим требованиям ГОСТа. Несущие стены из пеноблока необходимо возводить из блоков, изготовленных автоклавным методом. Это касается кладки стен высотой до 20 м.
Какой клей использовать
Кладка газоблоков осуществляется на тонкослойную клеевую смесь. Расход клея при толщине слоя 2 мм значительно ниже, если бы использовался обычный цементный раствор. Такая толщина клея имеет низкую теплопроводность.
Основные способы кладки
Такой вопрос, как класть пеноблоки, какой способ выбрать, зависит от вида стены (наружная, внутренняя, несущая, самонесущая), от этажности (последующей нагрузки).
- Укладка одним пеноблоком с применением порядовой цепной перевязки. Если толщина стены не более 300 мм, кладка газобетона производится толщиной в один блок.
- Укладка двумя пеноблоками с использованием вертикальной порядовой перевязки, величина — 0,5 толщины стены из пеноблоков. Также возможен вариант с перевязкой блоков, используя тычковые ряды через каждых два ряда.
- Укладка двумя пеноблоками — вертикальная порядовая перевязка и два блока со связью слоев дюбелями или анкерными пластинами. При этом методе между слоями блоков прокладывается паропроницаемый утеплитель. Для связевых элементов используются стержневая арматура с антикоррозийным покрытием, толщина 2 мм, нержавеющая сталь, стеклопластиковые или базальтопластиковые элементы. Они устанавливаются в клеевые швы кладки из пеноблоков.
Подготовка и технология кладки
Подготовка газоблоков
Газобетонные блоки продаются как в упаковке, так и без нее. Лучше приобретать упакованные в полиэтиленовую пленку блоки и распаковывать по мере использования. В этом случае газобетон будет защищен от атмосферных осадков. Перед использованием необходимо снять упаковку и дать проветриться блокам.
Подготовка клеевого раствора
Как правильно разводить клей? На упаковках клея, предназначенного для пеноблоков, дается подробная инструкция по приготовлению, которую необходимо строго соблюдать. Клеевая смесь разводится в теплой воде и перемешивается в миксерах, бетономешалках до образования однородной без сухих частиц массы. Отметим, что свежеприготовленный раствор сохраняет свойства 3 часа, поэтому не стоит замешивать большое количество, а уже имеющийся раствор желательно периодически перемешивать.
Подготовительные работы перед укладкой первого ряда
На готовый фундамент производится укладка пеноблоков первого ряда. Между ними необходимо произвести горизонтальную гидроизоляцию. Она тем самым предотвратит в последующем капиллярный подсос. Для гидроизоляции применяется битумный материал. В местах стыков или углах рулоны настилаются внахлест до 10 см. Если поверхность фундамента неровная, можно своими руками приготовить выравнивающую смесь из расчета 1/3 цемента и песка.
Нивелировка углов, примыканий
Как укладывать пеноблоки первого ряда ровно? Для этого производится нивелировка углов, устанавливаются угловые маячные пеноблоки. По углам устанавливаются блоки, выравниваются с помощью уровня, при необходимости положение корректируются резиновым молотком. Далее натягивается шнур и располагается на верхнем уровне газоблока и на расстоянии до 3 мм от них. Для того чтобы не было провисаний, по середине стены можно установить дополнительный маячный пеноблок. В дальнейшем шнур монтируется уже в швах кладки.
Нанесение клея
На подготовленную очищенную от мусора и пыли поверхность наносится клеевая смесь. Используя зубчатый шпатель, клей наносим своими руками и на боковые поверхности уложенных ранее газобетонных блоков. Готовая консистенция смеси такова, что при использовании зубчатого шпателя (либо используется кельма), бороздки смеси не слипаются. Толщина клея около 2 мм. При сухой погоде рекомендуется увлажнять поверхность блоков перед нанесением клеящего раствора.
Укладка блоков
Далее на клей производится укладка блоков своими руками. В течение 15 минут газобетонные блоки еще можно корректировать. После высыхания необходимо шлифовальной доской убрать все неровности, то есть выровнять поверхность, удалить пыль. Только потом можно приступать к последующей кладке пеноблоков. Шлифование уменьшит в последующем расход клея, сделает кладку своими руками более точной. Для распиливания блоков обратитесь к обзору инструментов для работы с пеноблоками.
Армирование кладки
Отчего возникают трещины на конструкциях из пеноблоков? Причин этому множество: оттаивание грунта, перепады температуры, неправильно рассчитанная нагрузка на стены, раствор, приготовленный с нарушениями, толстые швы. Перед тем, как правильно укладывать пеноблоки, необходимо предусмотреть все факторы, способствующие впоследствии к возникновению трещин и деформаций стенных конструкций.
- опорные поверхности,
- каждый 4-й ряд,
- длинные стены для повышения сопротивления нагрузкам (боковой ветер),
- части стены, если предполагается большая нагрузка,
- первый ряд, который лежит на фундаменте,
- нижние блоки оконных проемов.
- кладка зимой
Пенобетон является ячеистым материалом, что является как преимуществом, так и недостатком. Плюсы состоят в том, что материал имеет низкую теплопроводность. Недостатком является его высокая влаговпитываемость.
Кладку из газобетона, не рекомендуется проводить во влажное время и при низких температурах зимой.
Рекомендации при выполнении кладочных работ из газобетонных блоков зимой
- Проводить кладку своими руками только при сухой погоде, температуре от +5°С,
- Применение зимнего клея для ячеистого бетона, имеющего противоморозные добавки,
- Добавлять зимой при замешивании клеевого раствора теплую воду,
- Клеевую смесь использовать в течение получаса,
- Хранение газобетонных блоков, мешков клея в помещении при температуре от +5°С,
- Перед тем, как класть пеноблок, тщательно очистите поверхность от пыли, излишков раствора от предыдущего ряда и разровняйте клей зубчатым шпателем,
- При перерывах верх кладки необходимо накрывать зимой водоотталкивающим материалом. Это предотвратит проникновение влаги в блоки,
- Кладку в одноэтажных домах, где площадь не превышает, как правило, 100 м2, производить своими руками можно в тепляках, которые защищают всю строительную площадку. Тут используются для прогрева воздуха тепловые пушки.
Мы рассмотрели основные моменты при укладке газобетонных блоков. Если ответственно подойти к делу нужно учесть основные моменты:
- Выбор газобетонных блоков соответствующих ГОСТу,
- качество клея,
- армирование,
- обвязка углов,
- нивелир,
- теплое и сухое время года.
Только в этом случае постройка будет радовать вас долгие годы.
Как класть газоблоки?
Газоблоки имеют множество неоспоримых преимуществ перед различными другими строительными материалами. Газоблоки отлично сохраняют тепло в помещении, а также очень удобны в кладке.
Прежде всего, следует обратить внимание на тот факт, что газоблоки делятся на три типа. Типы газоблоков определяются их плотностью.
Для возведения ответственных зданий, а также для кладки несущих стен, используют газоблоки типа d 500. Данные газоблоки обладают самой высокой плотностью из всех. Однако такие блоки не рекомендуется применять для возведения перегородок, а также для строительства не несущих конструкций. Газоблоки типа d500 обладают большим весом и массой, поэтому увеличивается нагрузка на фундамент.
Газоблоки типа d 400 обладают средней плотностью и массой. Использовать данный тип газоблоков можно также для возведения несущих стен здания. Однако для особо ответственных строений лучше выбирать тип d 500.
Газоблоки третьего типа d 300, обладают наиболее низкой массой и плотностью. Такие газоблоки называют теплоизоляционными. Они не выдерживают больших нагрузок, зато используется в качестве строительного материала для возведения перегородок. Газоблоки типа д 300 также успешно применяют в качестве надежного утеплителя.
Для кладки газоблока используются цементный раствор и специальный клей. Первый ряд газоблоков всегда укладывают на цементный раствор, а все последующие на клей.
Для приготовления цементного раствора берут одну часть портландцемента и три части песка. Данное соотношение нарушать не рекомендуется. Дело в том, что за столетия беспрерывный практики, строители уже нашли оптимальное соотношение ингредиентов, для приготовления кладочного раствора и улучшить его вряд ли получится. Зато легко можно ухудшить свойства раствора, если допустить просчет.
Кладку газоблоков начинают с возведения углов здания или постройки. Точно так же как при кладке обычных кирпичей, следует строго соблюдать укладочные швы. Проверяют вертикальную, а также горизонтальную плоскость кладки. Делать это удобно при помощи отвесов или уровня.
Когда углы будут выложены, между ними натягивают шнур. Данный шнур будет символизировать внешний край будущей стены. Крепят шнур к верхним углам газоблока. Разумеется, шнур необходимо натянуть как можно ровнее. Поэтому во время натягивание шнура, также не помешает воспользоваться строительным уровнем.
После этого очень легко соблюдать ровность кладки. Следует лишь ориентироваться на уровень шнура. Однако, через каждые несколько рядов, необходимо проверять как горизонтальность, так и вертикальность кладки. Для этого используют те же уровень и отвесы.
Кладку газоблоков выполняют точно также как и кладку кирпича. То есть каждый из рядов смещают на полблока, а при возведении двойной кладки осуществляют перевязку. Перевязка – это просто. Данный прием означает, что через каждые несколько рядов блоки кладут не вдоль возводимых стен, а поперек них. Это нужно сделать для того, чтобы получить монолитную стену, а не отдельно стоящие и независимые стенки или даже столбики из блоков.
Кладка газобетонных блоков
Газобетонные блоки — это искусственный камень, который легко поддается обработке: резке сверлению и другим, необходимым в ходе строительства действиям. Благодаря своим размерам и уникальным свойствам кладка газобетонных блоков идет быстрыми темпами.
Расчет количества газобетонных блоков для строительства дома
Расчет производится в соответствии с проектом дома, котором четко определена кубатура строительства. В соответствии с этими данными и производится закупка блоков и смеси для соединения блоков между собой.
Смесь продается в сухом виде. В ее состав входит цемент, песок и различные клеевые добавки. Сухая смесь разводится водой в соответствии с рекомендациями производителя. Готовая смесь должна быть использована в течение 40 минут. Применяют и специальный клей для соединения блоков между собой.
Кладка из газобетонных блоков
Первый ряд блоков из газобетона укладывается на подготовленный и выровненный фундамент, надежно изолированный при помощи рубероида, проверяется при помощи уровня. Толщина шва не должна превышать 3 мм., высвободившийся раствор не затирается, а тщательно убирается. Если уровень нарушен незначительно он, как правило, убирается за счет второго ряда.
После того как первый ряд уложен при помощи отвеса и деревянного угольника, проверены углы по всему периметру, натягивается бечевка, которая будет служить ориентиром для дальнейшей кладки. Бечевка натягивается от внешнего края угла до следующего угла.
Если стена длинная и есть вероятность провисания бечевки, устанавливают дополнительные маячки по периметру стены. Бечевка поднимается каждые 3 – 4 ряда. Все зависит от квалификации мастера. Каждый ряд проверяется отвесом по вертикали и уровнем по горизонтали.
Правило кладки газобетонных блоков
Так же как и в кирпичной кладке чтобы избежать мостиков холода, а нагрузку на фундамент распределить равномерно кладу газобетонных блоков кладут со сдвигом на половину блока, распиленного всеми доступными способами. Каждый последующий ряд должен полностью перекрыть швы предыдущего ряда.
Кладка газобетонных блоков делается на готовые смеси или на смеси приготовленные самостоятельно из цемента песка и воды. В этом случае шов будет от3 мм до 10 мм. В настоящее время используются для соединения газобетонных блоков специальный клей. При его использовании толщина шва будет всего 1,5 мм. Кладка смотрится более цельной и аккуратной.
Армирование кладки из газобетонных блоков
Одним из недостатков газобетонных блоков является то, что в процессе эксплуатации на стенах в блоках могут появиться трещины, ликвидировать которые бывает крайне сложно или даже не возможно, что может привести к разрушению все кладки. Это происходит от неравномерно распределенной нагрузки, под действием которой в блоках возникает напряжение. Оно и становится причиной появления трещин.
Для того чтобы избежать этих неприятностей каждый пятый ряд армируют. Чтобы арматура не выделялась и не приводила к образованию мостиков холода, в блоках проделывают канавки и в них закладывают арматуру.
Арматуру закладывают в углы под оконные и дверные проемы. Эта процедура приводит к удорожанию строительства, но как показывает практика армирование оправдано. Канавки заливают клеем или смесью, а затем кладут арматуру. Клей станет хорошим консервантом металла от коррозии.
Правильная кладка газобетонных блоков имеет свое дальнейшее развитие, не так давно стали выпускать монтажную пену, при которой сокращаются проемы между блоками и она не создает промерзающей прослойки, что свойственно клею, так как в нем присутствует цемент.
5 правд о том, можно ли строить из газобетона осенью
На дворе середина осени, и многим домостроителям приходится принимать решение, строить или не строить. Дело в том, что традиционно большинство строительных этапов проводится весной и летом. Считается, что осенне-зимняя стройка и стоить будет дороже, и выйдет некачественной. Так ли это? Давайте посмотрим, например, на строительство осенью дома из газобетона.
Главные опасения критиков связаны с дождями и холодом, которые действительно осложняют процесс. Даже летом и даже кирпичную кладку не ведут в дождь. А тут осень… А что если вода попадет внутрь блоков, а потом ее заморозит, не разорвет ли газоблоки?
Правда №1. Гигроскопичность газобетона довольно высока – это правда. Если полностью погрузить элемент из газобетона под воду, то в течение суток он наберет до 40% воды от своего общего объема. А если вынуть и оставить на просушку, то 90% из набранной жидкости фрагмент отдаст в атмосферу уже за первые 3 суток! Но ведь дождь – не ёмкость с водой, да и редко осадки идут сутки подряд. К тому же на время дождя кладку из любого стенового материала накрывают пленкой, чтобы не смыло дождем раствор. Так что, к наступлению холодов, воды в блоках не будет, разумеется, если соблюдать технологию строительства.
Правда №2. Даже если строители напортачили, газобетон намок, а после дождя ударил морозец, сумевшая проникнуть внутрь на глубину 2-3 см влага (глубже возможно только, если блок находится погруженным в воду не менее суток) не повредит материалу. Газоблоки имеют открытые поры, и, расширяясь, вода спокойно находит выход. Все еще сомневающиеся могут поставить в морозилку 2 полные бутылочки с водой – одну открытую, другую нет. Посмотрите, что произойдет, когда вода, как следует, замерзнет.
Правда №3. В жару клеевая смесь быстрее схватывается, не оставляя возможности для выправления огрехов кладки. При температуре +6 +20 вести работу гораздо легче, раствор дольше сохраняет жизнеспособность, а результат – более качественный. Вот только если столбик термометра опускается до -10… +5°С, придется добавлять в клей противоморозную добавку. Ну или сразу купить зимний клей для газобетона, что в итоге обойдется дешевле.
Правда №4. По причине снижения спроса, газобетон осенью дешевеет, транспорт для него найти проще, строителей – тоже, да и за услуги каменщики запросят меньше. Сплошная экономия! Единственная тонкость – будет лучше всего, если выбранные исполнители уже имеют опыт кладки в холодное время года.
Правда №5. Зимой кладка проходит усадку быстрее. А это значит, что весной Вы сможете сразу приступить к отделке дома и благоустройству участка, не теряя времени. Сэкономите, как минимум, одну зиму!
И еще одна тонкость. Если все-таки не удалось закончить возведение коробки и кровельной системы целиком и пришлось прервать работы, необходимо произвести консервацию незаконченного объекта по всем правилам.
Узнайте актуальную стоимость газобетона в нашем интернет-магазине>>
На какой раствор кладут газосиликатные блоки
Автор Евгения На чтение 26 мин. Опубликовано
На какой раствор кладут газосиликатные блоки
bik ton
Строительство дома требует использования материалов, обеспечивающих сцепление блоков между собой. Расход клея для газобетона – решающий показатель при выборе материала. Что же всё-таки выгодней: клей или цементный раствор? Ответим на этот вопрос ниже.
Клей или раствор?
При проведении расчёта сметы на строительство дома из газоблоков первоначально может показаться, что использование строительного раствора, а не специальных клеевых составов, может значительно удешевить строительство. Такой расчёт основывается на примитивном умножении количества блоков и стоимости единицы раствора, но не учитывает тот факт, что расход раствора на 30-70% выше, чем клеевого состава. Толщина слоя строительного раствора при кладке газобетонных блоков составляет 0,8-2 см, тогда как клея – 0,3-0,5 см. Если посчитать реальный расход раствора, то получиться, что его использование в реальности удорожает строительство на 5-10%!
Также стоит учесть, что газобетон обладает отличными теплосохраняющими свойствами и способен аккумулировать тепло. Дом, возведённый из таких блоков, часто не нуждается в дополнительном утеплении, но только при условии, что материал, при помощи которого осуществлялась кладка блоков, также будет обладать теплоизоляционными свойствами. Слой цементного раствора более 5 мм превращается в “холодовый мостик”, через который уходит тепло из дома. А ведь обычно слой раствора гораздо толще! Именно поэтому, дом, построенный из газоблоков с использованием цементного раствора, приходится дополнительно утеплять.
Преимущества применения клея для газобетона в сравнении с цементным раствором:
- меньше толщина слоя в 2-3 раза, что гарантирует отсутствие “холодовый мостик”;
- клей удобен в использовании, не нуждается в специальных смесительных ёмкостях и инструментах;
- не нужно думать о соблюдении пропорций, каждая партия клея будет обладать всеми свойствами, что и предыдущая;
- быстро схватывается, имеет высокие показатели сцепления с поверхностью блоков;
- стойкость к повышенной влажности, температурным перепадам и климатическим воздействиям;
- трудозатраты при использовании клея на 50% меньше, чем при использовании раствора, что удешевляет строительство и экономит время.
Как видите, использование клеевого состава для газобетона не только экономически обосновано при строительстве, но и в будущем оказывает влияние на теплоизоляционные свойства дома, а значит комфорт жильцов.
Клей для газоблоков: состав, характеристики, способ применения
В состав любого клеевого состава для газоблоков входит: портландцемент высокой марки, мытый песок мелкой фракции, модифицирующие и специальные полимерные добавки. Включение в состав различных добавок позволили добиться максимальных теплоизоляционных свойств материала, а также увеличить влагостойкость и ускорить время схватывания.
Применять клей для газобетона, характеристики которого соответствуют оптимальным очень просто – достаточно развести состав согласно инструкции производителя и при помощи шпателя нанести на увлажнённую поверхность, сверху прижимается газоблок, при необходимости выравнивается.
Важно! При наличии атмосферных осадков или температуре воздуха свыше +25°С свежую кладку необходимо укрыть. Для этого можно применить брезент или плотный полиэтилен. Укрытие необходимо, чтобы оградить кладку от преждевременного высыхания, которое впоследствии может стать причиной появления трещин.
Считаем расход клея для газобетона
Стандартный расход клея для газобетона на 1 м2 составляет 1,3-1,7 кг сухого вещества при толщине клеевого слоя 1 мм. Эта информация есть на упаковки от любого производителя, однако такие расчёты были проведены в условиях близким к идеальным, а в реальности стоит расход составляет на 20-30% выше, указанного производителем.
На практике выходит, что расход клея для газобетона на 1 м3 равняется 25 кг сухого клея (25 кг = 1 мешок). При расчёте сметы рекомендуется увеличить общее количество клея ещё на 10-15% на различные потери и неровности газобетона.
Важно! Перед началом работ рекомендуется провести пробное склеивание для определения оптимальной толщины клеевого слоя.
Есть ли способы уменьшить расход клея без потери качества кладки? Не разводите клея больше чем на 4 часа работы, иначе он утратит свои сцепляющие свойства и потребуется наносить более толстый слой. В процессе работы периодически перемешивайте клеевой состав, чтобы избежать расслоения и неоднородности. Разводите сухой состав водой, имеющую оптимальную температуру (указана на упаковке). После разведения дайте клея настояться 15 минут.Клей для газобетона: зимний
При проведении строительных работ при отрицательных температурах использовать обычный клей невозможно, но при этом необязательно прекращать строительство и ждать тепла, а можно использовать морозостойкий клей.
Стоимость зимнего клея будет немного дороже за счёт добавления добавок, которые не позволят составу замерзать при отрицательных температурах. Кладка, выполненная с использованием зимнего материала, по качеству и толщине шва не будет отличаться от обычной. Однако использование морозостойкого клея имеет свои особенности:
- использовать разведённый состав необходимо не позже 30 минут;
- корректировку блоков можно проводить в течении 3 минут;
- газоблоки не должны иметь наледь и следы снега;
- не использовать блоки с трещинами, сколами или неровной поверхностью;
- хранение и разведение сухого клея должно проводиться при температуре не менее +10°С, если иное не указано производителем;
- готовую кладку обязательно укрывают брезентом до полного схватывания клея.
Морозостойкий клей для газобетона имеет более тёмный оттенок в сравнении с обычным, за счёт добавления пластификаторов и специальных добавок.
Расчёт нужного количества морозостойкого клея производится точно так же, как и обычного. Применение зимнего клея при температуре ниже -10°С не допустимо!
Вывод: какой бы клей для газобетонных блоков вы не использовали, вы всегда останетесь довольны получившимся результатом. Клеевой состав демонстрирует отличные теплоизоляционные, морозостойкие свойства, высокую адгезию и удобство применения. Клей является универсальным, его остатки можно использовать для кладки керамической плитки, пеноблоков и кирпичей.
Кладка газобетона: выбор клеящего состава и расчет количества, технология и пошаговая инструкция
Технические характеристики газобетонных блоков (хорошие теплоизоляционные свойства, приемлемая цена, небольшой вес и большой в сравнении с традиционным кирпичом размер) делают этот строительный материал привлекательным для частных застройщиков. Но кладка газобетона имеет свои особенности, которые обязательно нужно тщательно изучить при подготовке к строительству.
Выбор инструментов
Для строительства сооружения из газоблоков понадобятся материалы:
- рулетка;
- строительный уровень;
- строительный миксер или дрель со специальными насадками;
- резиновый молоток;
- ручной штроборез;
- зубчатая кельма;
- уголок;
- ручная пила;
- электрофреза;
- терка;
- емкость для замешивания раствора.
До начала строительства нужно приобрести достаточное количество газоблоков и сухой клеевой смеси или материалов для приготовления цементно-песчаного раствора. И газоблоки, и материалы для кладки лучше брать с небольшим запасом (10-15% сверх расчетного количества). Обязательно в процессе строительства понадобится арматура и рулонный гидроизоляционный материал, поэтому их тоже нужно приобрести заблаговременно.
Приготовление раствора
Класть газобетонные блоки можно как на цементно-песочную смесь, так и на специальный клеевой раствор. Вне зависимости от вида кладочной смеси она не должна растекаться, иначе блоки в кладке не будут надежно зафиксированы. Для укладки на цоколь первого ряда газоблоков используют только цемент.
Клеевой раствор
Клеевые смеси продаются в магазинах в сухом виде. Готовят из них клеевой раствор небольшими порциями непосредственно во время кладки. Неиспользованный раствор быстро засыхает, твердеет и становится непригодным для работы. Размягчать его, добавляя новые порции воды или сухой клеевой смеси, нельзя.
Чтобы приготовить клеевой раствор, в емкость сначала наливают воду из расчета 1 л на 5 кг сухой смеси. Затем, постоянно помешивая, тоненькой струйкой всыпают в воду сухую клеевую смесь. Засыпав и тщательно все взбив, раствору дают 10 минут настояться, а затем повторно тщательно перемешивают. Правильно приготовленный раствор должен быть однородной текстуры с консистенцией густой сметаны.
Цементно песочная смесь
Для приготовления цементно-песчаного раствора смешивают цемент, песок и воду, соблюдая необходимые для получения раствора нужной марки пропорции компонентов. При необходимости в традиционный состав смеси могут вводиться различные добавки.
Что выбрать
Оба варианта имеют свои преимущества и недостатки. Кладочные смеси легко приготовить своими руками. Сухие клеевые смеси стоят сравнительно дорого, поэтому цементно-песчаный раствор считается более бюджетным вариантом.
Оба варианта обеспечивают надежную фиксацию уложенных в кладку газоблоков. Использование цементно-песчаной смеси дает возможность в течение 30-40 минут после укладки подправить выявленные мелкие погрешности кладки. На клей газоблоки класть нужно сразу — клеевой раствор быстро твердеет, и через 15-20 минут что-то изменить в кладке уже невозможно.
Толщина швов при использовании цементно-песочной смеси будет около 9 мм, а при использовании клеевого раствора шов получается не больше 3 мм. Это означает, что раствора понадобится в 3 раза меньше, чем смеси. Из-за этого почти нивелируется разница в ценах — клеевая смесь обойдется застройщику немногим дороже, чем приготовление цементно-песчаного раствора.
Газобетон по теплоизоляционным характеристикам превосходит как клеевую смесь, так и цементную. Благодаря меньшей толщине шва уложенные на клей стены из газобетона лучше удерживают тепло внутри помещения.
Поэтому многие застройщики предпочитают использовать для укладки клеевой раствор или же в целях экономии комбинируют оба варианта: фасады зданий укладывают на клей, а монтаж внутренних стен выполняется на цементно-песчаном растворе.
Технология укладки
Перед началом работы нужно провести небольшую подготовку: внимательно изучить инструкцию по укладке газоблоков, распаковать блоки и перенести их максимально близко к месту кладки.
Это важно при посадке на клей: он быстро отвердевает, и кладку нужно вести максимально быстро.
Также необходимо тщательно выставить по всему периметру выгоняемых стен специальные сигнальные маячки. По этим маячкам натягивается специальный шнур или провод, служащий во время проведения кладки нивелиром, с помощью которого контролируется правильность кладки.
По углам строящегося здания и в местах примыкания перегородок устанавливаются специальные разметочные горизонтальные рейки с нанесенной разметкой высоты будущих рядов, на которые и крепится провод-нивелир. При необходимости такие рейки устанавливают и в других местах кладки, добиваясь, чтобы провод был натянут ровно и нигде не провисал.
Обязательно до начала кладки проводят гидроизоляцию фундамента.
Замешивание смеси
Клеевый раствор готовят небольшими порциями, на 15-20 минут кладки. Замешивают в специальной емкости (можно использовать ведро), наливая в нее теплую воду и засыпая сухую смесь. Для взбивания используют строительный миксер или электродрель со специальной насадкой. Вымешивать нужно, пока клеевая масса не приобретет однородную консистенцию.
Разметка
Перед началом кладки выполняется разметка. Выполнять ее нужно по всем осям поверхности строящегося здания. Блоки предварительно выкладываются в линию. При необходимости проводят подгонку блоков при помощи ручной пилы, добиваясь максимально ровной горизонтали. Для этого в местах, где на цоколе фундамента есть выступающие дефекты, блоки подпиливают снизу.
Укладка и армирование
1 ряд газоблоков укладывают на цементно-песчаный раствор, чтобы за счет большей толщины укладочного шва выровнять цоколь фундамента. Также использование цементно-песчаной смеси для укладки 1 ряда за счет большей продолжительности ее отвердевания позволяет тщательно выставить блоки в горизонтальную линию, чтобы на ней монтировать остальные ряды выгоняемой кладки.
2 ряд начинают класть не раньше чем через 2-3 часа. 2 и последующие ряды лучше укладывать на клей. Укладывают блоки с обязательной перевязкой, для чего каждый блок в верхнем ряду сдвигают на половину длины по отношению к уложенным в нижнем ряду.
Прежде чем выполнить перевязку, в блоках предварительно проделывают штробы для укладки в них в последующем арматуры. Штробы делаются на глубину, достаточную для полного заглубления в них используемой арматуры. Уложенные арматурные прутья заливаются клеем.
Первый слой арматурного пояса обустраивают между цоколем и 1 рядом кладки, затем арматурные слои регулярно повторяют через каждые 3-4 ряда кладки. Обязательно обустройство сплошного арматурного пояса в верхнем ряду кладки, на который будет опираться кровля.
Проверка правильности кладки
Во время выполнения кладки регулярно нужно контролировать ровность укладываемых рядов и толщину скрепляющего клеевого слоя. Для контрольных измерений используют линейку, правило и строительный уровень.
Чтобы проверить вертикальную плоскость, правило прислоняют к возведенному участку стены. При правильно выполненной кладке оно должно плотно примыкать к стене. Строительный уровень устанавливают сверху на уложенные блоки и по его показаниям определяют горизонтальную линию.
При обнаружении отклонений уложенных блоков от вертикальной или горизонтальной плоскости участок кладки нужно переделать. Если отклонения не выявлены, то можно продолжать кладку дальше.
Отделка
Правильная отделка возведенных стен является важной частью надежности и долговечности построенного здания. Газобетон является пористым материалом и способен впитывать много влаги. Правильно выполненная отделка позволяет устранить этот недостаток.
Для отделки можно использовать любые способы, препятствующие впитыванию газоблоками влаги: штукатурку, шпатлевку, облицовку плиткой, кирпичом, обшивку вагонкой, сайдингом и др.
Расчет состава раствора для кладочных работ
Расход клеевого состава составляет около 25 кг на 1 м³ газобетонных блоков. Эти показатели выдерживаются при условии, что используемые блоки будут стандартного размера: 600Х375Х250 мм, а толщина клеевого слоя не будет превышать 3 мм.
Несмотря на некоторые нюансы при возведении построек из газобетонных блоков, их кладка мало отличается от традиционной. При надлежащем старании и терпении кладку по силам выполнить даже начинающим мастерам.
Все о строительстве и инструментах
Правильная кладка газосиликатных блоков на клей
Правильная кладка газосиликатных блоков на клей
Укладка первого слоя блоков на раствор
Ведение кладки на клею имеет много достоинств. В первую очередь использование клея дешевле, чем использование цементно-песчаного раствора. Его цена выше всего в 2—2,5 раза, тогда как расход меньше в 6 раз. Во-вторых, использование мелкозернистого клея исключает образование мостиков холода. В-третьих, толстый слой раствора увеличивает шансы сделать кладку неровной. В-четвертых, кладка блоков на тонкослойном клеевом растворе прочнее кладки с толстыми швами. И прочность при сжатии, и прочность при изгибе у такой кладки будут выше за счет когезионного характера сцепления между пенобетоном и клеем. И, наконец, использование клея вместо раствора снижает общий вес стены.
Распределение клея по поверхности блока
Для получения пенобетона используется менее энергоемкая безавтоклавная технология, позволяющая изготавливать его как в стационарных условиях производственного цеха, так и непосредственно на стройплощадке. В результате вода из бетона испаряется естественным образом, а точность геометрических размеров блоков может иметь значительные отклонения, что усложняет кладку. В этом случае клей применить не удастся и весь монтаж придется вести на растворе, который будет нивелировать несовпадения размеров. Зато для изготовления монолитных стен этот материал подходит отлично: полость в опалубке заполняется тут же приготовленным пенобетоном из шланга.
Масса одного блока при кладке без применения средств малой механизации не должна быть более 45 кг. При работе с ячеистым бетоном требуется осторожность и аккуратность. Запрещается производить погрузку блоков навалом и разгрузку их сбрасыванием. Поддоны с блоками необходимо устанавливать на выровненное основание, защищенное от почвенной влаги. Высота складирования не более 2 ярусов. При длительном хранении незащищенный ячеистый бетон нужно укрывать от дождя или снега изоляционными материалами (брезентом, толем, полиэтиленовой пленкой). Клей для кладки должен храниться в защищенном от влаги состоянии при температуре не ниже 5 °С. При проектировании и возведении зданий из блоков следует выполнять требования, предъявляемые к каменным конструкциям СНиП 3.03.01.
Перед укладкой блоки нужно очистить от пыли, грязи (зимой — от снега и наледи), а битые или с отколотыми кромками и углами отложить (потом их можно использовать для изготовления доборных элементов). Укладке первого ряда блоков следует уделять максимум внимания. Задав первым рядом кладки ровную горизонтальную поверхность, вы максимально облегчите укладку последующих рядов. Между фундаментом или цоколем и кладкой необходима отсечная горизонтальная гидроизоляция, предотвращающая капиллярный подсос.
Гидроизоляция первого слоя кладки
В качестве гидроизоляции могут использоваться рулонные битумные материалы. В случае если поверхность фундамента не идеальна, первый ряд блоков следует укладывать на выравнивающий слой цементно-песчаного раствора толщиной не более 20 мм. В дальнейшем при кладке на цементно-песчаном растворе толщина горизонтальных швов принимается 10—15, в среднем 12 мм в пределах высоты этажа. Толщина вертикальных швов (если нет паза и гребня) принимается 8—15, в среднем 10 мм.
Блок опускают на клей (раствор) сверху, избегая горизонтальной подвижки более 5 мм. Швы должны быть тщательно заполнены клеем.
Выдавившийся клей (раствор) снимают скребком сразу же, не допуская его схватывания. Рихтуют блоки покачиванием или подбивкой резиновым молотком.
Первым закладывается блок в самом высоком углу дома, затем по нивелиру устанавливаются остальные. Следует строго следить за правильностью высоты рядов с самого начала ведения кладки с помощью натянутого шнура-причалки и горизонтального и вертикального уровней или лазерных координаторов. Когда целый блок не входит, нужно изготовить доборный блок, который промазывается клеем с двух сторон и устанавливается на оставшееся для него место. При необходимости выравнивание установленного блока производится пристукиванием киянкой. Неровности кладки нужно устранить при помощи шлифовальной доски или рубанка для гипсокартона.
Если предполагается последующее шпаклевание или оштукатуривание пено- и газобетонной кладки с двух сторон, а кладка ведется с продольным армированием, то заполнение клеем вертикальных швов не требуется. Однако если хотя бы одна из поверхностей стены не будет выравниваться мокрым способом, то проклеивать вертикальные швы необходимо. При этом клей наносится не на центральную пазогребневую зону блока, а двумя полосками шириной около 50 мм с внешней и с внутренней сторон.
При кладке необходимо соблюдать правила перевязки. Вертикальные швы следующих рядов кладки выполняются со смещением не менее 0,4 высоты блока. При кладке стен в два блока перевязка вертикальных швов может быть тычковой или плашковой. Тычковые ряды следует располагать через один ложковый ряд. Опорный и верхний ряды кладки в два блока по толщине всегда следует выполнять тычковыми. Глубина плашковой перевязки должна составлять не менее 100 мм. Сопряжения стен разных направлений следует устраивать с глубиной перевязки не менее 1/3 длины блока. Внутренние стены и перегородки возводят по тем же правилам, что и наружные стены. Сопряжение наружных и внутренних стен выполняют перевязкой блоков в каждом втором слое. При двухслойной конструкции наружной стены блоки каждого второго слоя внутренней стены входят в наружную стену на всю толщину слоя. Для сопряжения с однослойной наружной стеной можно вырезать кусок ее блока на глубину 150—200 мм и на соответствующую длину подогнать блок внутренней стены. При этом вертикальный шов сопряжения обязательно заполняется раствором. Примыкание перегородок к стенам устраивают с применением гибких связей из стальных полос, заранее закрепляемых в соответствующих местах в швах стен.
Места, армирование которых наиболее целесообразно, первый ряд кладки, затем каждый четвертый ряд, опорные зоны перемычек и зоны под оконными проемами. Практически всегда следует устраивать армированный кольцевой пояс в уровне каждого перекрытия и под стропильной системой, а также во всех случаях по высоте кладки при расстоянии в свету между перекрытиями более 3,0 м.Для укладки прутковой арматуры в поверхности кладки следует прорезать штрабы сечением не менее 40 х 40 мм. Это можно сделать, например, с помощью угловой шлифмашинки (болгарки) или штрабореза. Для исключения откалывания бетона штрабы рекомендуется устраивать на расстоянии не менее 60 мм от боковых граней блоков. На углах стены штрабы следует соединять не ломаной линией, а плавным закруглением, пригодным для укладки в него загнутого прутка арматуры. Из нарезанных штраб тщательно удалите пыль, чтобы раствор имел лучшее сцепление с пеноблоками. Для укладки в штрабы лучше всего использовать арматуру периодического профиля 08 мм.
Армирование пенобетонной кладки
Перед укладкой арматуры смочите штрабы водой и наполовину заполните клеем для пенобетона или цементно-песчаным раствором. Уложите арматуру и полностью заполните паз раствором. Излишки клея (раствора) удалите.
Проемы в стенах перекрывают брусковыми перемычками из армированного ячеистого бетона марки D700 и класса прочности В3,5; их укладывают на обычный или клеевой раствор. Рекомендуемая длина опорных поверхностей составляет 300 мм, минимальная — 200 мм. Блоки опорной поверхности и предшествующего ей ряда необходимо склеить цельным швом (не оставляя воздушной прослойки). Длина цельного шва должна составлять не менее 600 мм. При отсутствии или невозможности изготовления брусковых изделий требуемой длины или несущей способности применяют сборные перемычки. Над дверными проемами шириной до 1 м с внешней и внутренней стороны стены устанавливаются металлические уголки с полкой 50—60 мм. Опираться на стену уголок должен не менее чем на 30 см. Над оконными проемами до 2 м используют уголки с полкой 80—100 мм. Для того чтобы блок установить заподлицо, в месте контакта уголка с пенобетоном ножовкой выбирают паз под уголок, устанавливая последний на клей для пенобетона.
Армирование U блока
В этом случае U-блок выполняет роль опалубки, а перемычку образует залитый в эту опалубку бетон. При монтаже устанавливают временную опалубку, которую снимают после полного затвердевания бетона. Перемычки следует проектировать как можно более жесткими (прогиб не должен превышать 1/400 пролета) для предотвращения деформации кладки на опорной поверхности. Несущая способность типовых перемычек составляет 15 кН/м, 20 кН/м и 30 кН/м.
Кладка первого ряда газобетона на фундамент: важный этап возведения стен
Грамотная кладка первого ряда газобетона оказывает сильное влияние на параметры точности геометрии всего возводимого здания. Важно понимать, что этот ряд должен быть идеально ровным.
Стартовому ряду уделяют больше всего внимания. Работы производят тщательно. От ровности и горизонтальности уложенных первых блоков зависит удобство кладки стен дома и качество всего готового сооружения.
Монтаж первого ряда у бригады каменщиков может занять целый день. И это считается нормальным. Здесь формируется базис будущего здания. От точности его заложения зависит простота последующей кладки стен.
Подготовка фундамента
Особенностью газобетонов является не только максимальная лёгкость, но и высокие показатели гигроскопичности. Любое ощутимое повышение уровня влажности провоцирует потерю строительным материалом теплоизолирующих свойств, поэтому дома из газобетонов в обязательном порядке возводятся на цоколе, как правило из бетона или кирпича.
Высота цоколя для дома из газобетона определяется исходя из глубины залегания грунтовых вод, среднего количества и характера выпадаемых осадков. Она должна быть выше среднего уровня снежного покрова для данной местности.
Так для Московского региона средняя высота снега достигает максимума в феврале и в среднем составляет 25-35 см на открытых участках и 40-45 см — на защищенных. Защитой могут выступать заборы, соседние сооружения и растительность. Исходя из этого 40 см цоколя будет достаточно.
Ещё на высоту цоколя влияет эстетический внешний вид здания, количество и высота ступеней, исполнение продухов. А также наличие или отсутствие подвальных и полуподвальных помещений, расположение коммуникаций в подполье.
Гарантией качественной кладки будет применение отсечной гидроизоляции, что станет дополнением стандартной гидроизоляции фундаментного основания.
На что класть первый ряд?
Если перепад основания больше 5 мм, что встречается довольно часто, то обычный клей для газоблоков не подойдёт. Здесь понадобится совместить кладку начального ряда с выравниванием поверхности для последующей кладки блоков.
В этом случае монтаж стартового ряда должен осуществляться исключительно на правильно приготовленные, качественные цементно-песчаные кладочные растворы. Поскольку основание цоколя не идеально ровное, с допуском незначительных перепадов и шероховатостей, использование дорогостоящего клея будет являться недопустимой роскошью для кладки на фундамент. К тому же клей является более пластичным, он предназначен для тонкошовной кладки.
Правильно приготовленный раствор позволит не только получить максимально надежное соединение газобетона с основанием, но и помогает исправить все имеющиеся неровности. Допускается также использование уже готовых, заводских смесей, изготовленных на основе цемента и песка, дополненных гидрофобными, водоудерживающими добавками и пластификаторами.
Приготовление раствора
Цементно-песчаный раствор должен иметь максимально однородную консистенцию, поэтому для его приготовления целесообразно применять бетономешалку, в которую нужно залить ведро воды, засыпать ведро цемента М500 и добавить три ведра просеянного песка.
Ручной замес раствора также допустим.
В процессе замешивания требуется небольшими порциями добавлять воду, что позволит довести смесь до необходимой консистенции. В раствор рекомендуется добавить водоудерживающую добавку для предотвращения быстрого впитывания влаги в газобетон.
Пошаговая технология кладки
Если внутренняя несущая стена по проекту также выполняется из блоков, её монтаж осуществляется одновременно с наружными стенами. При этом выполняется перевязка блоков в кладке. Не забудьте также оставить проёмы под входную и межкомнатные двери в газобетонных стенах, об установке которых можно узнать в этой статье https://izbloka.com/dom/steny/bloki/gazobeton/dveri-g.html.
На первом этапе нужно проверить высоты и горизонтальность фундамента. Перепады до 5 см допускаются, так как при такой толщине раствор не даёт усадку.
Остальные случаи считаются браком и требуют ремонта. Любые не слишком выраженные неровности требуется срезать или заполнить цементной смесью. Очень значительные неровности потребуют установки дополнительной опалубки с последующей заливкой поверхности бетонной смесью с пластификаторами, и дальнейшим выравниванием по уровню. Высота выравнивающего слоя должна составлять порядка 30-50 мм. Кладку можно осуществлять после просыхания слоя.
На следующем этапе выполняется укладка отсечной гидроизоляции. Поверхность прикрывается рулонной гидроизоляцией с нахлёстом материала на стыках.
Выполнен гидроизоляционный слой, по углам ровно выставлены блоки по уровню или нивелиру, натянута шнурка в горизонтальном положении.Кладка начинается с углов, а ориентиром служит наивысшая точка фундамента. Именно в этой точке устанавливается первый блок. Затем расставляются блоки по другим углам. Монтаж угловых блоков с паз-гребневым соединением осуществляется гребнями наружу.
Правильность установки угловых газобетонных блоков можно проконтролировать строительным уровнем или оптическим нивелиром. При необходимости подгонка угловых блочных элементов выполняется специальным резиновым молотком.
Установите угловые блоки на раствор, сверяясь с величиной толщины раствора, написанной на каждом блоке. Устанавливайте блоки точно по уровню. С помощью оптического нивелира проверяйте высоту угла блока. При несовпадении осадите блок с помощью киянки, либо добавьте раствора.
Далее вдоль шнура, ориентируясь на маячные блоки, монтируется блочная кладка с проверкой по горизонтали и вертикали.
После того, как будет проведена кладка первых блоков, и цементный раствор полностью схватится, очень важно провести армирование. Об армировании газобетона и её необходимости читайте в этой статье: https://izbloka.com/dom/steny/bloki/gazobeton/armirovanie-gazosilicata.html.
Перед дальнейшим монтажом нужно дождаться полного затвердевания раствора, что предотвратит риск деформирования стартовых блоков весом последующих рядов.
Полезное видео
В этом коротком сюжете показаны основные моменты, на которые следует обратить внимание при укладке первого ряда.
Как класть газосиликатные блоки
Подумывая над строительством дома своими усилиями, люди стараются выбрать строительный материал, с которым легко работать. На современном строительном рынке можно увидеть большой выбор новых материалов, пригодных для возведения здания. Среди пользующихся популярностью у потребителей строительных материалов одно из первых мест занимают газосиликатные блоки. Чтобы дом получился крепким, надежным, необходимо знать, как класть газосиликатные блоки правильно, какой раствор использовать и как рассчитать необходимое количество материала на ваш проект.
Технология строительства из газосиликата
Построить самостоятельно дом из блоков газосиликата можно даже в том случае, если у вас есть только начальные знания о строительных технологиях, но присутствуют трудолюбие и энтузиазм. Для возведения стен понадобятся следующие инструменты и материалы:
- Для разбавления клея нужна емкость, мутовка-перфоратор.
- Наносить клей можно специальным ковшом или зубчатым шпателем.
- Распилить блок на куски нужных размеров поможет ножовка с большим зубом.
- Неровности можно выровнять крупным наждаком.
- Щетка-сметка.
- Металлический угольник, уровень.
- Раствор из песка и цемента.
- Газосиликатные блоки марки Д400 или Д500.
- Минераловатный паронепроницаемый утеплитель.
- Кладочная стекловолоконная сетка или арматурные стержни.
Расчет необходимого количества блоков
Можно сделать расчет общего количества газосиликатных блоков, рассчитав объем всех стен дома по проекту.
Более точный расчет проводят для каждой стены отдельно. Для этого нужно взять размеры стены из проекта, а размеры газосиликатного блока станут известны при его закупке. Зная ширину блока и длину стены модно сделать расчет количества блоков на один ряд кладки. Если нужна половина блока, она учитывается как целый блок. Точно так же проводят расчет количества рядов кладки. Количество рядов умножают на полученное число блоков в одном ряду. Итоговое число — количество блоков на одну стену.
Если в стене есть проемы дверей и окон, также делают приблизительный расчет. Затем, посчитав блоки для каждой стены, суммируют все цифры.
Выполнение кладки
Обратите внимание! От точности и качества кладки первого ряда зависит прочность и надежность всей конструкции здания.
Готовый фундамент необходимо покрыть гидроизоляционным слоем, сверху кладочной сеткой, а для кладки стартового ряда строительства использовать обычный раствор. Затем нужно проверить углы здания на разницу в высоте, она должна быть не выше 30 мм. Если углы не расположены на одном уровне, кладку необходимо начинать с самого высокого угла.
Первый ряд призван выровнять погрешности заливки фундамента, поэтому толщина раствора в разных местах может отличаться, но не должна быть меньше 20 мм. Следом устанавливаются угловые блоки и соединяются между собой шнуром. Проверяется уровень натянутого шнура, он должен быть строго горизонтальным. При длине стен больше 10 метров необходимо уложить промежуточные блоки, чтобы не допустить провисание шнура.
Для корректировки вертикального и горизонтального расположения блоков используют резиновый молоток. Неровности кладки убирают наждаком. Для устранения пыли и загрязнений применяют щетку-сметку. Если нужна часть блока, то делают распил электропилой или ручной ножовкой.
Дальше кладку блоков выполняют при помощи клеевого раствора. На строительную площадку поставляют сухую смесь из песка мелкой фракции, портландцемента и специальных добавок. Необходимо внимательно прочитать инструкцию по приготовлению качественного раствора требуемой консистенции. Толщина связующего слоя должна быть не больше 3 мм.
Обратите внимание! Перед нанесением клея на блоки их нужно тщательно очистить и смочить водой, чтобы обеспечить качественную адгезию.
Кладку стен проводят в теплое время года. Для строительства в холодное время необходимо использовать зимний клей. На блоки клей наносят зубчатым шпателем по ширине равным ширине поверхности газосиликатного блока. Слой должен быть равномерным как на вертикальной, так и на горизонтальной стороне блока. После нанесения клеевого слоя поверхность блока должна быть бороздообразная. Не нужно заполнять раствором промежутки между захватными карманами и между гребнем и пазом.
Второй ряд блоков необходимо укладывать со смещением наполовину, чтобы получилась перевязка между рядами. Кладка всех рядов начинается с углового блока. Положение каждого блока необходимо контролировать уровнем и делать корректировку молотком. Все швы должны быть заполнены клеевым раствором, чтобы избежать появления усадочных трещин. Избыток клея удаляется мастерком.
Если вы используете для самостоятельного строительства блоки формой паз-гребень, вам не нужно будет выполнять вертикальное армирование. Для горизонтального армирования на поверхности газосиликатных блоков уложенного ряда по периметру делают продольные штробы и укладывают в них стекловолоконные стержни или просто кладочную сетку.
Обратите внимание! В верхней части дверных и оконных проемов сначала укладываются металлические уголки длиной, превышающей ширину проема минимум на 40 см, а затем продолжают кладку блоков.
Монтаж перекрытий
После того как кладка стен будет практически завершена и останется сделать только последний ряд, необходимо вместо блоков устроить монолитный железобетонный пояс. Такой подход поможет равномерно распределить нагрузку от многопустотных или ячеистобетонных плит на все несущие стены.
Отделка стен из газосиликата
Для наружной отделки используют специальные вентилируемые системы или материалы, характеризующиеся высокими показателями паропроницаемости. Между кладкой из фасадного кирпича и стеной из газосиликата оставляется зазор. Соединяют две кладки гибкими связями. Если вы отдаете предпочтение использованию для фасадных работ краски, шпатлевок или штукатурных смесей, необходимо убедиться, что они предназначены для работ с газосиликатом.
Внутренняя отделка предполагает применение дышащих материалов. Стены из газосиликатных блоков можно оклеить обоями или покрасить водоэмульсионной краской. Для ванной, санузла, кухни необходимо сначала уложить пароизоляцию или пропитать стены специальным раствором. Когда для отделки ванной используется керамическая плитка, пароизоляция не нужна.
Обратите внимание! Шпаклевать внутренние стены можно не раньше чем через два месяца после завершения строительства.
Работы над фасадом здания можно начинать только тогда, когда будут завершены все внутренние отделочные процессы. Единственным исключением являются вентилируемые системы. Их можно устанавливать сразу после окончания строительства.
Видео
Подробнее о монтаже газосиликатных блоков можно узнать ниже:
CE2187_FinalPaper_2015-11-09_18.20.11_ORHDAU
% PDF-1.4 % 2 0 obj > / OCGs [43 0 R] >> / Pages 3 0 R / Type / Catalog / ViewerPreferences 40 0 R >> эндобдж 41 0 объект > / Шрифт >>> / Поля 47 0 R >> эндобдж 42 0 объект > поток application / pdf
AAC в Дейтоне, Огайо — Продукты
«Стандарт на огнестойкие испытания строительных конструкций и материалов»
Характеристики крыши, полов и стен при воздействии огня важны для безопасности людей, находящихся в здании, их имущества и содержимого здания. Этот стандартный метод испытаний определяет допустимые и неограниченные характеристики для крыш и полов, а также несущие и ненесущие характеристики для стен при воздействии стандартного воздействия огня с наложенной нагрузкой, моделируя условия максимальной нагрузки.Стандарт предусматривает относительную меру способности сборки предотвращать распространение огня и сохранять свою структурную целостность. После того, как сборка подвергается стандартному воздействию огня, на нее воздействуют струей воды из стандартного пожарного шланга, предназначенной для стимуляции воздействия усилий пожаротушения. Сборка должна успешно пройти обе части испытания, чтобы достичь определенного уровня огнестойкости.
Были испытаны две сборки панелей Aercon, UL K910 (сборка панели пола толщиной 8 дюймов) и UL P933 (сборка панели крыши толщиной 8 дюймов).Обе сборки достигли рейтинга ограниченной сборки 4 часа (с использованием панелей типа 1) и рейтинга неограниченной сборки 1 час (с использованием панелей типа 1) и 1,5 часа (с использованием панелей типа 2). Два протестированных типа панелей имели разную минимальную степень покрытия армирования; Тип 1 с минимальной крышкой 20 мм и Тип 2 с минимальной крышкой 45 мм. Сдерживание было обеспечено с помощью залитой на месте железобетонной кольцевой балки по периметру испытательной сборки. На основании типов протестированных панелей 10- и 12-дюймовые панели крыши и пола также имеют одинаковые рейтинги ограниченного монтажа и неограниченного монтажа.
Сборка блочных стен Aercon, UL U921, достигла 4-часового рейтинга несущей стенки и 4-часового номинального значения несущей стенки при минимальной толщине 6 дюймов и класс прочности AC6 / 650. Основываясь на тепловых свойствах этого класса прочности, остальные классы прочности также имеют такие же номинальные характеристики несущей стенки и ненесущие стенки, равные 4 часам.
Является ли газобетон огнестойким? — BuilderSpace
Воздухобетон пожаробезопасен?
Для многих строителей, работающих сегодня в строительной отрасли, воздухобетон (автоклавный газобетон) — это путь в будущее, но могут возникнуть вопросы по качеству и долговечности.Многие домовладельцы спрашивают, является ли газобетон огнестойким, чтобы минимизировать возможные будущие риски.
Aircrete является огнестойким, потому что он сделан из огнестойких материалов, включая цементную смесь, пену и воду. Независимо от того, как много тепла подвергается воздухобетон, он не загорится. Если вам нужен качественный огнестойкий строительный материал, то аэробетон — отличный выбор.
Конструкция и дизайн этого продукта делают его лучшим выбором по многим причинам. Aircrete может принести пользу множеству строительных проектов, от небольших домашних проектов до крупномасштабных многоэтажек.Чтобы узнать, чем именно и почему полезен газобетон, продолжайте читать.
Что такое газобетон и как он используется?
Aircrete — это результат объединения нескольких элементов, включая кальциевый гипс, кварцевый песок, алюминиевый порошок, известь, цемент и воду. После объединения смесь выдерживается в автоклаве для образования блоков. Эти блоки устойчивы к возгоранию и плесени, а также обеспечивают превосходную изоляцию.
В этом коротком видео показано, как эти блоки и панели производились и использовались во всем мире в течение многих лет:
Химический процесс, происходящий при нахождении воздушно-бетонной смеси в автоклаве, придает ей важные свойства, такие как огнестойкость или водонепроницаемость.Водородные газы образуются в результате реакции алюминиевого порошка с гидроксидом кальция. Как только пузырьки газа выходят, воздух заменяется и поддерживает мелкие пузырьки воздуха, которые можно увидеть в аэрбетоне.
Aircrete — не новый строительный материал. Фактически, он использовался в строительстве более 70 лет. Одно из главных достоинств этого продукта — низкий уровень воздействия на окружающую среду. Благодаря своей универсальности, это популярный выбор в различных строительных ситуациях, в том числе:
- Внутреннее и внешнее размещение
- Здания, подверженные резким перепадам температур
- Высотные дома
- Внутренняя сборка стены полости
- Конструкция из массивных стен
- Торговые центры
- Аэропорты
- Дома
- Коммерческие здания
- Изоляция
- Защитный барьер для стальных рам
Этот универсальный материал подходит для любой работы, независимо от ее размера.От крупномасштабных высоток до небольших домашних проектов, таких как садовые ящики, aircrete может обеспечить стабильный продукт с атрибутами, аналогичными традиционному бетону.
Преимущества Aircrete
Использование газобетона при следующем строительстве дает множество преимуществ. От простоты использования до огнестойкости, газобетон является популярным выбором во многих ситуациях для подрядчиков. Он не только сопоставим со стандартным бетонным материалом, но и обеспечивает большую гибкость, что делает его лучшим выбором для многих строительных приложений.
Легкий материал
Благодаря процессу производства изделий из газобетона, его легкая конструкция идеально подходит для многих проектов. Наличие универсальных блоков, которые легко обрабатывать, формировать и сверлить, может значительно сократить общее время на завершение строительства. Экономия времени на рабочем месте не только сэкономит деньги за счет сокращения рабочей силы, но и снизит затраты на доставку материалов.
Крупные блоки готового газобетона помогают рабочим выполнять крупные подрядные работы быстрее и эффективнее.Это преимущество проявляется в уменьшении объема каменных работ и в том, что эти легкие газобетонные блоки проще резать или формовать по мере необходимости, в отличие от традиционных бетонных материалов.
Огнестойкий
Aircrete обладает превосходными способностями не только быть огнестойкими, но также защищать и предотвращать другие участки от повреждений при пожаре. Эта огнезащитная способность обусловлена пористой природой материала, что делает его привлекательным выбором для многих ситуаций. Они классифицируются как негорючие материалы и соответствуют всем строительным нормам и правилам.
Независимо от того, как используется газобетон, в качестве изолятора или межсетевого экрана, преимущества огромны. Случаи возникновения электрических пожаров в домах с использованием традиционных методов изоляции привели к массовым разрушениям. Aircrete может изменить исход многих серьезных ситуаций, в том числе ограничить распространение огня изнутри стен или даже ближайшего здания.
Водонепроницаемость и защита от вредителей
Ущерб, причиненный водой и водой, также является серьезной проблемой для владельцев зданий.Благодаря своей конструкции Aircrete обеспечивает отличную вентиляцию.
Разрешая диффузию воды, аэробетон помогает снизить влажность в здании, поглощая и рассеивая влагу. Этот процесс может значительно снизить вероятность образования плесени или грибка. Состав материала воздухобетона спроектирован так, чтобы не разрушаться, не разлагаться или не гнить в воде.
Когда вы пытаетесь избежать вредителей, воздухобетон может быть эффективным решением. Эти легкие блоки устраняют щели, через которые вредители могут регулярно проникать в здания.От краев пола до дверей и оконных рам воздухобетон легко герметизирует, чтобы предотвратить любые потенциальные проблемы из-за мелких злоумышленников. Они не привлекают вредителей и неуязвимы для грызунов и других вредителей извне.
Прочный и долговечный
Долговечность газобетона делает этот строительный материал лучше по сравнению с традиционным бетоном. Способность выдерживать резкие перепады температур без каких-либо повреждений или изменений исходной конструкции является значительным преимуществом для некоторых климатических условий по всему миру.Его конструкция предназначена для предотвращения разрушения со временем из-за типичных условий окружающей среды.
Aircrete может пережить стихию, что бы ни случилось. Годы применения различными способами доказали, что этот автоклавный газобетон значительно превосходит многие традиционные методы. Здания, подверженные землетрясениям, торнадо и ураганам, выиграют от использования газобетона.
Экономичный
Одним из популярных атрибутов газобетона является звукоизоляционная способность, которую он придает зданиям при правильной установке.При правильной установке между полом и стенами этот автоклавный газобетон помогает снизить шум.
Если здание правильно изолировано, оно будет удерживать тепло и сохранять прохладу по мере необходимости. Aircrete может помочь сократить расходы на отопление и охлаждение зданий, помогая регулировать температуру в помещении. Он нетоксичен и не использует токсины в процессе автоклавирования, которые могут повлиять на окружающую среду в здании.
Aircrete также известен своей экологической безопасностью во многих отношениях.От процесса производства до транспортировки материалов на стройплощадке это помогает снизить воздействие на окружающую среду в целом. В качестве альтернативы, при укладке газобетона использование бесшовной интеграции помогает сократить количество отходов.
Недостатки Aircrete
У этого строительного материала не так много недостатков, но вы должны знать о некоторых потенциальных проблемах.
Во время обработки перед установкой газобетон может быть хрупким, и с ним нужно обращаться с большей осторожностью, чем с традиционным кирпичом, чтобы избежать повреждения блоков.Из-за хрупкости этих блоков из автоклавного газобетона рекомендуется использовать более тонкие и длинные винты для любых креплений, чтобы предотвратить поломку.
Aircrete также не следует укладывать в дождливую погоду, поскольку доказано, что он трескается и получает повреждения. Все блоки должны быть сухими при установке и после нее. Соблюдая рекомендуемые процедуры обращения с газобетоном и его установки, вы можете ограничить возможные неприятные эффекты.
Заключение
Хотя газобетон существует уже много лет, его применение быстро увеличивается.По мере того как все больше подрядчиков осознают многочисленные преимущества этого продукта из автоклавного газобетона, его популярность растет. От изоляции стен, полов и потолков — универсальность аэробетона дает ему преимущество перед традиционными методами.
ОгнестойкостьAircrete, наряду с другими многочисленными атрибутами, обеспечивает зданиям рекомендуемые стандарты, необходимые для правильного строительства. Если вы ищете экономичное решение, которое поможет сократить расходы на отопление или охлаждение, отпугнуть вредителей и обеспечить безопасность вашей семьи, aircrete — ответ для вас.
Источники
ТЕРМИЧЕСКИЕ ХАРАКТЕРИСТИКИ & ПОЖАРНАЯ УСТОЙЧИВОСТЬ АВТОКЛАВИРОВАННОГО ПЕРИОДИЧЕСКОГО БЕТОНА ВНЕЗАПНАЯ ВЛАЖНОСТЬ
Реферат
Автоклавный газобетон (AAC) также производится уже много лет, есть еще некоторые моменты, требующие уточнения. Один из этих моментов, который необходимо знать, — это воздействие влаги на членов AAC в районах с высокими уровнями относительной влажности в средиземноморском климате, которые важны для долговечности и изоляционных свойств AAC.Поэтому некоторые испытания механических и физических свойств бетона ACC проведены. К ним относятся испытания теплоизоляции и огнестойкости при разном уровне влажности блоков ACC. По результатам испытаний; Повышение влажности внутри камеры во время процедуры нагрева в установившемся режиме вызвало увеличение среднего изменения температуры на внешней поверхности стены АКВ. AAC теряет свою массу и механические свойства под воздействием высокой температуры выше 500 градусов по Цельсию.
Ключевые слова: Тепловые характеристики, AAC, испытание на огнестойкость, влажность
1. ВВЕДЕНИЕ
Конструкция здания и свойства материала влияют на тепловые характеристики и потребление энергии в жилых и коммерческих зданиях. Важно помнить, что тепловые характеристики любого строительного материала являются результатом нескольких факторов и не могут считаться эффективными или неэффективными на основании какого-либо одного фактора. Существует множество определений различных термических свойств, которые используются для определения общей термической эффективности любого строительного материала.Автоклавный газобетон (AAC) предлагает особые благоприятные свойства в контексте устойчивого развития в строительной отрасли. Технологии производства AAC энергоэффективны и потребляют небольшое количество сырья по сравнению с производством других строительных материалов, что можно объяснить низкой плотностью и специальной безотходной и экологически чистой производственной формулой AAC. Типичная плотность AAC составляет от 300 до 1000 кг / м3 (ub a drt cibduruib). Газобетон не имеет крупных заполнителей в своей смеси, и можно упомянуть, что пористый легкий бетон — это бетонный раствор, который аэрируется мелкими и мелкими пузырьками в результате химического процесса или с использованием воздухововлекающего агента.Автоклавный газобетон изготавливается из цемента, кварцевого песка, негашеной извести, гипса и алюминиевой пудры.
2. ПРОЦЕДУРА ЭКСПЕРИМЕНТА
Были проведены эксперименты для исследования тепловых характеристик и влияния проникновения влаги, а также испытания на огнестойкость. Равновесное содержание влаги для AAC зависит от насыпной плотности и климатических условий. Обычно влажность колеблется от 3 до 5%, если окружающие условия 23 градуса по Цельсию и относительная влажность 80%.Эта статья включает краткое описание экспериментальной процедуры испытаний, которые проводились в соответствии с TS pr EN и ASTM.
2.1 Испытание на огнестойкость
Испытание на огнестойкость было проведено для выявления воздействия огня на свойства AAC. Испытания проводились на кубах размером 50x50x50 мм при шести различных температурах. Эти температуры были установлены на уровне 100, 300, 500, 700, 900 и 1000, и были на электрической муфельной печи.Для каждой температуры были протестированы три образца AAC.
Блоки AAC были вырезаны на отрезном станке; все блоки сушили при температуре 60 градусов по Цельсию в течение трех дней с использованием электрической печи.
Каждый из трех образцов, отобранных для испытания, необходимо выдержать в печи при желаемой температуре в течение 30 минут. Каждый образец был взвешен до и после испытаний для определения влияния огня на потерю веса блоков AAC.
После испытания на огнестойкость была определена прочность образцов на сжатие, чтобы выявить влияние огня на прочностные свойства блоков AAC, рисунок 1.
2.2 Испытания на тепловые характеристики
Испытания на тепловые характеристики были проведены для оценки теплоизоляционных свойств панелей AAC в трех различных условиях влажности. Для этого испытания была установлена специальная камера из оцинкованных стальных пластин размером 700x850x600 мм. Расстояние между двумя стальными панелями камеры было заполнено легким материалом и гипсовым раствором, чтобы повысить ее изоляцию от любых термических условностей, а также избежать передачи тепла от двери камеры пенополиуретана, введенного внутрь дверной панели.
Испытания тепловых характеристик проводились в трех различных условиях:
1) Три различных режима влажности.
2) Панель AAC протестирована с покрытием и без него. На обе стороны панели нанесено гипсовое покрытие толщиной 10 мм.
3) Стены AAC прошли испытания при трех различных уровнях температуры в установившемся режиме. Образцы выдерживали при указанных температурах в течение 95 минут. Тесты проводились при температурах 40, 60 и 70 градусов и трех различных условиях влажности: 555, 70% и 100%.
Прибор Hot-Box был использован для определения коэффициента теплопроводности стенок АКВ. Процедуры этого испытания были выполнены в соответствии с TS EN ISO 8990.
Hot-Box содержит две хорошо изолированные камеры: холодную камеру и горячую камеру, которые кондиционировались нагревательным и охлаждающим оборудованием для достижения желаемых температур с каждой стороны стены. И холодная, и горячая камеры циклически менялись между разными температурами. Эти температурные циклы были запрограммированы для имитации внешних климатических условий.Температуры определялись термопарами с чувствительностью 0,1 градуса Цельсия. В каждой камере имелось 9 термопар для измерения температуры поверхности образца стенки, а в каждой камере имелось по 3 термопары для измерения температуры камер. Размер стены из AAC, которая использовалась для испытания теплопроводности, составлял 1200x1200x100 мм, рис. 4.
Все данные (температура поверхности и окружающей среды) были переданы на ПК, и был рассчитан коэффициент теплопроводности.
3. РЕЗУЛЬТАТЫ И ОБСУЖДЕНИЕ
Испытания тепловых характеристик проводились при трех различных условиях влажности, чтобы определить влияние влажности на тепловые свойства панелей AAC. Основная цель этого теста заключалась в обнаружении изменений температуры на внешней поверхности стены АКВ при проведении процедуры нагрева внутри камеры. Процедура нагрева проводилась при трех различных температурных режимах; каждый температурный режим поддерживался постоянным в течение 95 минут.
При влажности 55% внутри камеры уровень температуры на внешней поверхности стены AAC без покрытия после 95 минут процедуры нагревания при 40 градусах Цельсия увеличился с 23,2 до 24,9 градусов по Цельсию. После повышения температуры внутри камеры до 60 градусов по Цельсию, в течение 95 минут после процедуры нагрева, температура на внешней поверхности стенки AAC увеличилась с 24,9 до 27,3 градусов по Цельсию. Третьи 95 минут процесса нагрева проводились, когда внутренняя температура составляла 70 градусов по Цельсию, после этого процесса температура на внешней поверхности стены AAC составляла 30.2 градуса по Цельсию, рисунок 5.
После нанесения гипсового покрытия на обе поверхности был проведен процесс обогрева стен AAC при влажности 55%. В конце 95-минутного процесса нагрева при 40 градусах по Цельсию температура внешней поверхности стены AAC увеличилась с 22,7 до 23,2 градусов по Цельсию. Вторые 95 минут процесса нагрева начинались, когда температура внутри камеры поднималась на 60 градусов по Цельсию, температура на внешней поверхности стены AAC увеличивалась с 23,2 до 25 градусов.3 градуса по Цельсию. Температура внутри камеры составляет 70 градусов по Цельсию, что показывает изменение температуры наружной поверхности стенки AAC от 25,3 до 27,1 градусов после полного нагрева в течение 280 минут, рисунок 6.
При влажности 70% внутри камеры температура снаружи поверхность стены AAC при 40 градусах по Цельсию увеличилась с 22,9 до 24 градусов по Цельсию. А когда температура внутри камеры повысилась до 60 градусов по Цельсию в течение 95 минут, внешняя поверхность стены AAC увеличилась с 24 до 27.4 градуса по Цельсию. Третьи 90 минут процесса нагрева проводились, когда внутренняя температура составляла 70 градусов по Цельсию, после этого процесса температура на внешней поверхности стены AAC составляла 31,2 градуса по Цельсию, рисунок 7.
После нанесения гипсового покрытия на обе поверхности стены AAC процесс нагрева на 70% влажностный режим. В конце 95-минутного процесса нагрева при 40 градусах по Цельсию температура внешней поверхности стены AAC увеличилась с 20,5 до 22,1 градусов по Цельсию.
Вторые 95 минут процесса нагрева начинались, когда температура внутри камеры составляла 60 градусов по Цельсию, а после этого процесса температура на поверхности стенки ААК увеличивалась с 22.От 1 до 24,6 градусов по Цельсию. Когда температура внутри камеры достигла 70 градусов по Цельсию, температура на внешней поверхности стены AAC увеличилась с 24,6 до 27 градусов после всего 280 минут процесса нагрева, рис. 8.
При 100% влажности внутри камеры, Уровень температуры на внешней поверхности стены AAC после 95 минут процедуры нагревания при 40 градусах по Цельсию увеличился с 22,7 до 23,1 градусов по Цельсию. После повышения температуры внутри камеры до 60 градусов по Цельсию, в течение 95 минут процедуры нагрева температура на внешней поверхности стенки ААК повысилась с 23.От 1 до 29. Третьи 95 минут процесса нагрева проводились, когда внутренняя температура составляла 70 градусов по Цельсию, а после этого процесса температура на внешней поверхности стены AAC была измерена как 32,3 градуса по Цельсию, рис. 9.
A
после нанесения покрытия из гипса как на внешней, так и на наружной стороне. На внутренних поверхностях стены ААК проводились процессы обогрева в условиях 100% влажности. По окончании 95-минутного процесса нагрева при 40 градусах по Цельсию температура внешней поверхности стены AAC увеличилась с 23.От 5 до 26 градусов по Цельсию.
Второй 95-минутный нагрев внутри камеры составлял 60 градусов по Цельсию, и после этого процесса температура на внешней поверхности стены AAC увеличилась с 26 до 28 градусов. При повышении температуры внутри камеры до 70 градусов по Цельсию, температура на внешней поверхности стены AAC увеличилась с 28 до 30,7 градусов после всего 280 минут процесса нагрева, рисунок 10.
Согласно результатам испытаний после 155-45% повышение влажности во время включения
Влажность и температура внутри домов — два важных фактора, которые могут повлиять на комфорт и здоровье жителей.Сообщается, что температура от 20 до 26 градусов и влажность от 30% до 70% необходимы для создания подходящих условий жизни внутри домов.
Согласно результатам испытаний, после увеличения влажности на 15–45% в течение 280 минут нагрева в устойчивом режиме, температура на внешней поверхности стены AAC увеличилась в среднем на 1,3 градуса по Цельсию до 2,6 градуса для панели без покрытия. После нанесения гипсового покрытия на обе поверхности стены AAC, температура на внешней поверхности стены снизилась, а внешняя поверхность стены уменьшилась в среднем на 2.44 градуса по Цельсию при сравнении с такими же условиями влажности для стены из AAC без покрытия. Это означает, что гипсовое покрытие блокирует открытые поры на поверхности стены из AAC и препятствует проникновению воздуха и влаги внутрь стены, тем самым повышая теплоизоляцию.
3.1 Теплопроводность стен из AAC с помощью устройства Hot-Box
Коэффициент теплопроводности 0,0934 Вт / (мК) был получен по результатам испытаний стеновых систем из AAC, что в 3 раза меньше, чем у стеновых систем из глиняного кирпича.Это указывает на то, что стеновые системы AAC с блоками AAC обеспечивают лучшую теплоизоляцию по сравнению со стеновыми системами из традиционного глиняного кирпича, а также примерно в 3 раза меньшую статическую нагрузку. Снижение статической нагрузки — важная проблема в сейсмических регионах, подверженных землетрясениям.
Удельный вес материала является наиболее важным фактором, влияющим на теплоизоляционные свойства. Более низкий удельный вес материала приводит к меньшему коэффициенту теплопроводности, что означает лучшую теплоизоляцию. Другими словами, более легкие материалы обеспечивают лучшие теплоизоляционные характеристики.Кроме того, теплоизоляционные свойства стеновых систем AAC тесно связаны с количеством пор и их распределением. Мелкие поры обеспечивают лучшую изоляцию.
Результаты экспериментальных исследований также показывают, что существует значительная разница между стеной из AAC и традиционной системой стен из глиняного кирпича, основанная на коэффициенте теплопроводности.
Использование блоков из автоклавного газобетона для отопления и охлаждения жилых зданий позволяет сэкономить до 35-60% энергии по сравнению с другими традиционными каменными материалами.
3.2 Испытание на огнестойкость
Испытание на огнестойкость было проведено для выяснения влияния различных температур горения на свойства образцов AAC. Для этого образцы кубиков диаметром 50 мм были испытаны при шести различных температурах с помощью электрической печи. После испытаний на огнестойкость было проведено испытание на прочность при сжатии, чтобы выявить влияние огня на прочностные свойства образцов AAC.
После 30-минутной процедуры нагревания при температуре 100 градусов Цельсия никаких изменений во внешнем виде блоков AAC не наблюдалось, а также не было обнаружено снижения веса и прочности на сжатие.
После 30-минутной процедуры нагревания при температуре 300 градусов Цельсия никаких изменений во внешнем виде блоков AAC не наблюдалось, но было обнаружено небольшое уменьшение веса блоков. С другой стороны, средняя прочность блоков на сжатие после огневых испытаний снизилась примерно на 22%.
После 30-минутной процедуры нагревания при температуре 500 градусов по Цельсию наблюдалось потемнение цвета блоков ААС, также было обнаружено небольшое уменьшение веса блоков. Среднее снижение прочности блоков на сжатие после огневых испытаний составило примерно 28%.
Процедура нагрева при температуре 700 градусов по Цельсию, изменение цвета блоков ААС на более темный и обнаружено уменьшение веса блоков. Среднее снижение прочности блоков на сжатие после огневых испытаний показывает большее снижение, примерно на 35%.
После 30-минутной процедуры нагрева при температуре менее 900 градусов по Цельсию цвет блоков AAC изменился со светло-серого на серый. Помимо уменьшения веса блоков, на поверхности блоков наблюдались трещины.С другой стороны, средняя прочность блоков на сжатие снизилась до 46% по сравнению с контрольными образцами.
Процедура нагрева при температуре 1000 градусов по Цельсию привела к тому, что цвета блоков AAC стали ярко-белыми и на поверхности образцов образовалось множество трещин. Это явление было связано с разложением химических фаз кремнезема и извести.
Согласно стандарту TS-EN 679 оптимальная влажность для блоков AAC, которые будут испытываться под осевой нагрузкой, составляет 6%. С другой стороны, с повышением температуры внутри печи влажность уменьшалась из-за процесса испарения, что приводило к уменьшению веса блоков, а также к некоторой дегардации в порах.
4. ВЫВОДЫ
Тепловые характеристики были оценены для различных температур и влажности для двух типов стен из AAC с покрытием и без покрытия. По результатам испытаний; Повышение влажности внутри камеры во время процедуры нагрева в установившемся режиме привело к увеличению среднего изменения температуры на внешней поверхности стены АКВ. Испытание на огнестойкость проводилось для определения способности материала AAC противостоять огню при шести различных температурах, возрастающих от 100 до 1000 градусов по Цельсию.Испытания на огнестойкость повлияли на цвет, вес и особенно прочность на сжатие блоков AAC. Цвет образцов начинает становиться темнее от своего первоначального беловатого цвета при повышении температуры до 900 градусов по Цельсию, за исключением образцов, подвергнутых воздействию 1000 градусов по Цельсию, которые показали более яркий белый цвет. Масса и прочность на сжатие всех образцов начали снижаться по сравнению с исходным сухим состоянием; это указывает на то, что AAC теряет свою массу и механические свойства под воздействием повышенной температуры. Следует учитывать, что снижение упомянутых свойств при повышенных температурах допустимо до 500 градусов по Цельсию, что свидетельствует о небольшом снижении свойств AAC.
Автоклавные прямоугольные термостойкие блоки из пенобетона AAC, для перегородок, размер: 8 (H) x 24 (L) дюймов, 75 рупий / штука
О компании
Год основания 2005
Юридический статус Фирмы Физическое лицо — Собственник
Характер бизнеса Оптовый торговец
Количество сотрудников До 10 человек
Годовой оборот2–5 крор
Участник IndiaMART с марта 2010 г.
GST33ADZPV0727F2Z5
Shreesha Building Solution , основанная в 2005 , является одним из ведущих оптовых продавцов с обширным ассортиментом блоков AAC AEROCON. Наш предлагаемый диапазон состоит из Автоклавных газобетонных блоков высшего сорта и Блочного Мастерка AAC. В дополнение к этому, благодаря своему превосходному качеству, легкости, удобству в использовании и идеальному размеру, эти линейки продуктов высоко ценятся среди наших клиентов.Выгодно для инженеров: Так как инженеры должны продумать все возможные укромные уголки и уголки строительных работ, им придется следить за тем, чтобы блоки были прочными и имели отличную отделку. Следующее, что вам было бы полезно знать о блоках, это то, что они не допускают капиллярного действия и, следовательно, обеспечивают водонепроницаемость. По этой причине эти блоки больше всего рекомендуются инженерами строительного бизнеса. Прочность на сжатие определяется как прочность или величина фактора устойчивости, необходимая для преодоления сжатия против любых внешних факторов, когда речь идет о контакте с этими блоками AAC.Эти блоки, следовательно, еще одно преимущество к удовольствию инженера. Блоки сделаны с сильной структурной поддержкой дизайна.
Выгодно для архитекторов: Эти современные архитекторы могут экспериментировать с новыми идеями и стилями, и они могут свободно использовать эти новаторские идеи при использовании блоков AAC. К удовольствию архитекторов, которые хотели бы видеть свои творения в таком же состоянии даже спустя долгое время, эти здания практически не требуют обслуживания, поскольку они требуют обслуживания каждые пятьдесят лет.Это причина, по которой архитекторы выбрали блоки AAC.
Выгодно для подрядчиков: Подрядчик будет искать рентабельные методы строительства и поэтому предпочел бы иметь меньше рабочей силы для работы над своим проектом. При этом блоки сделаны с меньшим количеством стыков, и для них потребуется меньшее количество раствора, и эти блоки можно легко установить. Блоки AAC больше по размеру по сравнению с обычными обожженными кирпичами. Эти блоки сделаны так, что в них можно забивать гвозди без предварительного сверления.
Видео компании
Проблем обработки автоклавного газобетона
[1] Г. Запоточна-Сытек, М. Собон, 60 лет бетона в Польше — прошлое и будущее, Материалы 5-й Международной конференции по автоклавному газобетону «Обеспечение устойчивого будущего», Быдгощ, (2011) 27-45.
[2] Бо Г. Хеллерс, Бо Р. Шмидт, Автоклавный газобетон (AAC) — история легкого материала, Материалы 5-й Международной конференции по автоклавному ячеистому бетону «Обеспечение устойчивого будущего», Быдгощ, (2011) 63-71 .
DOI: 10.1520 / c1693-09e01
[3] В.А.Мартыненко, Н.В. Морозова, Перспективы производства и применения газобетонных изделий в Украине, Строительные материалы. 5 (2009) 75-79.
[4] Джос Кокс.Продвижение, решения AAC для устойчивых проблем сужения в Европе, Материалы 5-й Международной конференции по автоклавному газобетону «Обеспечение устойчивого будущего», Быдгощ, (2011) 22-24.
[5] А.Семенов А.А. Перспективы развития строительного комплекса и отрасли строительных материалов в 2016 году, Строительные материалы. 1-2 (2016) 4-7.
[6] А.А. Вишневский, Г. Гринфельд, А. Смирнова, Российский рынок автоклавного газобетона. Итоги 2016 года, Строительные материалы. 3 (2017) 49-51.
[7] Н.П. Сажнев, Н. Сажнев, Н. Сажнева. Производство изделий из ячеистого бетона: теория и практика. Минск, (2010).
[8] М.Homann. Porenbeton-Handbuch, т. 6, BAUVERLAG-GÜTERSLOH (2008).
[9] Э. Юмашева, На Рефтинском объединении «Теплит» запущена новая линия по производству газобетонных блоков «Стройматериалы».3 (2019) 74-75.
[10] В.В. Бухмиров. Тепло и энергия. Иваново, (2014).
[11] Д.Рудченко, Г. Автоклавная обработка изделий из ячеистого бетона. Теория и практика от «Aeroc Internatoonal», Popular Concrete Studies. 3 (2007) 86-90.
АВТОМАТИЧЕСКАЯ ЛИНИЯ ПО ПРОИЗВОДСТВУ ПЕРИОДИЧЕСКИХ БЕТОННЫХ БЛОКОВ С ЗОЛЕНЫМ АГРЕГАТОМ. Производительность 50 м3 / смену
Технические характеристики линии
Вместимость | 50 м 3 / смену (100 м 3 / сутки) |
Потребляемая мощность | 54 кВт / ч (без водяного отопления) |
Использование воды | ~ 13 тн / смену |
Утилизация цемента | ~ 12,5 тн / смену |
Утилизация летучей золы | ~ 10,5 тн / смену |
Производство | мелкие стеновые блоки по ГОСТ 21520-89 |
Требуемая площадь производственного помещения | 500-1000 м 2 |
Высота потолка в зоне смешивания | не менее 6 м * |
Высота потолка в производственной зоне | не менее 3 м * |
Температура окружающей среды | не менее +15 o С |
Требуемый персонал | 6 рабочих, 1 начальник производства / прораб |
ПРЕИМУЩЕСТВА
Автоматизация управления процессами
На производственных линиях используются электронные системы для управления загрузкой и дозированием сырья в зоне смешивания.В системах управления предусмотрены функции регистрации и контроля сырья. Зона смешивания контролируется одним оператором. В зоне раскроя имеется отрезной станок, которым также управляет один оператор. Процесс демонтажа формы и укладки блоков автоматизирован.
Точность дозирования
Сырье подается на весы с тензодатчиками и весовым контроллером, который обеспечивает точное дозирование.
Высокая вместимость
Высокая производительность обеспечивается автоматизированной системой загрузки и дозирования сырья, а также высокой скоростью заполнения смесителя водой и сырьем.Высокопроизводительный отрезной станок обеспечивает высокую скорость резки монолита на блоки заданного размера.
Высокое качество
Система автоматизации процессов обеспечивает высокое качество продукции и гарантирует точность дозирования, а также стабильный и однородный состав, что позволяет нам выпускать качественную и конкурентоспособную продукцию.
СЫРЬЕ ДЛЯ ПРОИЗВОДСТВА ПЕТРОБЕТОНА
- Папка. Портландцемент ПЦ-500 Д0, ПЦ-400 Д20 ГОСТ 30515 и ГОСТ 10178 применяется в качестве вяжущего для газобетонных изделий.
- Кремнеземный компонент. Зола уноса применяется для ТЭЦ с содержанием SiO2 не менее 45%, CaO не более 10%, R2O не более 3%, SO3 не более 3%.
- Вода для замешивания. Вода соответствует требованиям ГОСТ 23732.
- Смазка для форм. Смазки для форм SDF или другие антиадгезионные агенты используются для обеспечения эффективного удаления плесени.
- Армирующие средства. Полипропиленовые волокна диаметром 12 мм используются в качестве армирующего агента.
- Модификаторы. ГОСТ 24211
- Газообразующие агенты. Алюминиевый порошок или пыль на его основе используются в качестве газообразующего агента.
ОБЗОР ПРОЦЕССА
1. Производство газобетонной смеси
Смеситель для наполнения водой
Для дозирования воды используется электронный водомер.Оператор зоны смешивания вводит необходимое количество воды и запускает цикл загрузки миксера.
Загрузка сырья в смеситель
Контроллер веса используется для загрузки сырья (цемент, летучая зола) в весы и реагентов в весы химических добавок. Цемент, летучая зола и примеси транспортируются шнековыми конвейерами. Цемент и летучая зола выгружаются из весов в смеситель. Раствор перемешивают 2–3 минуты до однородности.Когда раствор будет готов, в смеситель выгружают добавки и снова перемешивают газобетонную смесь в течение 1–2 минут.
Оператор контролирует все процессы в зоне смешивания в режиме реального времени. Оператор может использовать панель управления для корректировки или изменения рецепта, времени смешивания и других параметров процесса.
Оборудование поддерживает как ручной, так и автоматический режимы.
2. Монолитный багет
По готовности газобетонную смесь выгружают до 0.85 м 3 форма через смесительный клапан. Форма заполняется за один раз. Состоит из основы и съемных сменных бортов. Перед заполнением форма смазывается и транспортируется в зону смешивания для заполнения.
3. Отверждение монолита из пенобетона
Заполненная форма транспортируется по перилам в зону отверждения (в камеру термообработки), где монолит достигает своей прочности на отрыв. Заказчику рекомендуется устраивать герметичные туннельные камеры с полной теплоизоляцией по всем поверхностям.Температура в камере должна быть +30 … + 40 о С. Достижение прочности снятия изоляции может занять от 3 до 5 часов и зависит от плотности газобетона, активности, типа кремнезема, температуры и т. Д.
4. Демонтаж форм и вырезание массивов
После того, как массив наберет необходимую прочность, форма, содержащая массив, по железным дорогам переносится на демонтажную машину, основание формы фиксируется на пути. Затем четыре стенки формы снимаются и поднимаются захватом.После демонтажа формы основание формы и массив переносятся в секцию резки. Затем свободные стены накладываются на свободное основание, которое находится на прилегающей железной дороге. Форма в кожухе отправляется на участок разливки. Массив разрезают на блоки заданных размеров режущим агрегатом АРК-004. На участке резки находятся два отдельных последовательных модуля для вертикальной и горизонтальной резки массива.
Основание пресс-формы фиксируется захватом на вертикальном модуле, в то время как оператор запускает вертикальный модуль.Двигаясь по направляющим, модуль разрезает массив в вертикальной плоскости и обрезает его с обоих концов. После вертикальной резки опалубка с массивом переносится в зону горизонтального модуля, фиксируется захватом, после чего разрезается в горизонтальной плоскости на блоки заданных размеров, а также нижний слой и верх срезан. Пока горизонтальный модуль работает, следующий массив подается в зону вертикального модуля. Таким образом, одновременно производится резка двух массивов, что обеспечивает высокую пропускную способность линии.
5. Укладка блоков на поддоны, упаковка и хранение
Опалубка с вырезанным массивом переносится в блок штабелирования блоков. Основание пресс-формы закреплено на рельсе. Затем половину среза массива с помощью захвата укладывают на поддон. Для комплектации поддона вручную устанавливаются восемь блоков. Затем укладывается вторая половина массива, а также восемь блоков вручную (в зависимости от их размеров).Поддон с блоками обматывают стрейч-пленкой.
6. Блок термовлагообработки
В зависимости от климатической зоны и типа производимого материала блоки, уложенные на поддоны, могут набирать марочную прочность на складе готовой продукции или при термовлагообработке. Для ускорения набора прочности блоков необходима термовлагообработка блоков. При термовлагообработке блоки выдерживаются в камере от 8 до 12 часов при температуре от +40 до 60оС.Режим термовлагообработки также зависит от плотности материала, активности цемента и определяется заказчиком для каждого конкретного вида выпускаемой продукции.
7. Утилизация отходов резки
Режущие модули вырезают монолит с обоих концов, вверху и внизу. Инновационным решением является использование измельчителя отходов ДГ-1 для переработки отходов резки. Позволяет измельчать отходы газобетона до частиц размером до 0–30 мм.Грунт может быть использован как сыпучий утеплитель для крыш, чердаков, пола и т. Д. Измельчитель делает производство бетона практически безотходным.
ТЕХНИЧЕСКИЕ ХАРАКТЕРИСТИКИ ЛИНИЙ
N | Имя | Количество |
Участок хранения, подготовки и отгрузки сырья | ||
1 | Шнековый транспортер цемента (L = 6 м *, мотор-редуктор (Италия), N = 4 кВт) | 1 |
2 | Шнековый транспортер летучей золы (L = 6 м *, мотор-редуктор (Италия), N = 4 кВт) | 1 |
Зона смешивания | ||
1 | Электронная система управления (со встроенным водосчетчиком + подкачивающим насосом) | 1 |
2 | Весовой дозатор (тензодатчики, пневмоклапан, макс.600 кг) | 1 |
3 | Дозатор химических добавок ДХД-1 (N = 0,5 кВт) | 1 |
4 | Смеситель для газобетона ГБ-0.85 (N = 11 кВт, V = 0,85 м3 3 ) | 1 |
5 | Компрессор C200LB40 (500 л / мин, 8–10 атм.) | 1 |
Участок резки монолита | ||
1 | Автомат раскройный АРК-004 (Н-19.5 кВт) | 1 |
2 | ФМ-0,91 м 3 опалубка для монолита из газобетона (V = 0,91 м 3 ). | 55 |
3 | Транспортная тележка | 4 |
4 | Комплекс для демонтажа форм (N = 2,0 кВт) | 1 |
5 | Комплекс для укладки блоков на поддоны (N = 2.5 кВт) | 1 |
Зона измельчения стружки | ||
1 | Измельчитель ДГ-1 (N = 4,5 кВт) | 1 |
РАСХОД МАТЕРИАЛА * НА 1 м
3 ИЗ НЕАУТОКЛАВИРОВАННОГО ПЕРИОДИЧЕСКОГО БЕТОНА D-600Материал | Количество |
Цемент (ПЦ500 Д0), кг | 250 |
Летучая зола, кг | 210 |
Вода, л | 250 |
Газообразующий агент, кг | 0,5-1,5 |
Клетчатка, кг | 0,6 |
Химические добавки, кг | ** |
* Рецепты корректируются с учетом свойств сырья, выбранного заказчиком.
** Тип и количество добавок определяется на этапе проектирования бетона.
ОБЩАЯ ИНФОРМАЦИЯ
Для снижения затрат заказчика линия поставляется без силоса для цемента, бункера для песка и перил для транспортировки форм. Заказчику предоставляются чертежи раздельного изготовления этих узлов.
Кроме того, заказчик несет ответственность за подогрев воды до +35 … + 40 ° C и устройство камер пропаривания.Для работы линии в 2 смены необходимы дополнительные опалубки.
Гарантийный срок на поставляемое оборудование — 12 месяцев. Компоненты каждой единицы оборудования указаны в контракте, паспорте оборудования и акте приема-передачи.
Специалисты ООО «Сибирские строительные технологии» (СКТ) разрабатывают компоновку оборудования на производственном объекте заказчика. Установка оборудования согласно схеме осуществляется заказчиком и за его счет.Заказчику предоставляется схема (чертежи) оборудования соответствующих помещений и подробная иллюстрированная инструкция по установке.
После того, как заказчик завершит установку и подключение оборудования, SCT выполняет следующие работы:
• пуско-наладка оборудования;• конструкция из газобетона;
• оптимизация технологии производства;
• обучение персонала заказчика.
Заказчик несет ответственность за соблюдение всех правил техники безопасности, требований по охране труда и окружающей среды, а также других местных нормативных актов.
Все расходы по транспортировке и размещению персонала SCT на период проведения работ берет на себя заказчик. Оптимизация технологии включает оптимизацию состава бетона на основе сырья, предоставленного заказчиком. SCT предоставляет услуги поддержки.
После ввода оборудования в эксплуатацию заказчику предоставляется техническая документация, в том числе:
• технический регламент на производства;• Диаграмма процесса;
• описание вакансии;
• Инструкции по технике безопасности;
• ГОСТы.